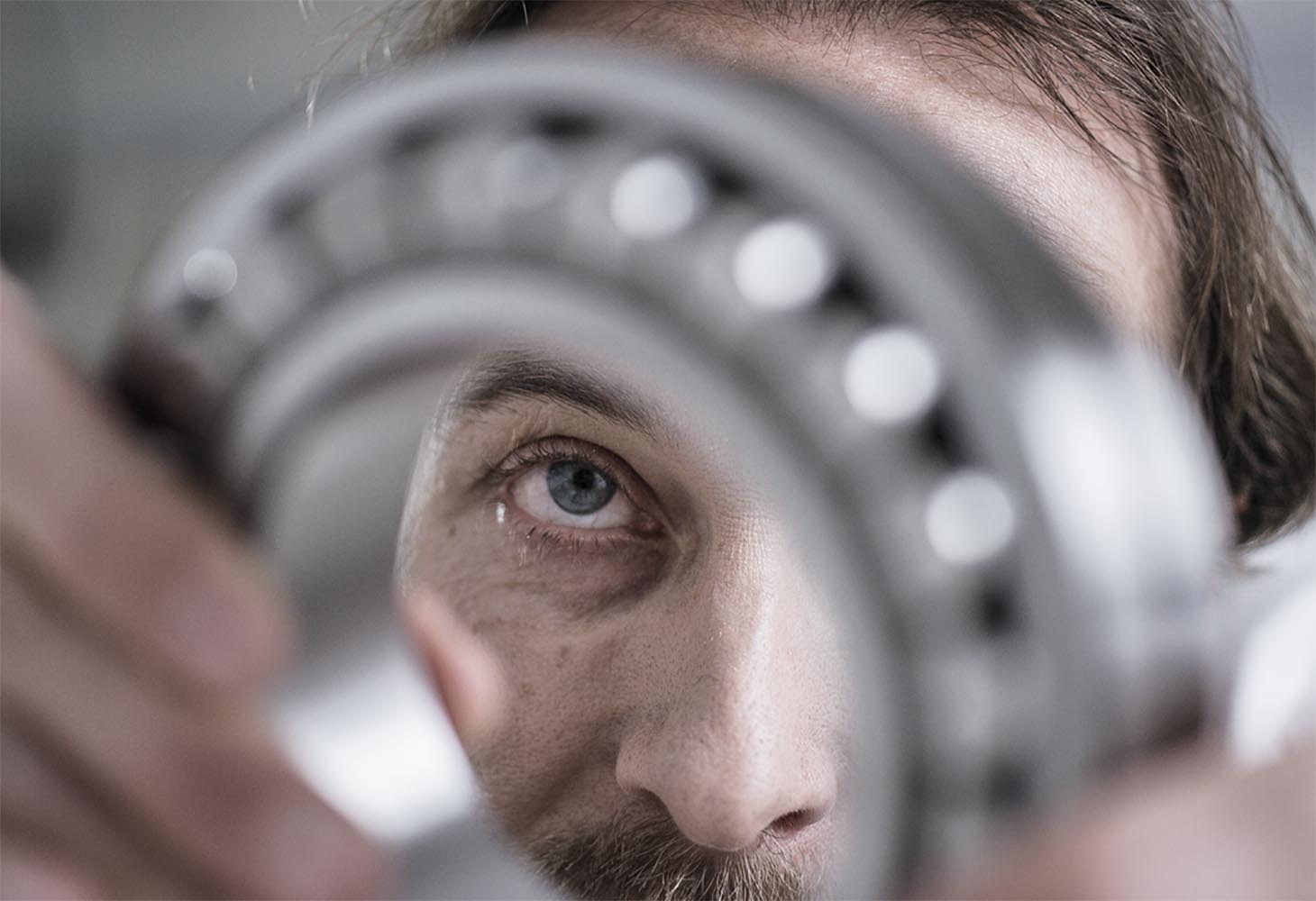
Oil as a service
Industry 4.0 is the fourth revolution in manufacturing. We are in the midst of a significant transformation of global industry that is blurring the boundaries between the physical and digital worlds. Technology is rapidly changing the businesses we are in, with this shift being reflected in new business models.
Traditional OEM and end-user business models bring with them an inherent conflict. OEMs are self-interested in selling more units in a transactional relationship. Buyers contact them when something requires replacement. However, the desire of end-users is to purchase less. What they need is the reliable functioning of a machine, a reduction in the total cost of ownership, minimal downtime, and low maintenance costs. It takes a significant leap of faith for either party to disestablish the existing business model. How can we align the interests of the manufacturer, user, and the environment?
Founded in 1907, SKF is a bearing and seal manufacturing company located in Gothenburg, Sweden. Reliability is of the utmost importance when it comes to bearings and rotation. During an SKF Technical Press day entitled “Bearing 2.0: What the future holds” on October 7-8, 2020, the company highlighted efforts to use technology to optimise rotating equipment performance and affiliate the interests of SKF with their customers. Imagine a situation where customers pay for results, and the opportunity value created in a performance-based arrangement is shared between both parties. This could be the reality in an industry 4.0 world.
Typically, customers contact us if something is broken, says Victoria Van Camp, chief technical officer at SKF. No doubt, SKF will continue to provide customers with the opportunity to purchase products. Though, Van Camp believes businesses need to take more responsibility for products than they have in the past.
During the Press day, Van Camp outlined the emergence of new subscription-based business models that include rotating equipment performance contracts. Customers are looking for a more holistic solution, including a single solution for multiple types of machines.
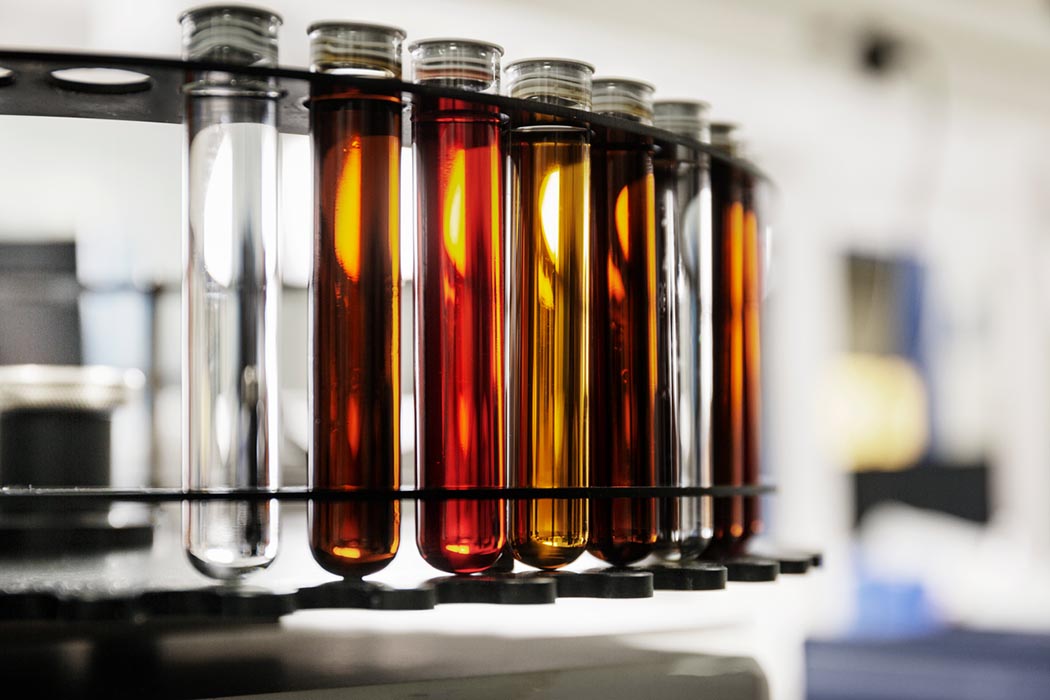
How open companies will be to rethinking business models in a Covid-19 impacted economy remains to be seen. SKF believes Covid-19 will reshape customer expectations and force a roadmap acceleration. The strategy remains, but on a shorter time scale, says Van Camp. The SKF representative also expects the green circular transformation will be fast-tracked and noted a rapid development of Asian markets.
A switch to new business models is not as simple as it sounds. Van Camp highlighted the growing importance of the “three A’s” — agility, accessibility, and artificial intelligence (AI). Plug and play solutions for fixed and mobile equipment, modular drop-ins for accelerated designs, re-manufacturable traceable products, design automation, digital twins and configurators will become increasingly prevalent to enable improved agility and accessibility.
Alongside the lingering effects of Covid-19, and the looming climate crisis, Van Camp emphasised a heightened reliance on “low skill and low travel.” Companies can no longer rely on the ability of a specialist to travel the globe. Companies have to make do with a less skilled local person who does not need to quarantine. The digital upskilling of staff will also be accelerated, she says.
A focus on performance requires care for a customer’s machine from design to monitoring and lubrication. Such contracts may cover repair, reengineering, reuse, and recycling, providing an opportunity to realise a circular economy.
Customers may not be ready for a new business model just yet, says Eitan Vesely, AI director at SKF. Still, we can help customers with their problems now, rather than lecturing them about changes, and the business model change comes later, he says.
Artificial intelligence holds the key to SKF’s performance-based offering. The bearing manufacturer acquired software company Presenso in October 2019, an organisation that develops and deploys artificial intelligence-based software for improving machine performance. The Israeli company employs data-driven Automated Machine Learning (AML) for predicting maintenance and integrates data from thousands of sensors installed on critical assets like pumps, fans, gearboxes and mills, and dozens of models.
The automated machine modelling means there are no overheads maintaining models once in production. The tool selects its algorithm, generates digital models of machines, continuously validates and maintains the models, says Vesely. Automation allows SKF to quickly respond to new and futuristic opportunities — reducing the incidence of unplanned asset downtime — or identify the root cause of failure and provide customers with corrective action recommendations.
So long as bearings are not run to failure, they can be remanufactured up to three times. If we can extend the bearing lifecycle, we can extend the machine lifecycle, says Van Camp, a step forward in achieving a circular economy. A connected supply chain can shorten lead times and optimise spare parts.
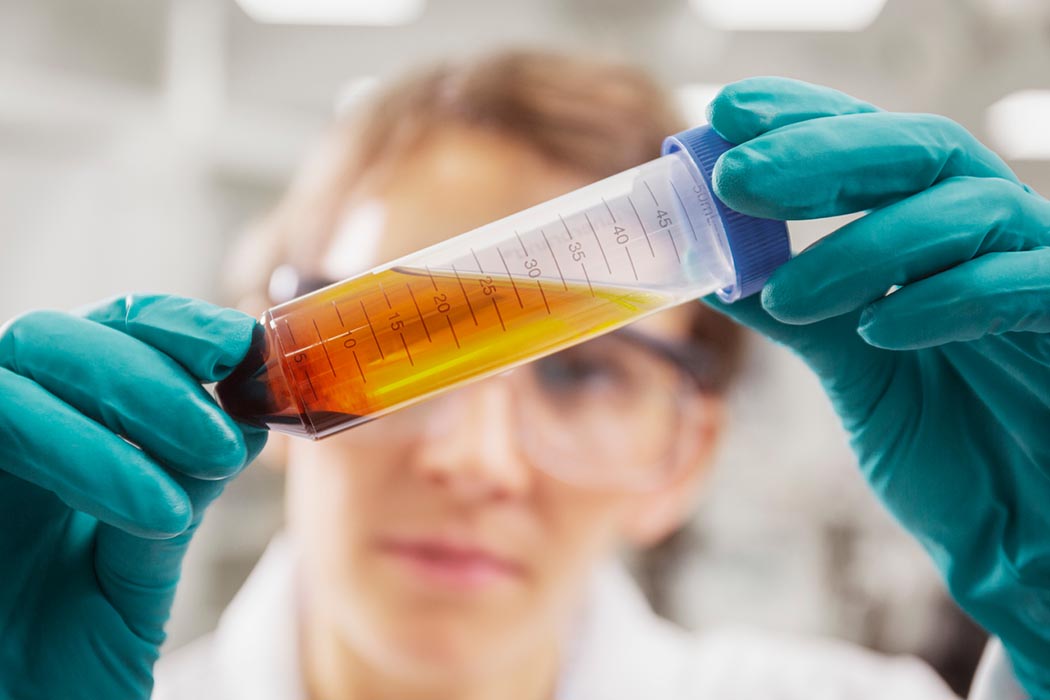
Lubrication management is a key consideration in any performance-based service, not to mention our efforts to combat climate change. The inefficient use of valuable non-renewable resources is an important factor. Every year millions of tons of industrial lubricants are used globally, emitting vast quantities of carbon dioxide during their lifecycle. Lubricant manufacturers are continually making advancements to oils, increasing drain intervals and reliability — in some respects, these improvements are to their own detriment.
There can be many reasons for bearing failure. Though, improper lubrication is at the top of the list, with some research indicating it plays a role in almost half of failures. Ensuring the right type, amount, and proper management of lubrication of bearings is vital to extending bearing life and minimising equipment failure.
Data analytics and machine learning can reduce total oil-related costs and the environmental footprint, says Van Camp. Rather than treating oil as single-use consumable; what if you could use the same oil over and over again?
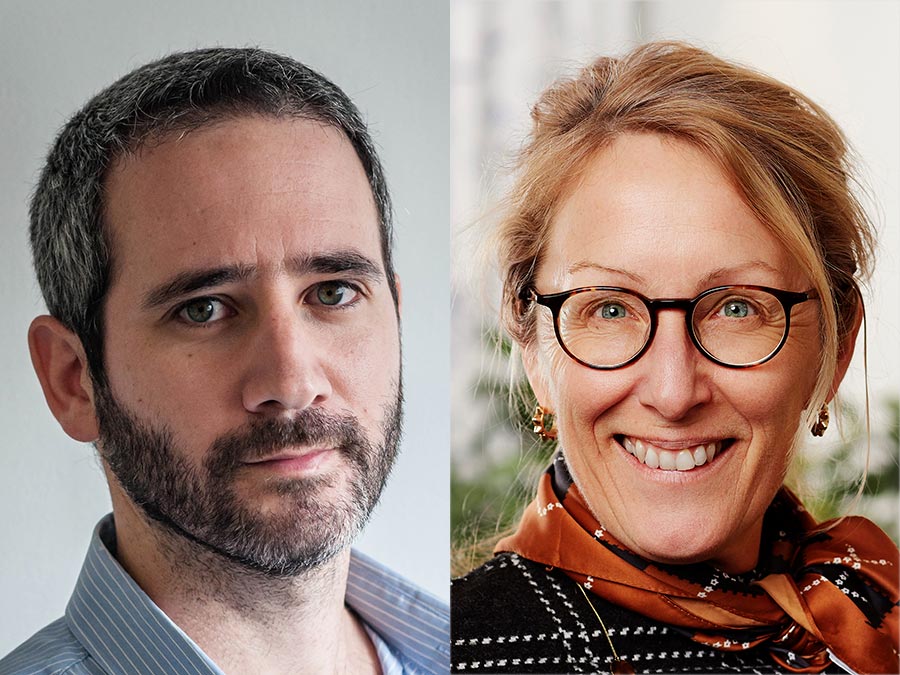
SKF’s performance-based business model includes “oil as a service.” SKF acquired cleantech start-up company RecondOil in 2019 to strengthen SKF’s lubrication offering. RecondOil was founded in 2010 by entrepreneur Fred Sundström. Using double separation technology, the company cleans oil to a nano level depth, allowing the regeneration of oil and giving it almost indefinite life. The circulating oil rarely needs changing, says Van Camp, and is suitable for nearly all machines that use oil as a lubricant.
For every oil litre reused, it saves up to 3 kg of carbon dioxide, the company claims. While ‘oil as a service’ appears to be a giant leap forward in the circular and sustainable use of oil, reducing the use of lubricating oil by up to 90%, the concept is likely to give oil manufacturers heart palpitations. Though, the future impact of “oil as a service” and predictive maintenance on broader lubricant volumes remains to be seen.