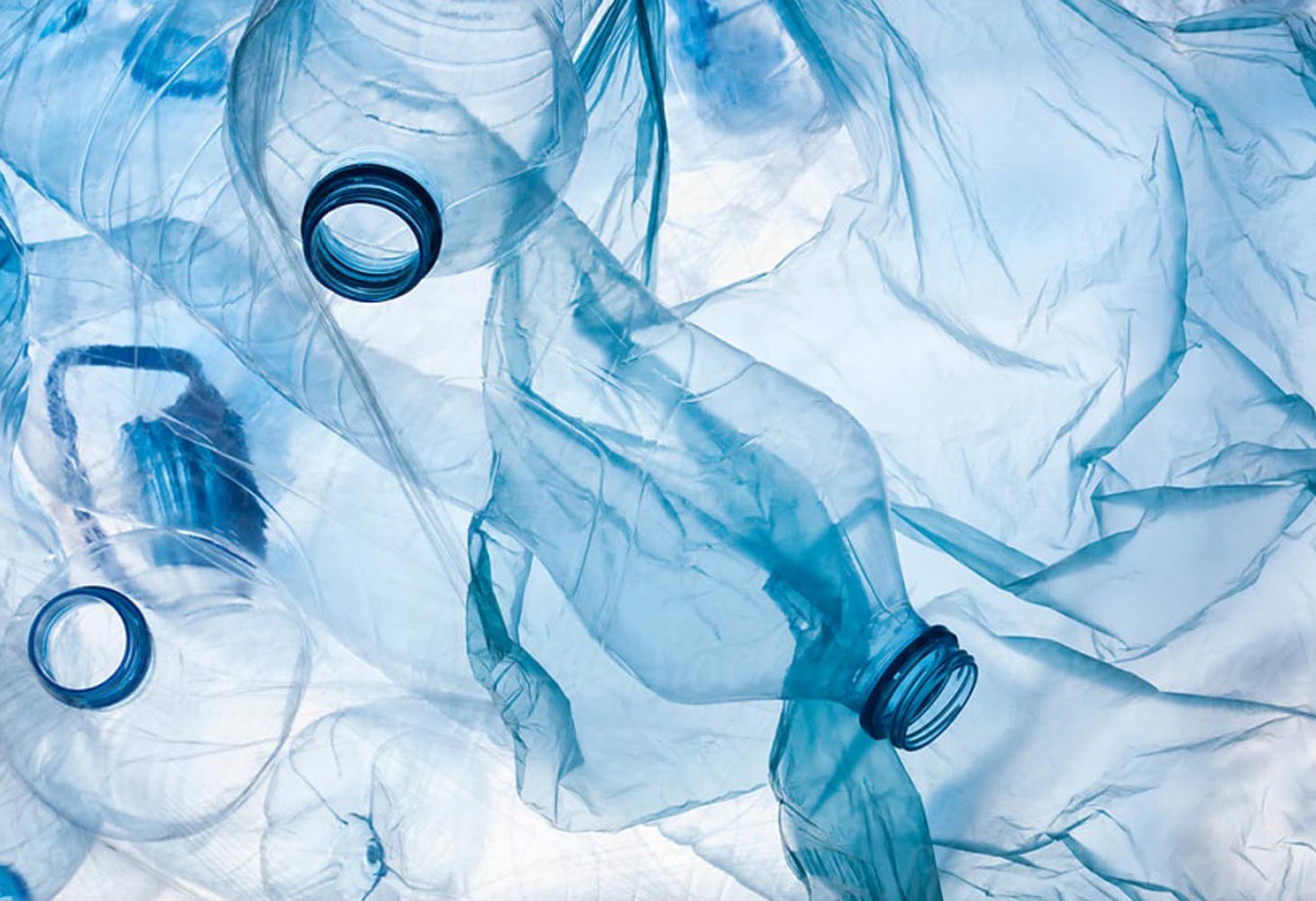
Neste joins forces with Mitsui Chemicals and Toyota Tsusho
Neste, Mitsui Chemicals, Inc. and Toyota Tsusho Corp. are joining forces to enable Japan’s first industrial-scale production of renewable plastics and chemicals from 100% bio-based hydrocarbons.
In this collaboration, Mitsui Chemicals will use Neste RE™, 100% bio-based hydrocarbons produced by Neste, to replace a part of the fossil feedstock in the production of a variety of plastics and chemicals at its crackers within Osaka Works during 2021. In doing so, Mitsui Chemicals will become Japan’s first company to use bio-based feedstock in its crackers. The collaboration between Neste, Mitsui Chemicals and Toyota Tsusho will enable brand owners and other potential clients in the Asian market, particularly in Japan, to start incorporating renewable plastics and chemicals into their products and offerings.
For this collaboration, Finland’s Neste will produce its Neste RE feedstock entirely from renewable raw materials, such as bio-based waste and residue oils, without any fossil oil. By using Neste RE, Mitsui Chemicals is able to produce plastics and chemicals with significantly reduced greenhouse gas emissions over their life cycle—spanning from the raw materials stage all the way through to product disposal—when compared to products made using fossil feedstock, such as petroleum naphtha.
Derivatives retain the same quality as petroleum-based products
The introduction of Neste-produced bio-based hydrocarbons as feedstock at the crackers will allow Mitsui Chemicals to produce renewable ethylene, propylene, C4 fraction and benzene, among others, and process them into basic chemicals such as phenol, or plastics such as polyethylene and polypropylene, without altering the high-quality of these derivatives; the quality will be on par with conventional products.
Mitsui Chemicals and Toyota Tsusho intend to acquire International Sustainability and Carbon Certification (ISCC), which is widely accepted in Europe as a system for the certification of products from bio-based feedstock. Mass balance-based ISCC Plus certification aims at driving up adoption of renewable content even in supply chains that feature complex production processes, such as those common in the chemical industry.
“Aiming to reach carbon neutrality by 2050, Mitsui Chemicals is looking to help bring about a circular economy by pursuing the two pillars of recycling and the use of bio-based alternatives for its chemical and plastic products,” said Hirahara Akio, managing executive officer for Corporate Sustainability at Mitsui Chemicals. “Switching fossil feedstock to bio-based feedstock helps combat global warming, and it is regarded as an important strategic focus in the push for reaching carbon neutrality by 2050. With this in mind, Mitsui Chemicals will not only go about developing materials from high-quality bio-based feedstock and processes but also work with stakeholders toward getting biomass widely used in society.”
“Bringing sustainable plastics and chemicals to the market can only be successful if all value chain parties closely collaborate. We are therefore very excited about our partnership with Mitsui Chemicals and Toyota Tsusho, two industry leaders with whom we will start Japan’s first ever production of high-quality, high-performance plastics, from 100% bio-based Neste RE. Through this collaboration, we can considerably reduce emissions related to the use of fossil feedstocks and help Japan to reach its national climate and polymers-related bio-content targets, fully in line with Neste’s purpose and drive towards a circular bioeconomy,” says Mercedes Alonso, executive vice president, Renewable Polymers and Chemicals, Neste.
“We are so excited that our decade-long experience brings our plastics market one of the best circular economy solutions from upstream to downstream,” says Kazuyuki Urata, COO for Chemicals & Electronics Division of Toyota Tsusho. “This project is very much aligned to support progress in the material sustainability issues identified for our company.”