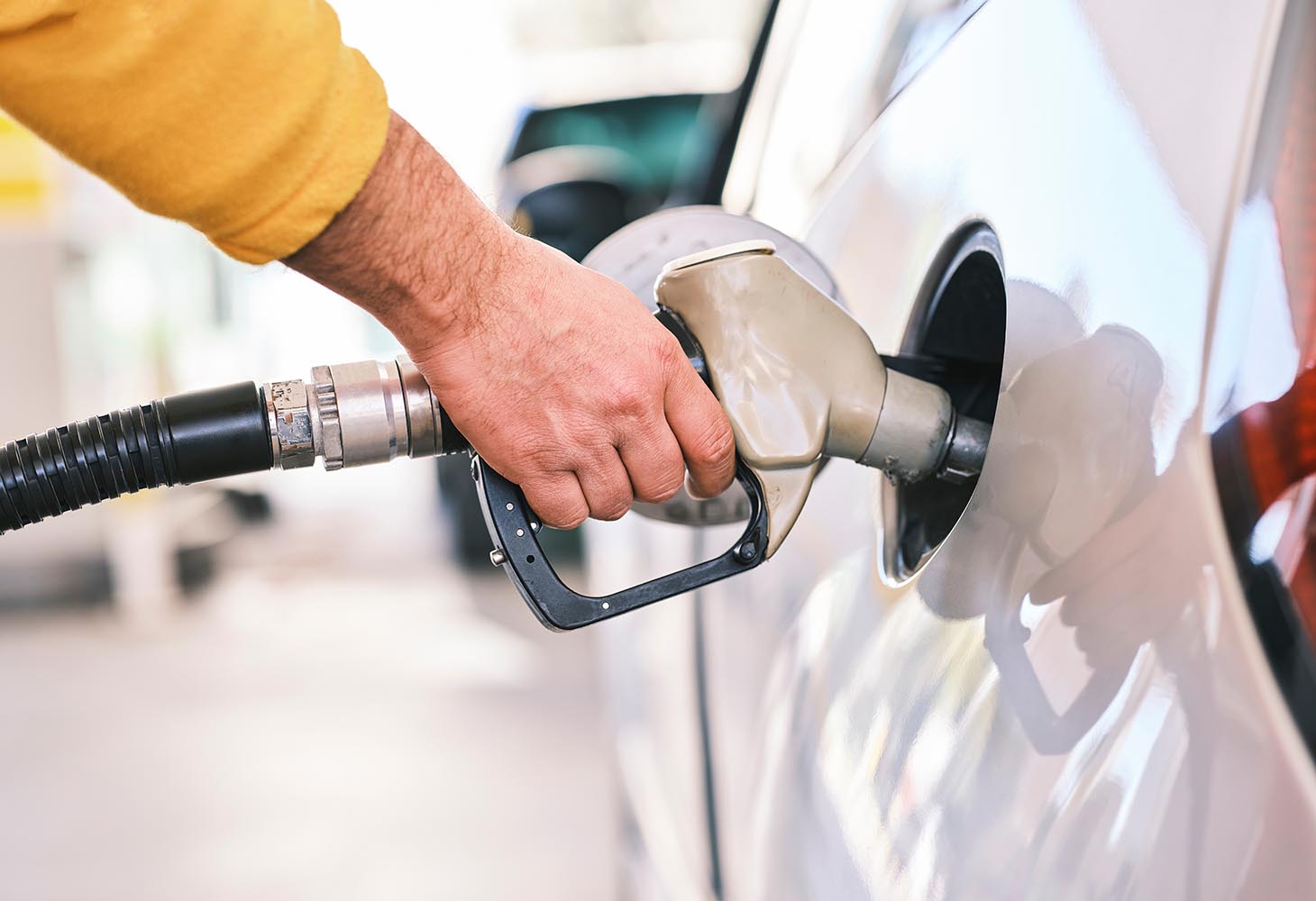
Study: Advanced aftermarket fuel additives essential for GDI engines
Gasoline direct injection (GDI) engines are an increasingly popular alternative to port-fuel injection (PFI) technology and have experienced rapid adoption in the automotive industry over recent years. In a GDI engine, fuel is injected directly into the combustion chamber at high pressure, offering a strong power output from a smaller engine, thermal efficiency and more economical fuel use.
Higher costs may constrain growth in some developing countries, but this has not stopped GDI from becoming the predominant technology in newer engine installations. GDI engines were installed in 53% of model year 2021 vehicles in North America, according to the 2022 EPA Automotive Trends Report. However, there are some downsides. Higher temperatures and pressures can lead to oil oxidation, deposit and soot formation and can compromise an engine oil’s useful life.
Carbon deposits can play havoc with GDI injector performance. Deposit accumulation on the injector tip can affect fuel spray characteristics, impeding fuel droplet atomization and dispersion. Untreated, a vehicle can experience power losses and declines in fuel economy and an increase in particulate emissions. GDI injector deposits have also been associated with abnormal combustion phenomena such as stochastic pre-ignition (SPI).
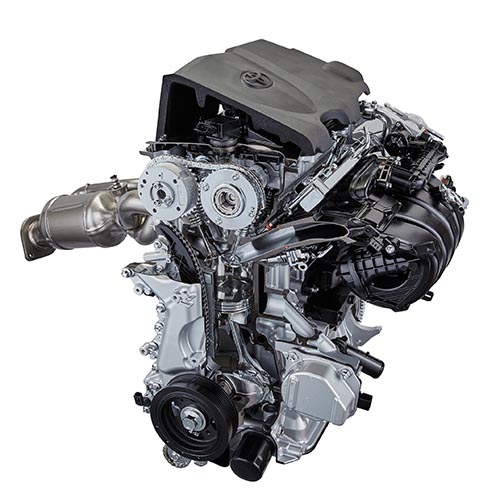
To combat these challenges, some vehicle owners have turned to aftermarket gasoline detergents containing deposit control additives (DCAs). However, not all of these additives are created equal. As Dr. Chung-Hao Kuo from Chevron Oronite pointed out at the SAE Powertrains, Fuels & Lubricants Conference in Krakow, Poland, in September 2022, there’s a pressing need to reformulate aftermarket fuel additives specifically for GDI engines.
Kuo’s research on aftermarket fuel additives revealed a significant gap in the market. Many deposit removal detergents were initially designed for port fuel injection (PFI) engines, leaving GDI engines underserved. While initiatives like the TOP TIER™ gasoline licensing program guide drivers towards high-quality fuels, they don’t address the specific needs of aftermarket products.
The goal of the research was to improve the understanding of how a shift in engine technology from PFI to GDI affects AFA formulation. The Oronite study analyzed various AFA products, revealing that many commercial products lacked the necessary detergents to combat GDI-specific challenges.
“Our research paper highlights that most of the deposit removal detergents in the market were formulated for PFI engines in the past decade, with limited development specifically targeting GDI engines,” says Kuo.
Oronite’s research analysed five AFA products including commercial products and newly designed additive technology. Products 1 and 2 were commercial AFA products that comprised predominantly hydrocarbon base oil and did not contain any active detergent. Product 3, a polyoxybutyl polyether amine, included 1210 mg of basic nitrogen (BN) per aftermarket bottle treatment and a solvent diluent. The final two products, 4 and 5, were experimental products, with equivalent BN and Non-Volatile Residues (NVR) content alongside alternative additive technology designed to be more effective in GDI engines.
Experimental design included a series of protocols and measurements to assess injector restriction and clean-up performance—including visual inspection to observe the impact on injector top deposits—and particulate matter (PM) impacts.
The study observed the critical importance of BN in the management of injector fouling. In testing completed on a 2012 GM LHU engine stand, products 1 and 2 did not offer any cleaning benefits on deposits in numerous engine tests. Conversely, product 3, which contained a nitrogen-based polymeric PEA detergent, exhibited strong performance—with an injector clean-up percentage value of 61.8%. Kuo noted that deposits were still present within the counterbores following a visual inspection of close-up images.
Kuo highlighted the “step out” performance of the experimental products (4 and 5) with injector clean-up values of 78.5% and 100% respectively—increasing percentage clean injector flow and leaving fewer deposits on the injector surface. Even though these products were formulated specifically for GDI engines, they are backwards compatible with PFI engines, according to the research.
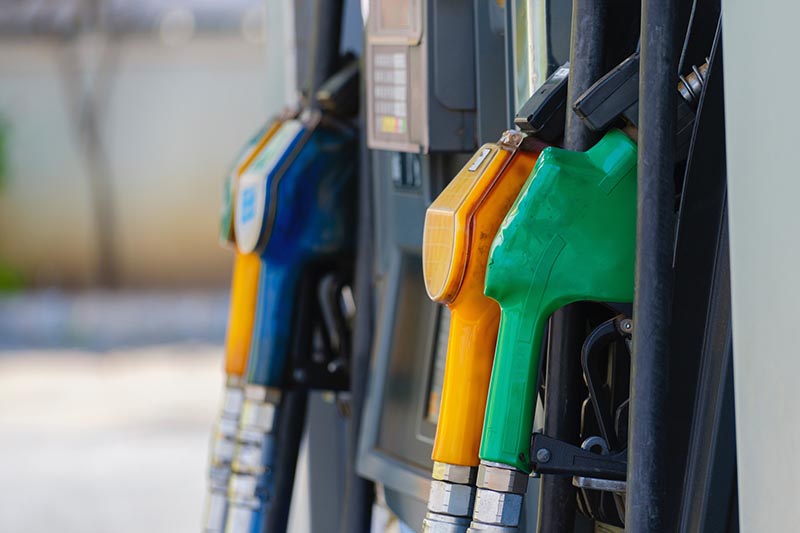
The effects of a commercial AFA product (3) on PM emissions were assessed in a Buick Regal engine throughout a 7.5-mile FTP-72 (Federal Test Procedure) test cycle followed by a 563-kilometre 1-tank clean-up (CU) in a mileage accumulation facility. No statistical differences in PM emissions were observed using product 3 compared to dirty injectors—indicating the product did not reduce PM emissions, despite the presence of polymeric DCA chemistry.
Further testing of injector deposits on PM emissions was completed on products 1, 3, 4 and 5 on an engine stand using a Honda 1.5L. The test consisted of a 50-hr dirty up (DU), followed by a 50-hr CU using the fuel additive package.
Product 1 continued to perform poorly, with no discernible reduction in PM emissions. After fuel substitution at 50 hours, product 3 delivered an initial reduction in PM emissions to hour 60 before gradually increasing again until the end of the test. Overall, a 30% reduction in PM from peak values at hour 50 was observed. This highlights the importance of a nitrogen-containing detergent package, says Kuo.
More promising results were demonstrated in the experimental products. Product 4 exhibited a dramatic reduction in PM up to hour 60 with continued reductions until the end of the test. An 83% reduction relative to the peak at 50 hours was observed. Product 5 additized fuel resulted in a 65% reduction in PM emissions out to hour 80, followed by a steady emissions level until test completion.
The Oronite study concluded that existing AFA products are not able to meet the performance required to clean GDI injector deposits effectively. The new technology demonstrated the effective elimination of GDI injector clogging, leading to a subsequent reduction in particulate emissions.