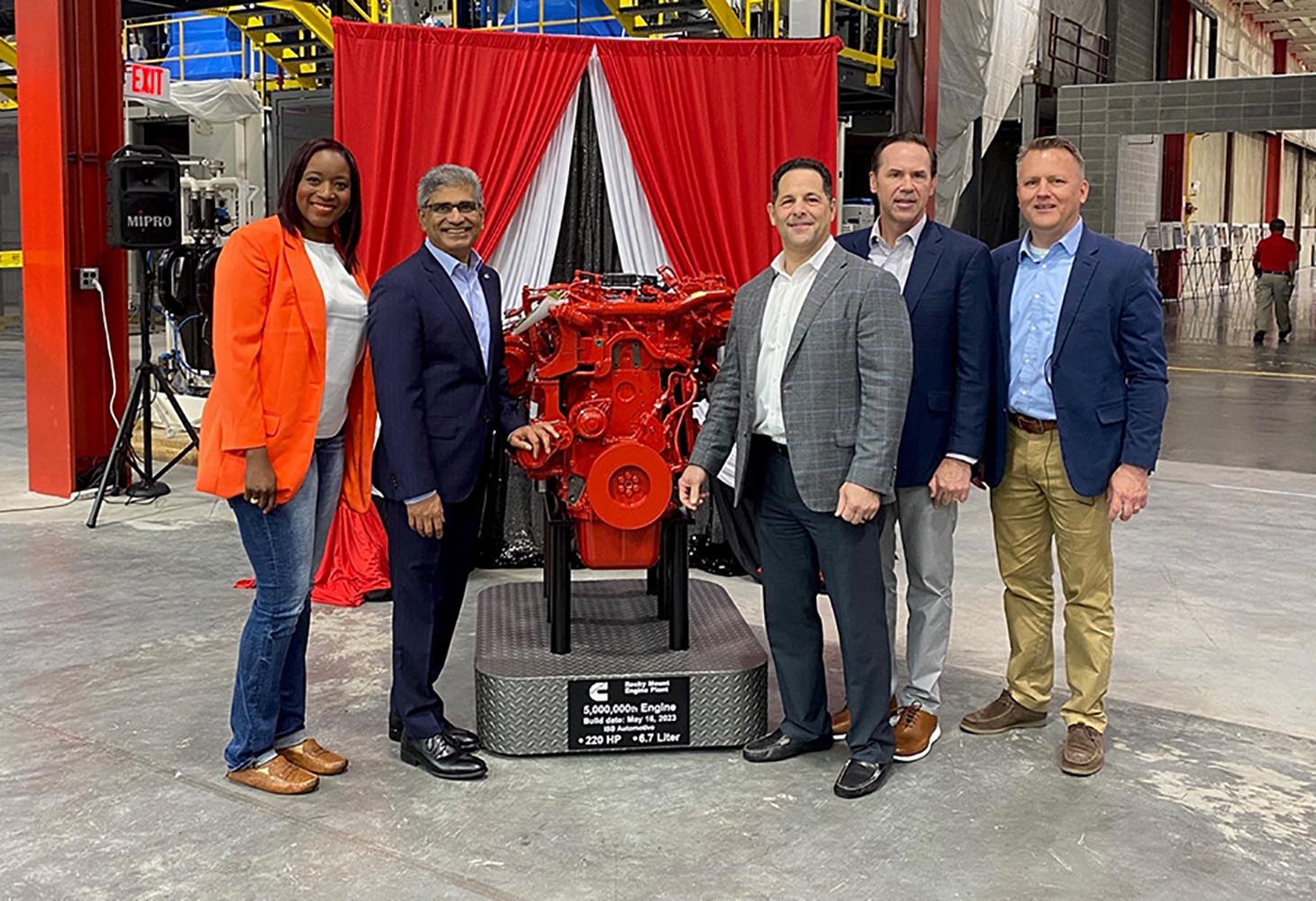
Cummins celebrates 5 millionth engine produced at Rocky Mount Plant
Cummins Inc., based in Columbus, Indiana, U.S.A., announced the 5 millionth engine produced at its Rocky Mount Engine Plant (RMEP) along with its 2.5 millionth engine produced at its Jamestown Engine Plant (JEP).
RMEP is the first Cummins plant to reach five million engines produced, recording more than one million additional engines produced than any other Cummins engine facility.
As the global power technology leader continues to pave a path to a more sustainable future for its products throughout the world, these milestone events are remarkable achievements, the company acknowledged.
RMEP produces the B6.7 and L9 used by Daimler Truck North America and Penske, among other engines for various original equipment manufacturers (OEMs) and applications, including pick-up and delivery, vocational trucks and school buses. The 5 millionth milestone engine is a B6.7, which will be received by Daimler, who will provide it to Penske.
“Rocky Mount Engine Plant has been important to Cummins for more than 40 years, and as we celebrate production of the 5 millionth engine, we know the plant—and our employees here—will continue to play a significant role as Cummins moves ahead with our Destination Zero strategy and our future fuel agnostic platform,” said Steve Pinkston, Cummins Rocky Mount Engine plant manager.
“We’re excited about the improvements to existing manufacturing technology at Rocky Mount Engine Plant and introducing new fuel agnostic technologies in markets and applications in line with our Destination Zero strategy. We are looking forward to RMEP manufacturing today’s technology and these future products as they launch.”
Jamestown delivers 2.5 millionth engine
The company is also celebrating JEP’s 2.5 millionth engine, which is an X15. Kenworth will be the recipient of the milestone engine, who will install it in the iconic Legacy W900 truck and provide the truck to Palmer Kenworth. Kenworth is celebrating their 100th anniversary and has been operating since 1923.
In addition to celebrating these milestones, Cummins is investing USD452 million into the 998,000 square foot Jamestown facility, to produce the industry’s first fuel-agnostic internal combustion engine platform that leverages a range of lower carbon fuel types, including natural gas, and is aligned with the company’s Destination Zero strategy. This investment is intended to retain the thousands of current engineering and manufacturing jobs and support the creation of new jobs as Cummins invests its people and facilities to grow innovation and accelerate decarbonization efforts.
Over half of all medium- and heavy-duty trucks on the road in the U.S. today use Cummins engines and the X15N is part of the new fuel-agnostic 15-liter engine platform that will be produced at JEP. This next generation engine is the first natural gas engine to be specifically designed for heavy-duty truck applications with up to 500 horsepower output and is a key step for the future of heavy-duty transportation fleets and a road to zero emissions, said Cummins.
“Our plant wouldn’t be successful without the dedicated employees who serve our company and community each day,” said Anna Dibble, Cummins Jamestown Engine plant manager. “We are proud to have such a strong presence in the community and be able to create a welcoming, caring and all-inclusive environment for our people to be successful.”
JEP is a critical piece of Cummins long-term Destination Zero strategy and next generation engine portfolio and remains one of the company’s largest manufacturing facilities. The facility has been operating for 49 years and has more than 1,500 employees and serves 1,949 active customers. JEP continues to be the largest private employer in Chautauqua County and the southern tier of New York.
About the fuel-agnostic platform
The new fuel-agnostic engine platforms feature a series of engine versions that are derived from a common base engine, which means they have a high degree of parts commonality. Below the head gasket of each engine will largely have similar components and above the head gasket will have different components for different fuel types. Each engine version will operate using a different, single fuel. This new design approach will be applied across the company’s legendary engine portfolios including the REM’s B6.7 and the X15, and the new 10-liter portfolio called the X10.
Srikanth Padmanabhan, vice president and president, Cummins Engine Business, shares his views and expertise on the future about the fuel-agnostic platform: “Our employees are innovating to find new ways of working that use fewer of the world’s resources, and the Engine Business is at the center of this exciting innovation. Our fuel agnostic platform builds on decades of experience manufacturing industry-leading products. It is essential to our commitment to help customers reduce greenhouse gas emissions.”