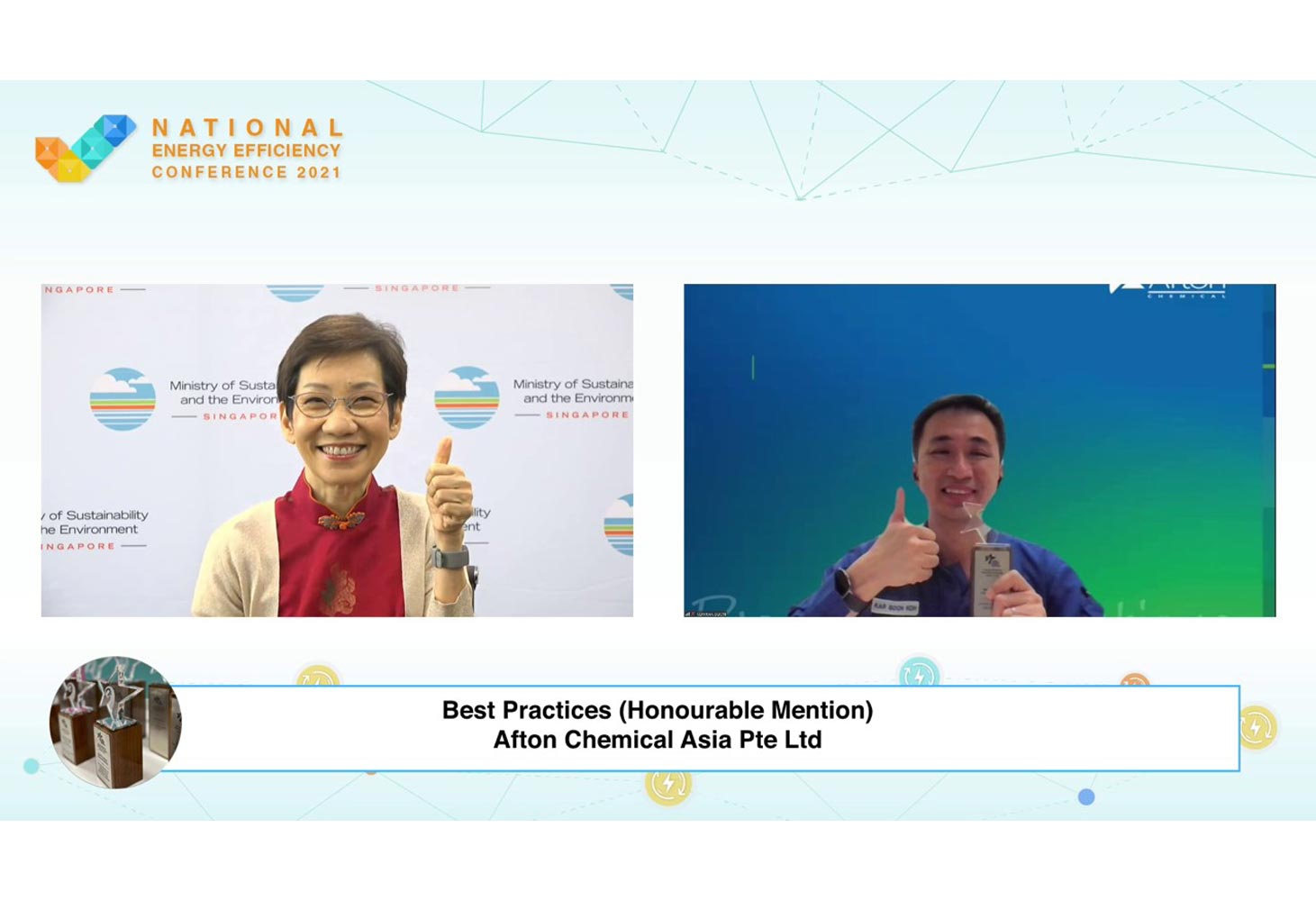
Afton recognized for best practices in energy efficiency
Afton Chemical Asia was recognized by Singapore’s National Environment Agency (NEA) recently for the air compression energy reduction project at its Singapore additive manufacturing facility. The U.S.-based global additive company received honourable mention for Best Practices in the Energy Efficiency National Partnership Awards 2021.
The EENP Awards has been organized annually since 2011 by the National Environment Agency, Energy Market Authority and the Singapore Economic Development Board to recognize EENP Partners for their efforts and achievements in improving energy efficiency. The EENP Awards aim to foster a culture of sustained energy efficiency improvement in the industry and encourage companies to adopt a proactive approach towards energy management.
Air compressor energy reduction project
The air compressor energy reduction project was initiated as part of the company’s energy reduction projects aimed at improving energy efficiency and minimizing waste in the Singapore additive facility. Senior Production Engineer, Koh Kar Boon, and Maintenance Supervisor, Kumar Varadharajan, identified that the batch production nature of the facility with varying start/stop timing for three production units resulted in un-even utilization of compressed air during power handling.
The team studied the pattern of header pressure changes and air compressor performance to get a better understanding of the facility’s air consumption. Surge line modelling was used to calculate a varying throttle limit for the compressor and build in last stage pressure against surges. The compressor sequence was also adjusted to adapt the header pressure changes and coasting time.
A key challenge was to maintain the stable air supply to the three different production units. Compressor capacity control tuning was done with the help of the OEM team. After the adjustments, only one compressor out of three was required to keep the facility running. A second compressor starts only occasionally to maintain the header pressure when one compressor cannot meet the demand.
“Our energy efficiency efforts have not only reaped cost savings, but it also means improved equipment reliability and increased equipment availability. Actual annual energy savings on a system level is 34.2% and 3.2% on a facility level with no CAPEX outlay,” says Kew Jin Woon, plant manager, Afton Chemical Asia.
Energy efficiency is one of key metrics
“At Afton Chemical, environmental responsibility is built into our Think Lean/Efficient culture which is an integral part of the way we manufacture and do business. Energy efficiency is one of the key metrics that we are always striving to improve on for our equipment and systems. Besides the air compressor energy reduction project, we are concurrently working on hot oil heater operation optimization, process chiller running optimization, tank recirculation pump optimization etc.,” says Jin Woon.
Afton Chemical is also a founding member of Responsible Care under American Chemistry Council (ACC) that helps improve health safety and the environment globally. As members of the ACC, Afton Chemical provides data on 12 sustainability metrics used to track environmental impact, safety and energy use.