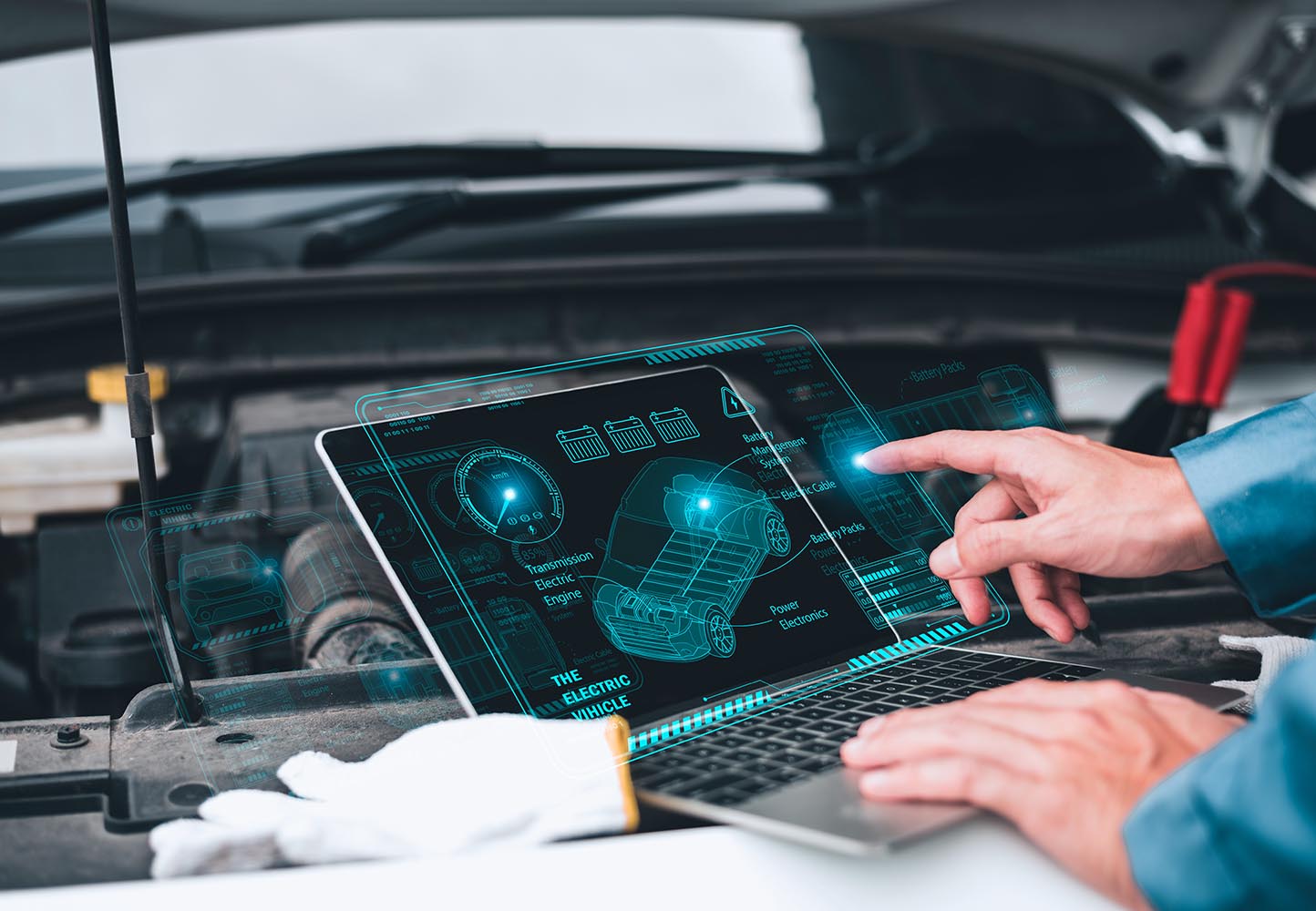
Tier 1 supplier says significant gaps still exist in EV test methods
American Axle & Manufacturing, Inc., commonly known as AAM, is a leading global Tier 1 automotive supplier, which means it is involved in the development, production, and supply of major vehicle components or systems. Formed in 1994 following the divestiture of General Motors’ (GM) axle and forge businesses, the company specialises in the design, engineering, and manufacturing of driveline systems, drivetrain components, and related modules and systems. As such, AAM is uniquely positioned to understand the overarching industry trends in electric vehicles (EV), as well as the difficulties associated with electric driveline fluids.
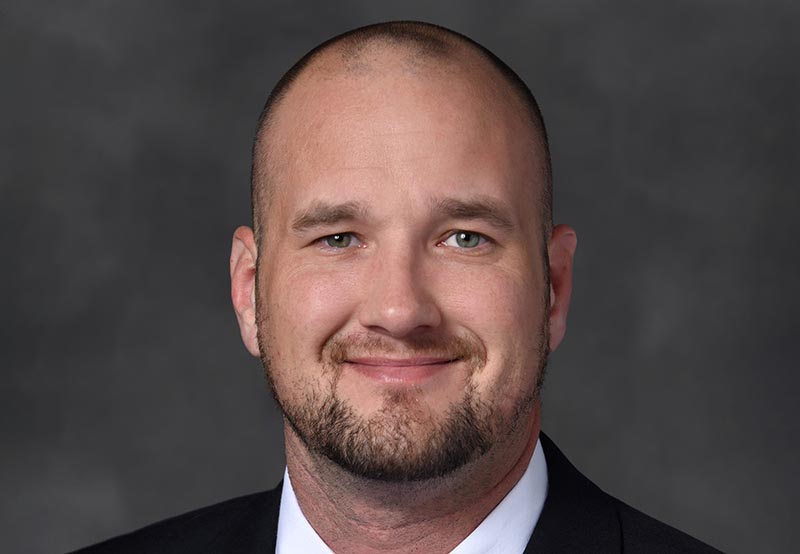
The 2023 STLE Tribology & Lubrication for E-Mobility Conference was held in Cleveland, Ohio, U.S.A., on November 14-15, 2023. During the meeting, Troy Muransky, lead organic materials engineer at AAM, provided a perspective on the Challenges of Selecting the Correct Electric Vehicle Driveline Fluid. In his presentation, Muransky highlighted a lack of proven test methods to validate the new properties required for EV fluids.
Muransky has 17 years of experience in the automotive industry in diverse roles spanning materials, processes, environmental engineering, analytical chemistry and laboratory management. He is an active member of ASTM, SAE and STLE and is the current chairman of ASTM D7452, Standard Test Method for Evaluation of the Load Carrying Properties of Lubricants Used for Final Drive Axles, Under Conditions of High Speed and Shock Loading. This test method is commonly referred to as the L-42 test.
During his presentation, Muransky outlined the various EV architectures and a broad range of components in the ever-changing world of electrification. The “biggest thing” for the industry is extending vehicle range and enabling faster charging, he says. This pursuit is encouraging advanced hardware designs—including the development of compact, high-power-density electric drive units (EDUs) with motor shaft speeds of 25,000 revolutions per minute (rpm) and beyond. Increasing battery voltages, higher local and system temperatures, and heightened stresses on gearing and bearings are key challenges as automakers aim for greater efficiency.
The latest hardware trends require fluids to lubricate the gearbox while also cooling the motor and inverter. These evolving needs are encouraging new chemistries and unique fluid formulations. Headline lubrication requirements include minimising friction—to aid durability and maximise efficiency, thermal management, corrosion protection and ensuring flowability and pumpability at cold temperatures. While this may seem relatively straightforward, there are many additional considerations, says Muransky.
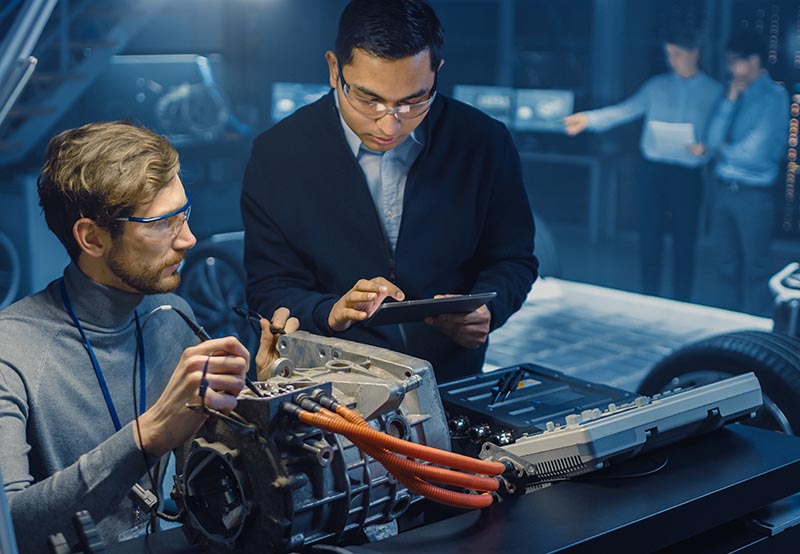
Muransky emphasised the need to maximise efficiency at high rotational speeds and torques while protecting gears and bearings. There is a need for increased extreme pressure and anti-wear chemistries, and alternative chemistries must be compatible with copper, he says. Oxidative stability properties need to be optimised to temperatures exceeding 180 degrees Celsius, which may require the inclusion of non-electrically conductive detergents to minimise sludge and deposits, he says. New chemistries also need to encourage entrained and dissolved air release, while limiting foaming.
The AAM representative’s laundry list of requirements also included amplifying the fluid’s heat transfer properties to address heat generated by both electronics and friction. Dielectric strength and oil-separation time must be maximised, and the fluids need to optimise flash points, electrical arc points and autoignition to prevent thermal events.
Ensuring material compatibility is a crucial factor in the lubrication of EVs. Muransky emphasised the need to consider rubbers, adhesives, sealants, plastics and copper impacts. He also stressed the importance of maintaining a two-year plus shelf life, with maximum chemistry and storage stability. Because of these new, unique requirements, driveline fluid selection can be very difficult, he says.
Which fluid should you select? Previous EV designs have principally used automatic transmission fluids (ATFs), says Muransky, which were generally adopted in dry motor systems. ATFs have the benefit of well-established industry standards and test methods to ensure they meet individual OEM requirements.
However, electric mobility is an evolving landscape, and the superfluity of unique, compact designs with higher power densities demands more from fluids. Electric drive fluid (EDF) is not an off-the-shelf product, says Muransky. Bespoke fluids must be developed for each design. Nonetheless, there is an absence of test methods to validate new properties and nor are their impacts completely understood, he says. In his keynote, Muransky provided a hardware supplier’s perspective on the testing gaps associated with individual lubricant properties.
In terms of lubrication, established test methods cannot effectively mimic EDU challenges around high speeds, aeration, electric currents or electric & magnetic (E&M) fields. The AAM representative also indicated that gearing and bearing software and models have accuracy concerns, especially when combined.
Concerns around the modelling of heat transfer properties were also raised, with precision issues in current Computational Fluid Dynamics (CFD) software noted. Muransky called for new test methods to address EDU challenges around dissolved air, entrained air, bubble sizes, foaming, sludge/deposits and restricted flow.
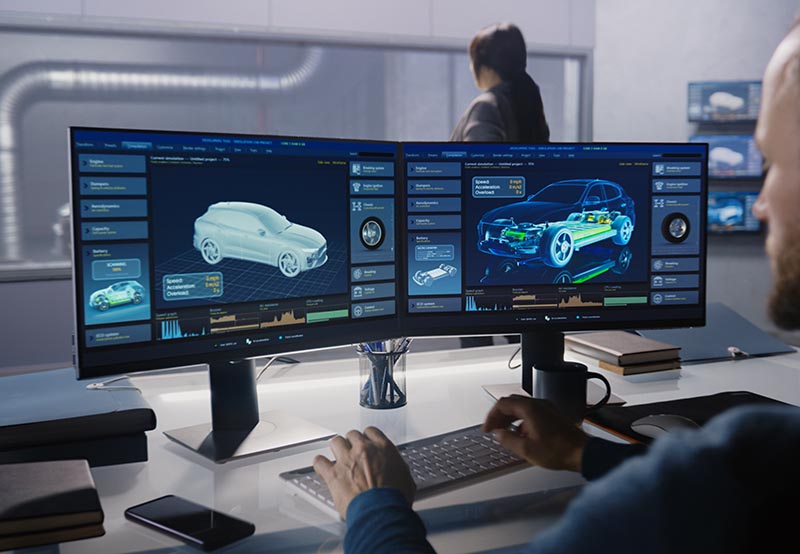
There is an absence of proven industry test methods for dielectric testing to evaluate high aeration impact or other dielectric strength degrading over time, says Muransky. Although electrical conductivity changes can be measured by ASTM D1169 (IEC 60247) after the addition of water and the fluid has been artificially aged. Standards do not exist to artificially create wear metals and copper content leached from exposed copper, he says.
ASTM is in the process of releasing a method for conductive sludge generation to address a known evaluation gap, however, there is no proven method for oil/water separation time and impact for conductivity during re-mixing, says Muransky.
In his presentation, Muransky emphasised the difficulty of measuring aeration in real-time, despite new technology offering some options. Quantifying bubble size, dissolved and entrained air volumes remains problematic. Muransky called for the creation of an introduction method to mimic what is evident in the hardware.
Finally, Muransky highlighted testing gaps in copper compatibility. There is a need for a comprehensive pass/fail test that evaluates liquid and vapour phase impacts on fluid and copper, he says. The test needs to address electrical current, high aeration, 150+°C temperatures, with extended durations—such as 1,008 hours. He also noted the importance of post-fluid analysis such as a post-FZG test (used to evaluate gear scuffing), total acid number (TAN), thermal transfer, and electrical conductivity. Additionally, Muransky discussed the misconception that soluble copper content (ICP) indicates fluid aggressiveness.