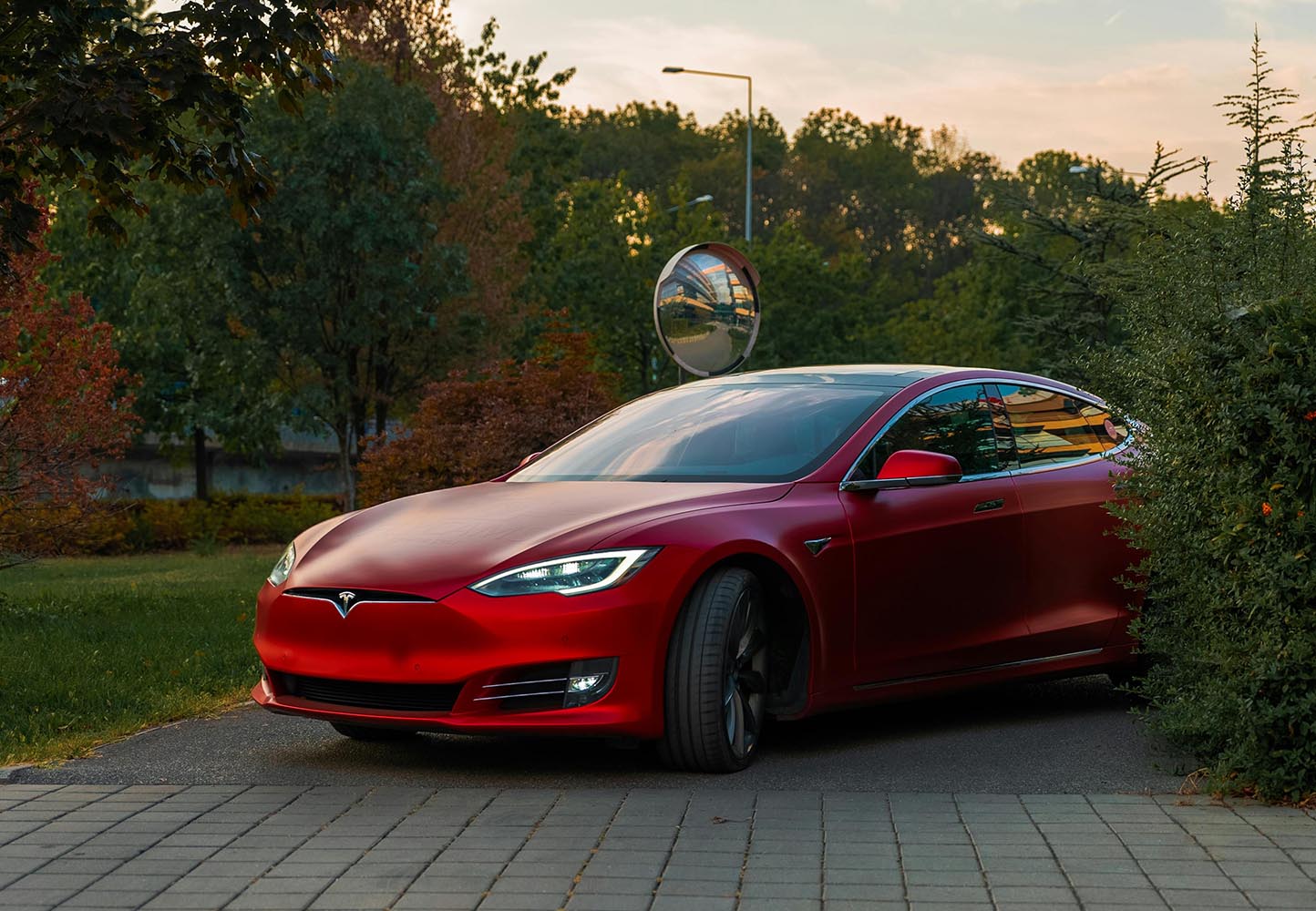
Tesla: Today’s greases well suited to electric vehicle requirements
Dr. Wenyang Zhang, senior staff engineer in Tribology & Oil System Engineering, heads the lubricant and tribology team at Tesla. Based in Palo Alto, California, U.S.A., the company’s headquarters until 2021, he oversees fluid engineering, including the design, selection and specification development of lubricants. His remit encompasses all lubricant-related aspects for both current and future Tesla platforms.
Tesla continues to lead in the development of EVs, producing 1.8 million vehicles in 2023. Approximately 10 million battery electric vehicles (BEV) were manufactured worldwide last year, accounting for 11% of the global passenger car volume. Year-on-year growth of EVs was around 30%, compared to 60% the previous year. Even though the rate is slowing, EV adoption is still growing fast, says Zhang.
Zhang is a Certified Lubrication Specialist from the Society of Tribologists and Lubrication Engineers (STLE) and a Certified Lubricating Grease Specialist from the National Lubricating Grease Institute (NLGI). He holds a BSc in Materials Science and a PhD in Mechanical Engineering and actively contributes to the academic community, including as Associate Editor of the ASME Journal of Tribology. With an impressive resume and intimate knowledge of the electric vehicle (EV) pioneer, Zhang is a highly sought-after speaker on the international circuit.
Advanced testing and system design for lubricant development
In March, Zhang was a featured speaker at F+L Week in Ho Chi Minh City, Vietnam, where he highlighted Tesla’s innovative approach to fluid development. This approach integrates a system design philosophy for fluids alongside the hardware development. He emphasised Tesla’s extensive in-house testing capability, which includes over 80 powertrain dynamometers (dynos) used to simulate real-world operating conditions and test how different lubricants perform under various loads, speeds and temperatures. Tesla continues to expand its testing capabilities, with plans to increase the number of dynos to over 100 in the next couple of years.
This testing capability allows Tesla to validate designs quickly and make informed decisions on lubricant optimisation. Zhang also noted the development of an in-house computer program that allows the automaker to rapidly iterate on lubricant design from a computational standpoint.
At the NLGI 91st Annual Meeting held at La Cantera Resort & Spa in San Antonio, Texas, U.S.A., in June 2024, Zhang presented “Tesla’s State-of-the-Art Approaches for Greases and Fluids in Electric Vehicles (EVs),” where he stressed that a system design approach is equally critical in the development of next-generation EV greases.
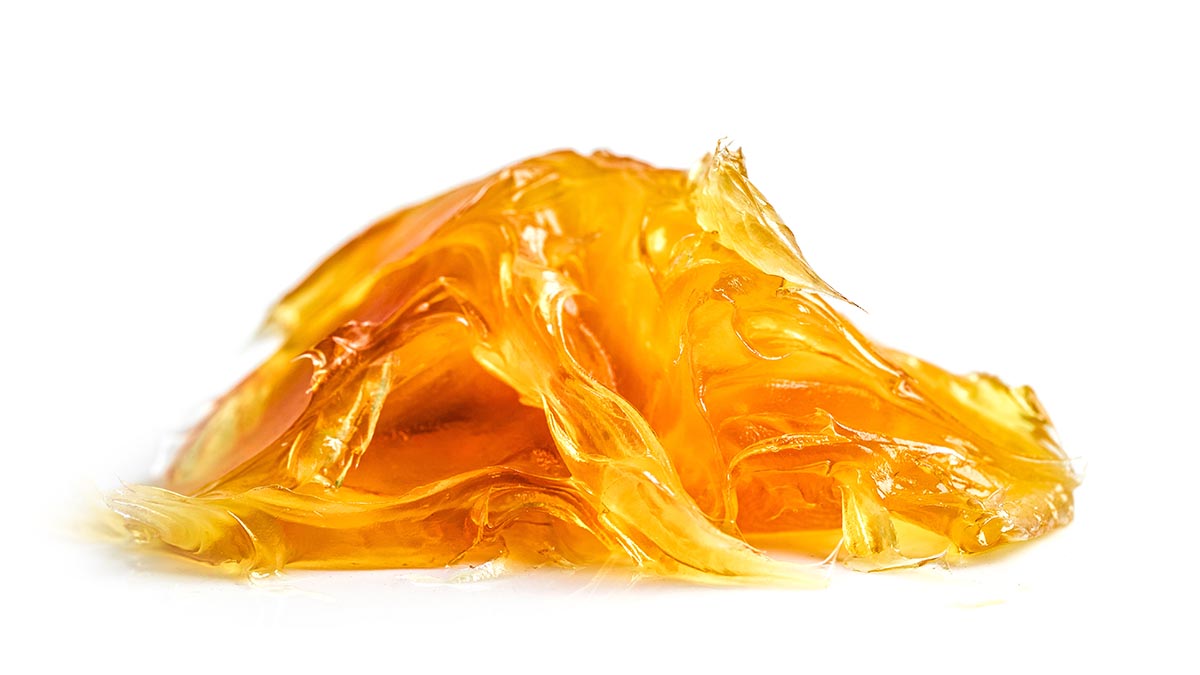
Key grease applications in Tesla’s EV platforms
Zhang detailed the primary grease applications for the Tesla Model S platform and chassis, while emphasising its impressive acceleration of 0-60 in under two seconds and acceleration forces ranging from 1.3 to 1.4 G-force, akin to today’s Formula 1 race cars. There are two primary grease applications in the chassis: Wheel-bearing grease, utilised in the wheel hubs, and constant velocity (CV) joint grease.
These two grease applications, along with the drive unit fluid, constitute the major lubricants used in Tesla’s vehicles.
Although drive unit fluid has higher volume than chassis greases, Zhang underscored the significance of greases in EVs, noting their volume amounts to ~37.5% of that for drive unit fluid. Tesla considers both grease and drive unit fluid as primary lubricants for EVs. While the grease volumes may be smaller, they are still considerable and in the same ballpark as drive unit fluids, says Zhang. Tesla’s approach to lubricants for EVs is “fill for life,” except in some special circumstances.
During his presentation, Zhang emphasised that today’s greases are well-suited for EVs, providing robust hardware protection and meeting durability requirements. Overall, there have not been significant changes in hardware for grease application between electric and internal combustion engine (ICE) vehicles, he says.
NLGI HPM Grease provides a robust foundation for formulating wheel-bearing grease, says Zhang. NLGI introduced this high-performance grease in 2021, surpassing the incumbent GC-LB specification long regarded as the benchmark in grease specifications. HPM Grease offers exceptional properties including high motor resistance, corrosion resistance, wide temperature range compatibility, prolonged grease life and structural stability, says Zhang.
He emphasised that Tesla’s goal is continuous improvement, aiming to further reduce friction to enhance overall performance. The wheel bearing grease experiences various lubrication regimes, including boundary lubrication and wear protection, and must operate at varying speeds and high temperatures—which can cause changes in viscosity. Tesla’s objective is to minimise friction across all lubrication regimes of the wheel bearing to improve performance.
CV joint grease is applied to the hub shaft, encompassing both the in-ball joint and the out-ball joint, crucial components of the vehicle’s drive system. Zhang again noted that HPM Grease serves as an excellent foundation, offering suitable characteristics. The goal remains to minimise friction, although the friction dynamics differ from those of wheel bearing grease due to the lubrication regimes and changes to contact mechanics. This prompts a different approach to grease design, he says. Zhang also highlighted the importance of protecting against reciprocating wear, robust fatigue wear protection and ensuring low-temperature noise reduction.
Challenges and innovations in EV lubricant technology
Zhang outlined several challenges facing the industry in advancing EV lubricant technology, including managing electrically-induced bearing damage (EIBD). This specific type of electrically induced bearing damage arises due to the unique electrical and operating conditions in EV motors. EIBD can occur when current flows through the rotor shaft, necessitating grounding to avoid compromising the bearings.
A special conductive grease application is used to ground the current from the rotor shaft to the chassis. The volume of this grease is tiny, less than 2 drums based on 2023 vehicle production volumes. However, this is a high-value grease, with extremely low electrical resistance, says Zhang. The grease must function as a conductor; even a semiconductor would not suffice for this critical application, he says.
The conductive grease is formulated with a high-temperature grease life capable of enduring more than 1,200 hours at 120°C. It must also withstand high dielectric stress, high-speed conditions, high compression and shear environments. For instance, if the motor spins at 18,000 RPM, the tiny bearings lubricated with this grease must sustain the same speed. Tesla aims to develop predictive models for EIBD to mitigate these challenges during the vehicle’s design stage rather than solving them post-production, says Zhang.