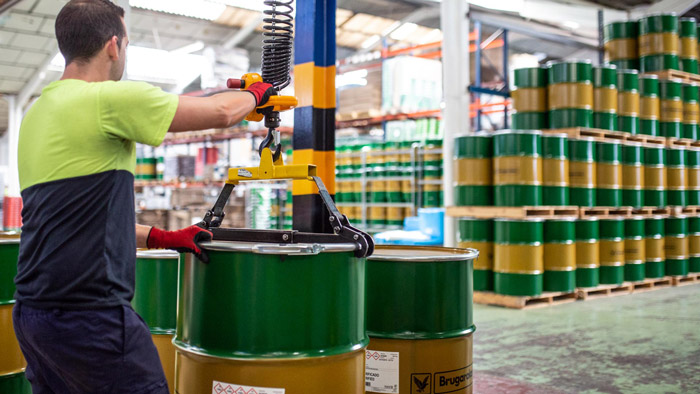
Lubes and Base Oils: SK Innovation, BASF, Brugarolas, Schaeffler India
South Korea’s SK Innovation says it can produce Group III+ base oils from plastic wastes
South Korea’s SK Innovation said it has successfully produced solvents and lubricating base oils from plastic wastes through chemical recycling. With chemical recycling, fossil resources for chemical production can be replaced with recycled material from plastic waste, transforming the plastic waste into secondary raw materials, such as pyrolysis oil.
Solvents are used for detergents, paint thinners and chemical synthesis. Base oils are a key raw material in producing finished lubricants.
“SK Innovation, which faces environmental issues such as plastic waste, needs to transform its chemical business into a new one completely and must seek intrinsic changes to become a company that stands out in terms of ESG,” President and CEO of SK Global Chemical Na Kyung-soo said. SKGC, which is leading the project, is a chemical subsidiary of SK Group.
“The solvent made with plastic wastes demonstrated a high ratio of paraffin and a low odor compared to existing solvent products. Also, the lube base oil showed enough quality to make premium Group III+ base oils categorised by American Petroleum Institute,” a representative from SK Innovation was quoted as saying.
The move is part of SK Group’s Green Balance initiative to boost the company’s environmental, social and corporate governance.
Chemical recycling is becoming the preferred approach to recycle plastic waste, as mechanical recycling is limited due to high sorting requirements and decreasing material quality in each cycle.
Last month, Germany’s BASF SE invested EUR16 million (USD18.8 million) into Pyrum Innovations AG, a technology company specialised in the pyrolysis of waste tires, headquartered in Dillingen/Saar, Germany. With the investment, BASF will support the expansion of Pyrum’s pyrolysis plant in Dillingen and the further roll out of the technology. Pyrum is currently running a pyrolysis plant for end-of-life tires that can process up to 10,000 tons of tires per year. Until the end of 2022, two additional production lines will be added to the existing plant. Furthermore, Pyrum intends to build additional tire pyrolysis plants together with interested partners. The collaborative set-up will accelerate the path towards the use of Pyrum’s unique technology in serial production.
BASF will uptake most of the pyrolysis oil and process it into new chemical products by using a mass balance approach as part of its ChemCyclingTM project. The resulting products will mainly be for customers from the plastics industry who are looking for high-quality and functional plastics based on recycled materials.
Additionally, BASF SE signed an uptake supply agreement in early September with New Energy, a technology company specialised in the pyrolysis of waste tires, headquartered in Budapest, Hungary. According to the agreement, New Energy will supply BASF with up to 4,000 metric tons of pyrolysis oil per year derived from waste tires. In a pilot phase, first volumes of the pyrolysis oil have already been utilized successfully in BASF’s integrated chemical production site (Verbund) in Ludwigshafen, Germany.
Spain’s Brugarolas completes facility upgrade
Spanish lubricant manufacturer Brugarolas announced the completion of a new warehouse next to its lubricant blending plant located in the town of Rubí, 26 kilometres from the city of Barcelona. The lube blending plant has a capacity of 50,000 tonnes per year.
The new warehouse represents a significant improvement, with a floor area of 12,000 m2 in three floors managed by four forklifts. Brugarolas has also expanded its loading docks from one to four, thus quadrupling the plant’s simultaneous truck loading capacity.
In addition, Brugarolas has installed solar panels on the roof of the new warehouse, which will generate more than 45% of the factory’s total energy consumption. On an annual basis, the photovoltaic installation will provide the factory with energy equivalent to the consumption of more than 80 homes, which is equivalent to more than 50 tons of oil.
Brugarolas’ goal is to achieve net zero greenhouse gas emissions by 2050.
Schaeffler India launches TruPower lubricants
Schaeffler India has launched a new lubricant product line under the Schaeffler TruPower brand. The product line includes a complete range of engine oils, transmission oils, greases, coolants, hydraulic oils and shock absorber oils.
Schaeffler TruPower lubricants are now available in various convenient sizes at authorised distributors across India. The comprehensive range of lubricants is formulated to maximise the efficiency, performance and longevity of petrol and diesel engines.
“We find lubricant is a perfect value addition for our installers who are already using our transmission, engine and chassis products. Our program is extensive in range and covers updated specifications including those of the latest BS VI range,” said Debasish Satpathy, vice-president, Automotive Aftermarket, Schaeffler.
“Quality oil was our priority; thus, the lubricants have been formulated and developed using the same expertise which goes into manufacturing of our known and trusted brands – LuK, INA and FAG. The new lubricant will give vehicle owners great peace of mind and comfort while driving on city roads, national highways, rural farms or mine roads.”
Ball and roller bearing manufacturer Schaeffler has four plants and 11 sales offices in India producing three major product brands – FAG, INA and LuK. The manufacturing plant in Vadodara, Gujarat was set up in 1964 and produces a vast range of ball bearings, cylindrical roller bearings, and spherical roller bearing and wheel bearings and sold under the brand name of FAG. The second plant in Vadodara at Savli produces next generation deep groove ball bearings and large size roller bearings also sold under the name of FAG. Schaeffler’s third state-of-the-art plant is located at Talegaon near Pune, and manufactures engine and transmission components for front accessory drive system, chain drive systems, valve train, shift systems and a range of needle roller bearings and elements, under the brand INA. The fourth manufacturing location is based out of Hosur, producing clutch systems and dual mass flywheels for passenger cars, light commercial vehicles, heavy commercial vehicles and tractors which are sold under the brand of LuK. In addition, Schaeffler also has dedicated engineering, research and development support based in India to augment the product teams. Schaeffler also has among the largest after-market networks serving the industrial and automotive markets.