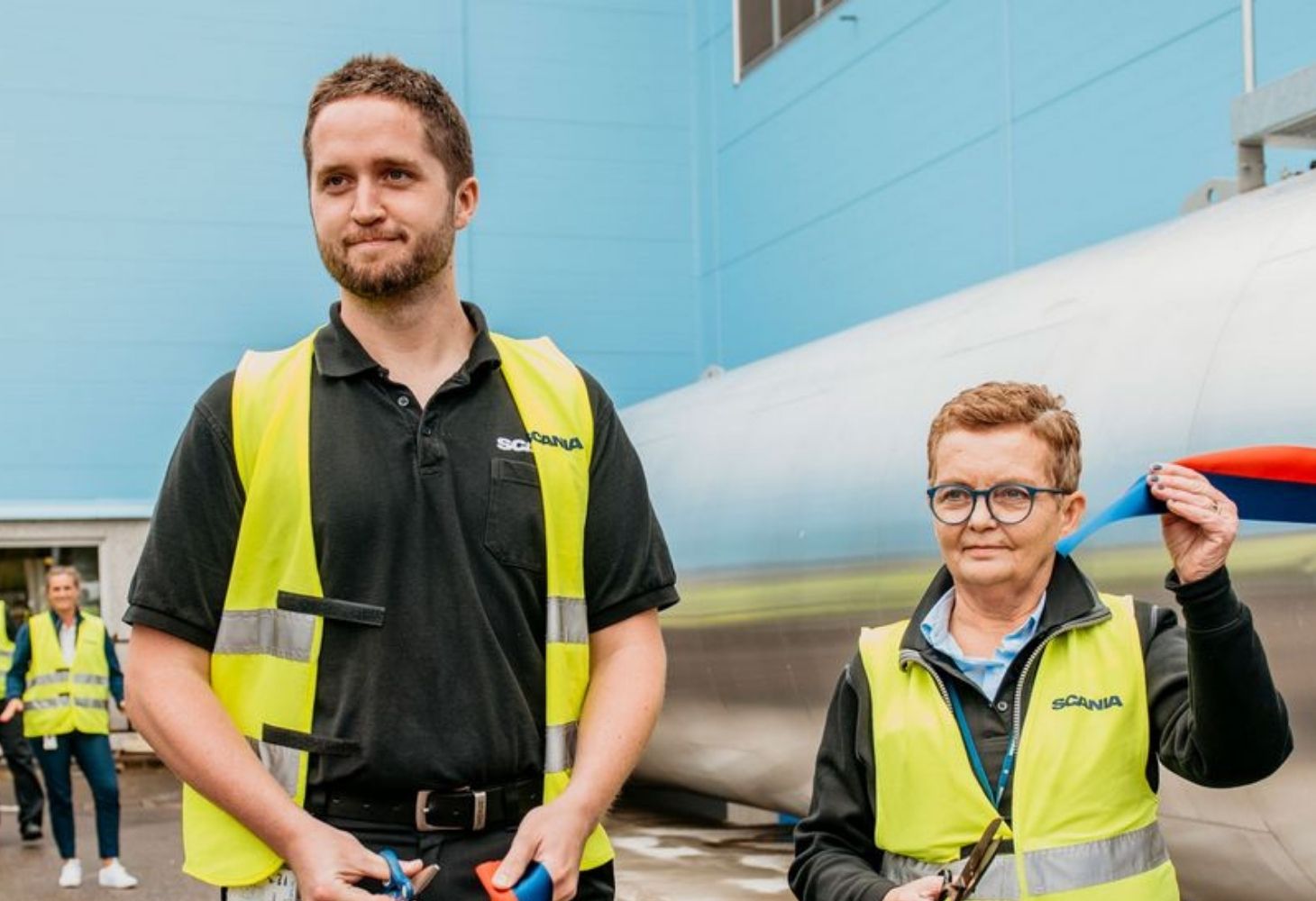
Scania’s Oskarshamn plant to be completely fossil free by 2021
Scania’s cab production plant in Oskarshamn, Sweden, will become fully fossil free by 2021, becoming the first of its major production plants around the world to successfully phase out carbon emitting production elements.
Scania has made a firm commitment, in line with the Science Based Target initiative, to halve its own carbon emissions by 2025, with 2015 as the baseline year. Additionally, Scania will reduce carbon emissions from the use of its products by 20% by 2025.
Concerted efforts are now in progress to reach the target and the Oskarshamn plant is not only first to cross the finish line. It expects to exceed the set target.
“This is a major step, not only for us here in Oskarshamn but for Scania as a whole. And we’re glad that we’ve been able to contribute to the target,” says Scania’s Oskarshamn Plant Manager Roger Blezell.
The Oskarshamn plant annually manufactures approximately 70,000 cabs, primarily for Scania’s European assembly plants in France, the Netherlands and Sweden. The highly automated process consists of five steps: pressing, bodywork, primer painting, topcoat painting and assembly.
The largest contribution to reducing carbon emissions has been to convert the three ovens – water drying, powder and seam sealing – for the primer painting process from fossil diesel to the biofuel RME (rapeseed methyl ester). That alone reduced Oskarshamn’s climate impact by 60%.
The final major step has been to also power ovens for the topcoat painting process by RME. Meanwhile the last diesel-powered forklifts have been phased out in favour of electric propulsion and those internal transport vehicles that were previously operated on fossil diesel switched to an on-site supply of the renewable biofuel HVO (hydrotreated vegetable oil).
“The greatest challenge with the RME project was to obtain cost-neutrality,” says Oskarshamn’s Sustainability Manager Pernilla Zackrisson. “Normally, what’s good for the environment is also good for your wallet but in this case it’s more expensive. Despite that, we’ve chosen to implement the project and instead recover the added cost through other energy-saving measures and higher productivity.”