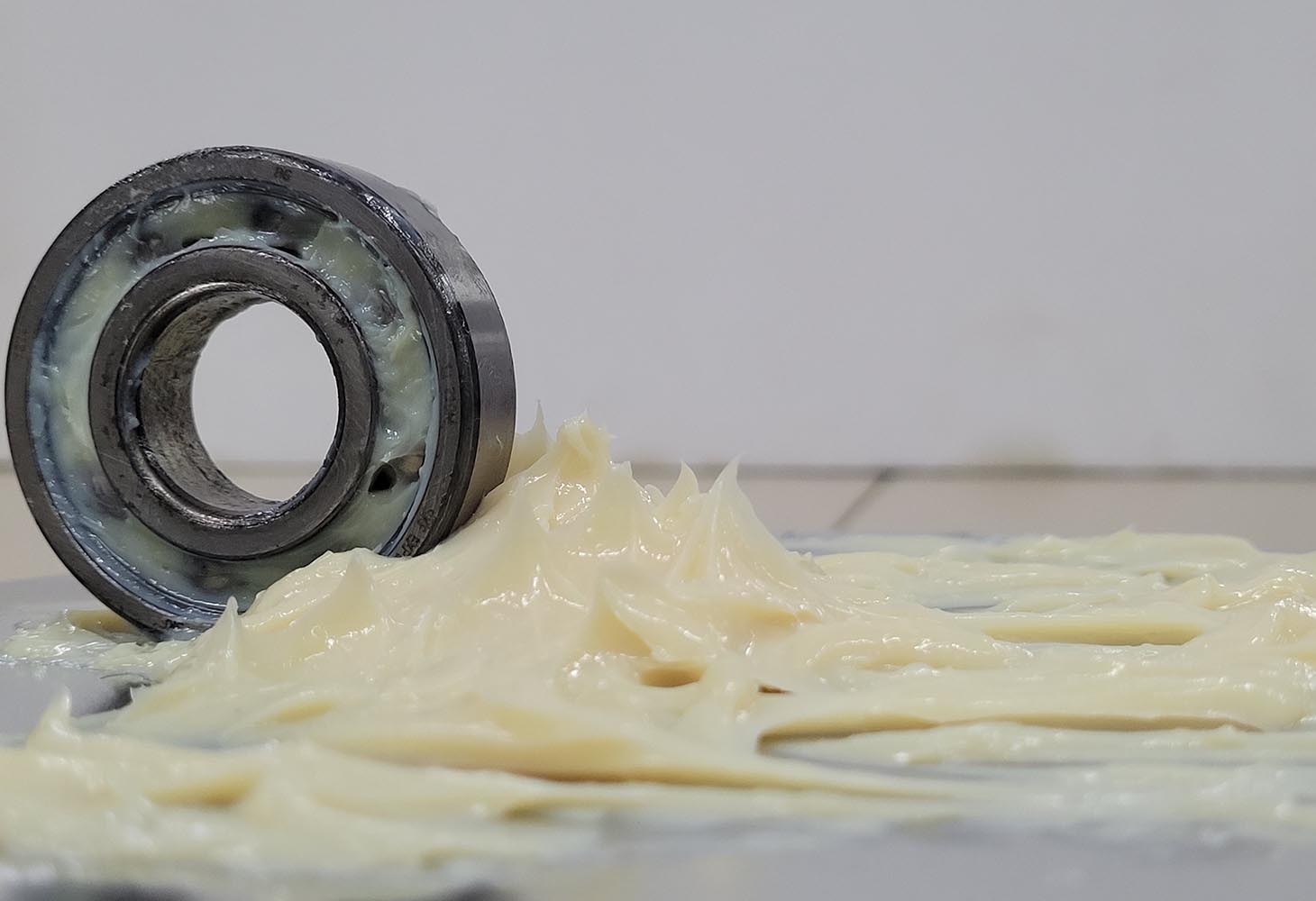
Polyurea greases may offer advantages for electric vehicles
Demand for electric vehicles (EVs) is already strong and the explosive growth of these alternative powertrains is expected to continue. About 70% of the global stock of electric cars in 2022 were battery electric vehicles (BEVs), according to Paris, France-based International Energy Agency (IEA). BEVs do not require engine oil and their growing adoption is set to have a significant impact on the automotive lubricants market. The IEA’s Global EV Outlook 2023 predicts that oil demand from road transport will peak around 2025, based on announced policies from governments.
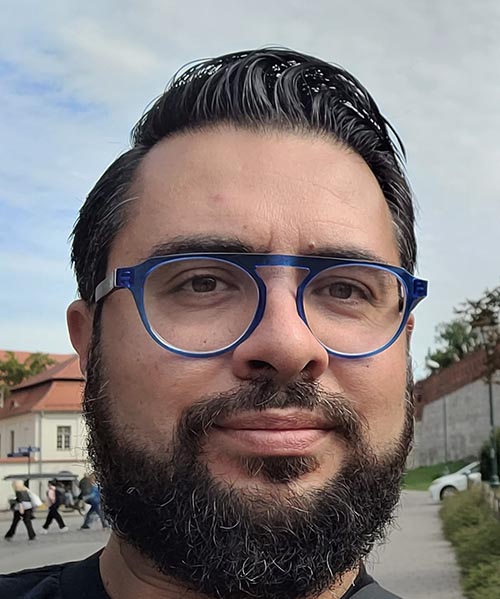
Upheaval in the development and market share of several types of lubricants is inevitable. However, not all lubricants will be negatively impacted. An increase in the demand and importance of lubricating greases for electric motors is anticipated alongside the EV and hybrid vehicle (HV) evolution, says Dr. George Dodos, a chemical engineer at Eldon’s Lubricants in Athens, Greece. Lubricating greases will continue to be used in chassis and wheel-bearing applications but especially in the case of electric motor applications, they will require new design criteria to address the challenges posed by EVs.
Formed in 1975, Eldon’s Lubricants is one of the largest production and trading companies in Greece. The company manufactures a full range of conventional and synthetic lubricants, greases and special products.
Dodos presented A Study on the Performance of Lubricating Greases for Electric and Hybrid Vehicle Applications at the SAE Powertrains, Fuels & Lubricants Conference & Exhibition in Krakow, Poland, held from September 6-8, 2022. The technical paper discusses the development trends for greases in EVs/HVs and assesses the performance of a series of grease formulations against quality parameters.
The importance of minimum electrical properties in greases throughout the lubricant lifetime was emphasised including electric conductivity/resistivity and dielectric strength—due to proximity to electric currents and electromagnetic fields. Inadequate electrical properties can cause electrical discharge damage which can eventually lead to bearing failures in the form of frosting, fluting and/or micro craters, says Dodos. The research mentioned the influence of base oil selection on electric properties and the potential adjustment using additives. Currently, there is no standardised method for measuring the electric properties of greases, he says.
The roar of an internal combustion engine (ICE) will usually mask any minor creaks and rattles during vehicle operation. With the quieter nature of EVs, noises stemming from the contact of surfaces can become more obvious. Dodos emphasised the rising importance of the noise-damping characteristics of greases. Greases also need to be thermally stable under a wide temperature range, with the ability to withstand sudden and multiple thermal shocks and temperature gradients.
Energy savings is another key design parameter to support higher mileage ranges. The paper noted EV motor speed can be two-fold higher than conventional high-speed thresholds and outlined the role of low viscosity greases in EV/HEV applications in reducing bearing torque for better economy.
Thickener chemistries impart a semi-solid consistency to greases. A variety of soap and non-soap thickeners are available—which include lithium complex grease, calcium sulfonate greases and polyurea formulations. Approximately 5-6% of the global grease market uses polyurea formulations, with its share expected to grow as polyurea is increasingly favoured in electric motor applications. In Japan, the polyurea market share is already much higher, at more than 25%.
The SAE paper outlined several advantages of polyurea greases including oxidative and shear stability, low noise characteristics, water resistance and low-temperature performance. Although, challenges were identified relating to production and a limited compatibility with additives and other thickeners.
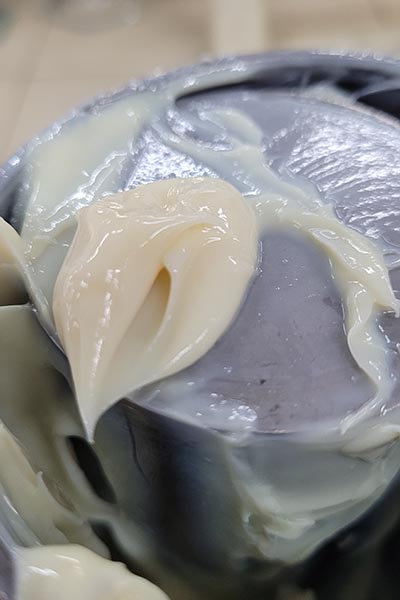
The research assessed a series of lubricating grease formulations based on polyurea thickener chemistry. The formulations excluded additives to restrict the results to the performance of the base oil. Greases were formulated using three kinds of base oils—polyalphaolefin (PAO), polyalkylene glycol (PAG) and polyolester (POE). Each grease had a similar ISO viscosity grade with a slight variance in thickener content. Formulations were finished to National Lubricating Grease Institute (NLGI) Grade 2—a widely used lubricating grease consistency.
Low-viscosity PAOs and PAGs are readily biodegradable. Dodos emphasised the potential sustainability benefits of premium renewable base oils, such as tailor-made oleochemical esters, in EV grease formulations.
The research reviewed grease performance against multiple quality parameters including dropping point (ASTM D2265), evaporation loss (ASTM D972), oil separation (ASTM D6184), oxidation (ASTM D8206), and leakage tendency (ASTM D1263)—which was followed by a change in the consistency—(ASTM D1403) and antiwear properties (ASTM D2266). Copper corrosion was assessed using a standard test method (ASTM D4048) and an in-house method was developed to determine noise-damping characteristics. Electric properties were tested first via the measurement of conductivity and the breakdown voltage of the base oils with subsequent data analysis on the breakdown voltage of the grease formulations.
The results of the study confirmed the advantageous performance of polyurea thickener systems in EV applications.
Relatively high dropping point values of above 250 degrees Celsius were observed in all samples. Dropping point refers to the temperature at which the grease loses its structural integrity. The POE-based polyurea greases demonstrated considerably higher dropping points.
The PAO-based formulations demonstrated a reasonably high oxidation stability, although it is the “considerably elevated” induction period of the polyol ester-based grease that is indicative of the potential of this base oil type, says Dodos. He also highlighted a possible synergistic effect of POE with the polyurea thickener. Low oxidative resistance was shown in the PAG formulation compared to the rest of the polyurea greases.
Leakage could cause premature deterioration of bearings and can contaminate the environment. The research stressed the strong reputation of polyurea thickened greases in leakage tendency, which is why they are often used in automotive wheel bearings. Grease formulated with PAOs displayed the least mass separation, whereas the POE formulation had a higher tendency to overflow from the bulk grease. However, Dodos noted that all results are within the repeatability of the method.
Base oil evaporation can impact grease life in rolling bearings. Despite the low viscosity of the base oils, evaporation loss at 100 degrees Celsius was found to be lower than 0.5% in all cases. Oil separation tests measure the inclination of the lubricating grease to separate at high or low temperatures during storage or normal operation. A satisfactory oil release tendency was observed during testing, which Dodos notes is typical for polyurea thickeners.
Efficient wear prevention properties were demonstrated in the four-ball wear test for all formulations, even considering the absence of additives in the designs. The experiment also verified that the selected base oils did not negatively affect the corrosiveness of the final formulated grease and none were characterised as corrosive to copper. The pro-oxidant activity of copper was also evaluated, showing that all formulations are efficient against the catalytic activity, with PAO and PAG greases being the least affected.
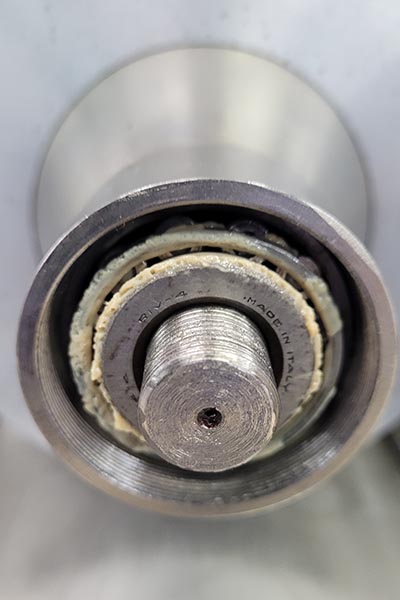
While no statistical significance was found between the greases on noise damping characteristics, Dodos noted the PAO and PAG greases provided relatively quieter operation of leakage tendency equipment compared to the POE-based formulation.
The POE and PAG base oils possessed a higher dielectric strength compared to PAO base oil, which was comparable to a typical transformer oil. The analysis indicated that the selected base oils are all appropriate for greases requiring medium-volume resistivity as they are neither purely conductive or insulating materials.
Results from the grease electric properties slightly contradict the base oil results. The PAO- and POE- based greases offered similar dielectric strength that could meet the requirements for an elevated behaviour in this parameter, says Dodos. However, the breakdown voltage of the PAG-based grease was substantially lower and regularly below the detection threshold of 10 kV. Further investigation of this finding is recommended, as the behaviour is at odds with the dielectric strength of the base oil, says Dodos.
In a continuation of this project, the cold flow properties of these three polyurea grease formulations are investigated, since this is also an important parameter for EV applications. The preliminary results obtained by DIN 51805, a test method that tests the flow of greases at low temperatures, show that at -30oC the flow pressure of all greases is satisfactory, being below the threshold of 1000 mbar. At lower temperatures, the presence of PAO or PAG appears to be more beneficial. A more detailed report of this work will be available later this year.
The development of specific specifications and standardised test methods within the grease industry is critical, particularly when it comes to the electric protocols of greases for EV applications. Collaboration between original equipment manufacturers (OEMs) and the grease industry is essential to ensure formulations that meet the evolving demands of a rapidly growing EV market.