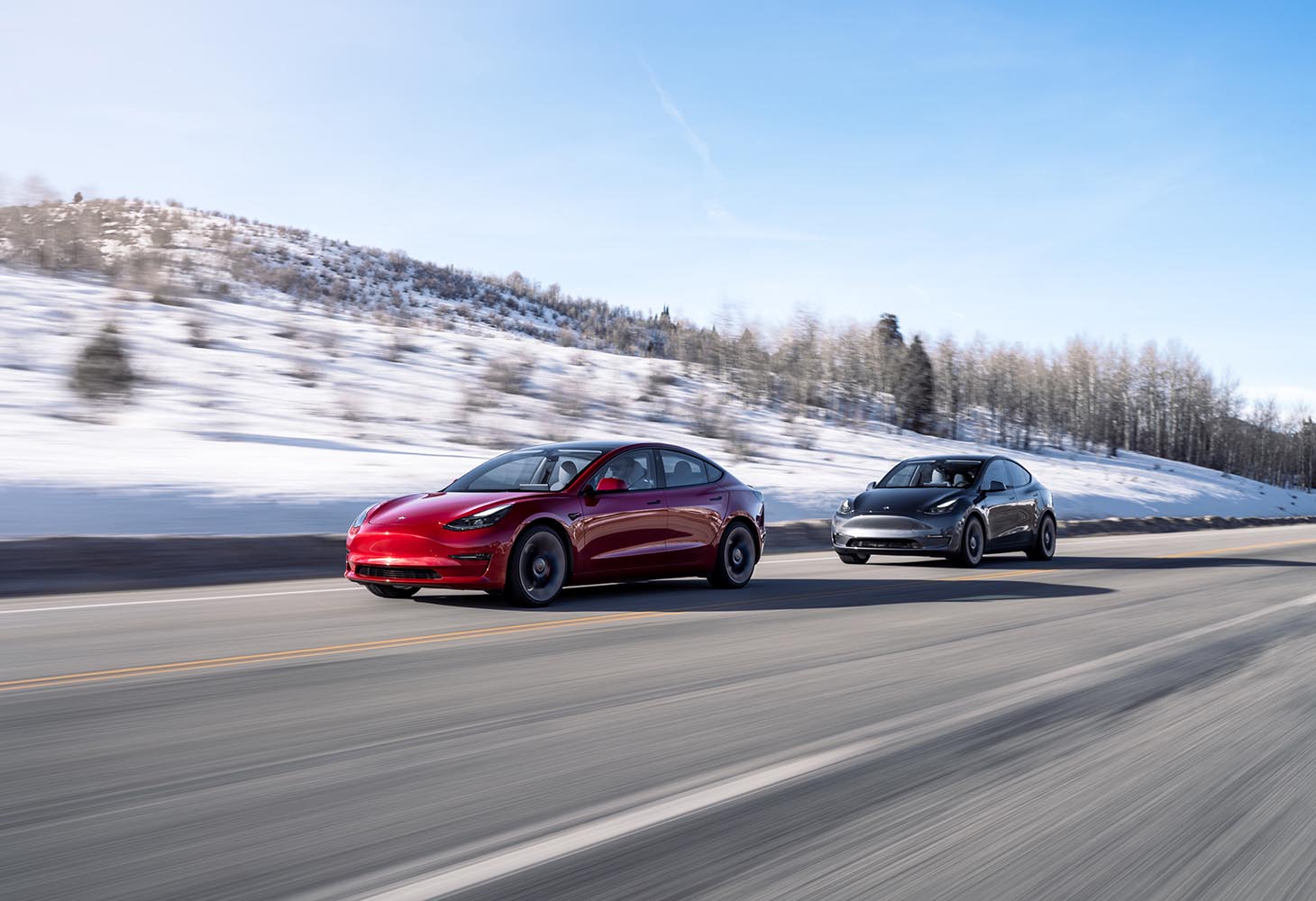
Tesla highlights importance of system approach in fluid design
U.S.-based automaker Tesla Inc. has been at the forefront of electric vehicle (EV) technology innovation since its inception in 2003. The Austin, Texas-based company’s strong commitment to design, performance and sustainability has resonated with a growing market of environmentally conscious consumers.
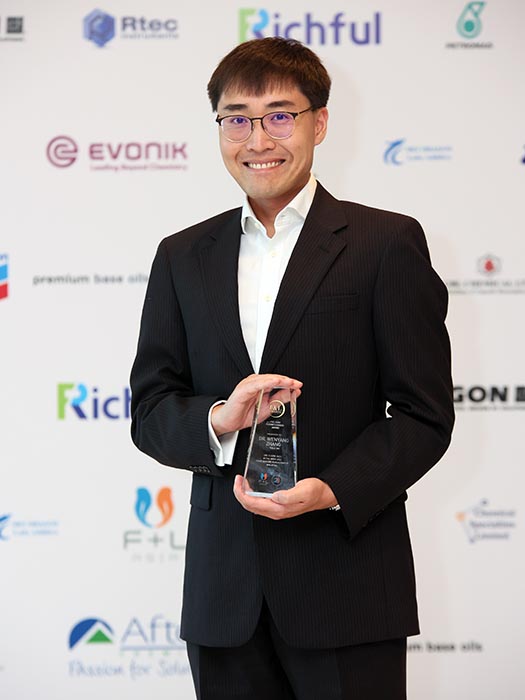
The Roadster sports car, Tesla’s debut model, was launched in 2008 followed by the Model S sedan four years later. In 2022, the company delivered 1.3 million vehicles across a growing portfolio of high-performance, long-range EVs. Based on deliveries in Q1 and Q2, Tesla’s vehicle sales are on track to grow another 40% to 50% in the current calendar year, says Dr. Wenyang Zhang, senior staff mechanical design engineer, drive system engineering at Tesla, Inc. Second-quarter deliveries were reported at 466,140, an 83% jump on the previous year and comfortably above market expectations.
Tesla operates six factories that produce EVs, solar and integrated renewable energy solutions across the United States (Nevada, Texas, New York, Fremont), China (Shanghai), and Germany (Berlin). The company has invested heavily in its supercharger network—which is a major differentiator for the company. Currently, Tesla operates 3,000+ supercharging stations, which include a total of 45,000+ superchargers, in strategic locations around the globe.
Zhang leads fluid engineering, tribology and lubricant-related subjects for all current and future Tesla platforms and is responsible for the determination of key lubrication parameters and designs.
Speaking at F+L Week in Kuala Lumpur, Malaysia, on June 14, 2023, Zhang provided an overview of Tesla’s state-of-the-art cooling and lubrication of drive units and the company’s vision for future development.
Unsurprisingly, Tesla’s every move is monitored very closely by the market due to the potential for it to shape the future of transportation and renewable energy. Tesla’s continuous advancements in EV technology, such as longer-range batteries and faster charging capabilities, and innovations in autonomous driving technology have garnered significant attention. However, there is also great interest in Tesla’s efforts from a tribological standpoint.
During his presentation, Zhang highlighted Tesla’s key fluid design considerations as the company endeavours to achieve higher efficiency without sacrificing durability. Fluids need to maintain sufficient fluid film to maintain durability, achieve lower friction and maximise heat transfer properties—by reducing working temperature and enhancing heat dissipation. Zhang emphasised the importance of appropriate base stock and additive selection, balancing and optimising viscosity, low elastohydrodynamic (EHD) traction and extended fluid stability.
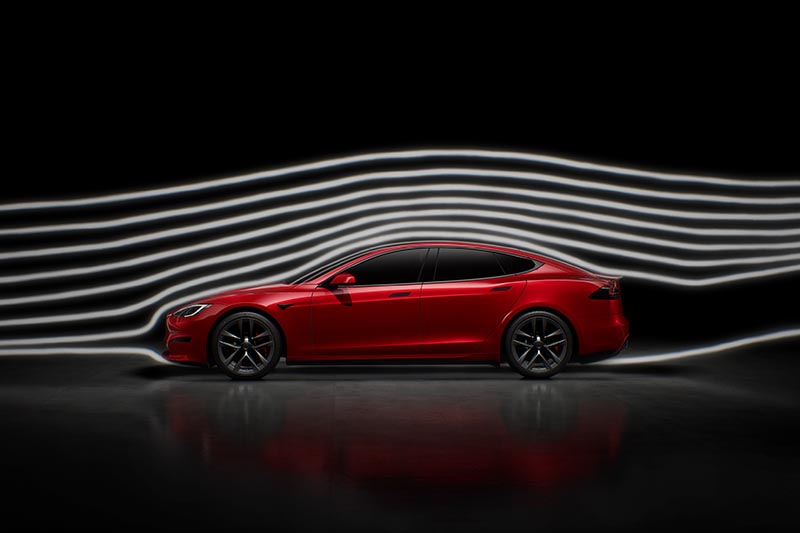
Zhang provided a breakdown of the energy efficiency of one of Tesla’s existing vehicles and drive units. ~10% of total vehicle loss comes from the electric motor, whereas only ~4% is contributed by the gearbox, he says. Within the gearbox losses, ~87% are torque dependent with the balance from torque-independent parasitic loss. Fluid formulation dominates torque-dependent loss and viscosity contributes to parasitic loss. Only ~13% of gearbox losses are determined by fluid viscosity, says Zhang. Although, the Tesla representative noted that the breakdown of losses is dependent on the drive unit design and driver behaviour.
There is an increasing push for ultra-low viscosities in the automotive sector that allow fluids to flow with greater ease. However, Zhang questioned the appropriateness of this approach. Individual drive unit components can cover a wide range of lubrication conditions. It is extremely risky to go to lower viscosity fluids without systematic understanding, simulations, and trials, he says.
Zhang outlined the results of an efficiency comparison of various fluid viscosities, comparing them to Tesla’s existing KAF I fluid. The KAF I formulation was employed in the fourth generation of Tesla’s drive units in 2022. Testing analysed gearbox efficiency and evaluated the performance of KAF I to 32 cSt fluid and 22 cSt fluid, as an example.
KAF I demonstrated greater efficiency in lower torque areas, but was less efficient in low-speed higher torque areas, boundary and mixed lubrication when compared to higher viscosity 32 cSt fluid. Analysed alongside the lower viscosity 22 cSt fluid, the Tesla formulation exhibited high efficiency in higher torque and lower speed areas, yet lower efficiency in lower torque areas. Rather than a singular focus on lowering viscosity, we need to optimise for different drive units and drivers, says Zhang. By taking a systematic approach in fluid design and computer simulation, with even slightly increased fluid viscosity, KAF I demonstrated close to 1% energy efficiency increase of the vehicle compared to the last generation of Tesla fluid, which is significant considering only ~4% of the accountable total loss.
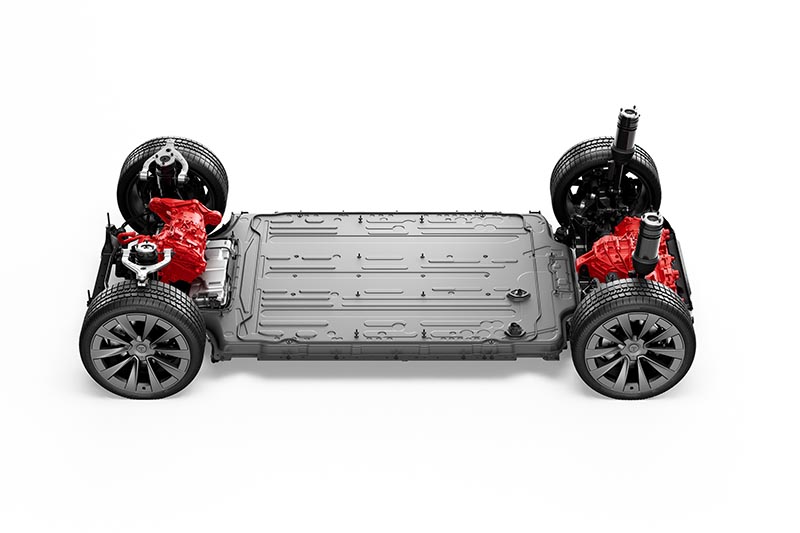
Many automakers look to combine lower fluid viscosity with cost-effective raw materials to further achieve cooling efficiency, energy efficiency, and to realise an appropriate build cost. Such an approach does not necessarily lower the overall system cost when you factor in vehicle lifetime performance, maintenance and overall energy cost, says Zhang. When it comes to solving the complexity of EV lubrication and lubricant design, Tesla is open to considering various types and costs of raw materials. It is not the game of fluid cost—but system cost and performance, he says.
During his presentation, Zhang outlined upcoming changes to Tesla’s lubrication and cooling designs. We are working on future fluid form optimisation with our additive partners, including fluid viscosity optimisation and mechanical design, he says. Based on the early findings of various formulations, Tesla encourages petroleum and chemical companies to work on new base oil molecules which could further enhance energy efficiency, for the next generation fluid formulation, KAF II.
Zhang’s presentation also outlined several drive unit challenges including electrically induced bearing damage (EIBD) and bearing creep. EIBD is a result of an induced voltage in the rotor shaft of a motor. Poor protection can result in heavy frosting and fluting. Tesla is interested in new grounding solutions to mitigate EIBD, he says.
A significant amount of radial wear on aluminium can lead to gear misalignment, gear life reduction, scuffing, and NVH (noise, vibration and harshness) issues. Axial wear can increase clunk due to additional motion in the shafts. There are solutions for bearing creep. However, Zhang outlined investigations into the impact of fluid formulations to understand if they can provide further mitigation.