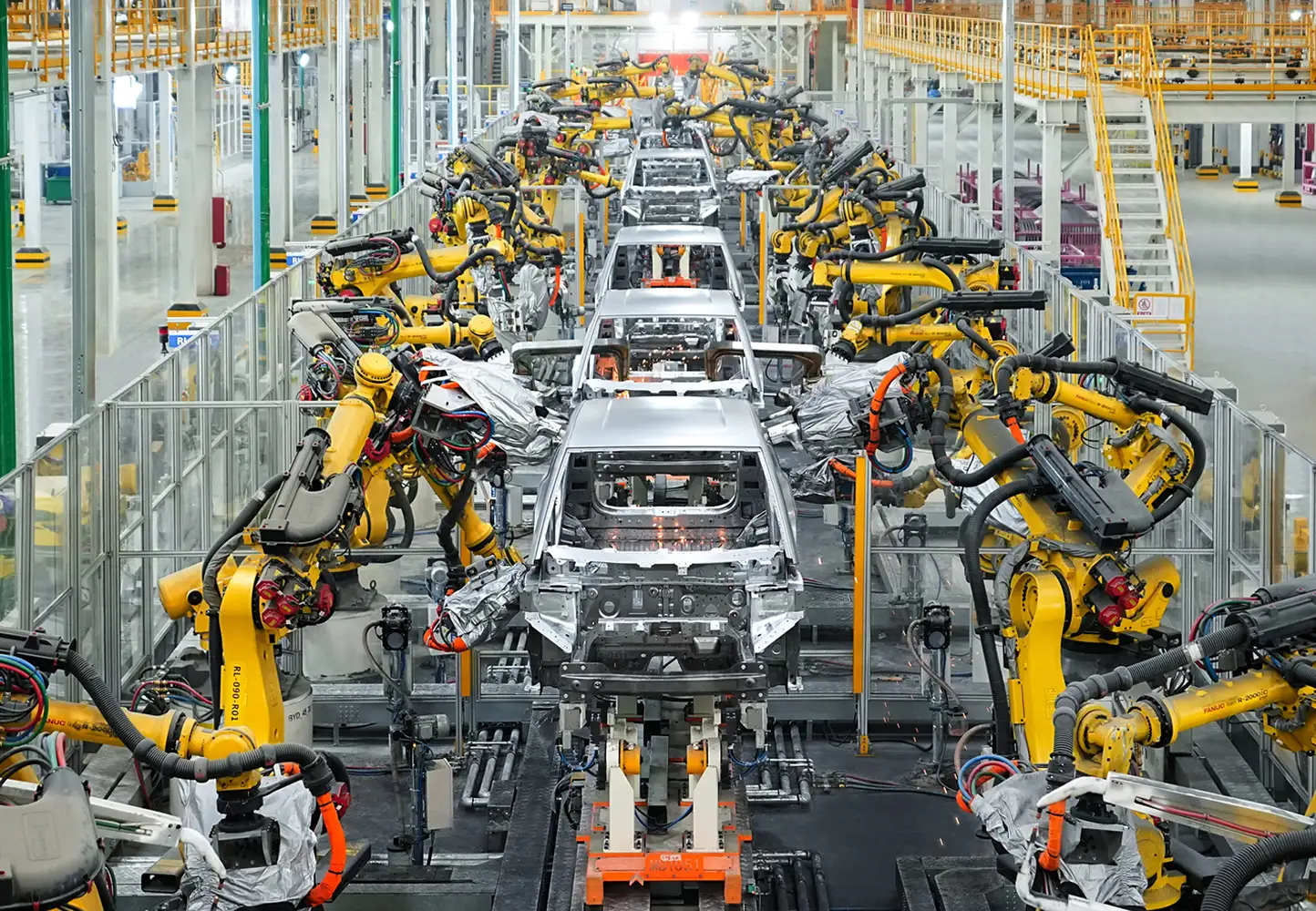
How automakers are driving supply chain sustainability
The International Organisation of Motor Vehicle Manufacturers (OICA) reports that road transport is responsible for 16% of human-made carbon dioxide (CO₂) emissions. With 80 million vehicles produced annually, the automotive industry has a pivotal role in emissions reduction. Many automakers are demonstrating a commitment to change, pledging to adopt more sustainable practices and shrink their carbon footprints, including a shift toward alternative fuel vehicles.
Shifting focus beyond the tailpipe
Existing efforts to reduce emissions have focused heavily on the tailpipe, with successive governments introducing strict exhaust standards and incentivising “zero-emission” vehicles. A collaboration between global management consulting firm McKinsey and the World Economic Forum suggested that around 80% of a petrol or diesel car’s lifetime emissions come from the exhaust, making it logical for environmental efforts to focus downstream of the dealership. Reducing emissions in modern vehicles involves more than just the tailpipe. The production of 80 million vehicles each year requires a staggering 112 million tons of materials.
The EV tipping point approaches
The future is unmistakably electric. Despite a temporary sales dip for electric vehicles (EVs) in some regions, the tipping point where battery electric vehicles (BEVs) will outnumber internal combustion engines (ICE) is drawing closer. A rise in EV models, extended range capabilities and growing customer demand all contribute to this shift. In a 2024 Spotlight on Mobility Trends, McKinsey predicted that annual EV sales could reach 40 million units by 2030. China, the runaway leader in EV adoption, has ambitious plans to expand into global markets.
With the EV revolution well underway, tailpipe emissions are no longer the sole focus. Automakers are looking upstream to meet carbon commitments, turning their attention from the vehicle’s use phase to production and the supply chain. Sustainable practices in manufacturing, particularly in battery production, are essential.
Stellantis’ supply chain strategy
Stellantis, formed in January 2021 through the merger of Fiat Chrysler Automobiles (FCA) and French automaker PSA Group, is one of the world’s largest automotive companies by revenue. Its diverse brand portfolio includes well-known names like Jeep, Chrysler, Dodge, Ram, Fiat, Alfa Romeo, Peugeot, Citroën and Opel.
In a recent episode of its Daring for Zero series titled Engaging Our Supply Chain to Mitigate Emissions, Stellantis revealed that 50% of the carbon footprint in its standard EVs comes from purchased parts, with batteries, steel and aluminium accounting for around 70% of emissions from these parts. Stellantis aims to reduce CO₂ emissions from EV parts by 40% by 2030, focusing on 70 key components that make up 80% of the carbon footprint in its purchased parts.
Prioritising supply chain sustainability
Supply chain sustainability has taken somewhat of a back seat in recent years as automakers navigated supply chain shocks from the pandemic and geopolitical tensions. However, sustainability in the supply chain can no longer be delayed. Without intervention, material emissions could account for 60% of a vehicle’s lifecycle emissions by 2040, according to McKinsey.
Vehicle manufacturing relies heavily on energy-intensive processes for the extraction, processing and production of materials like aluminium, steel, minerals, rubber and leather, all of which contribute significantly to emissions.
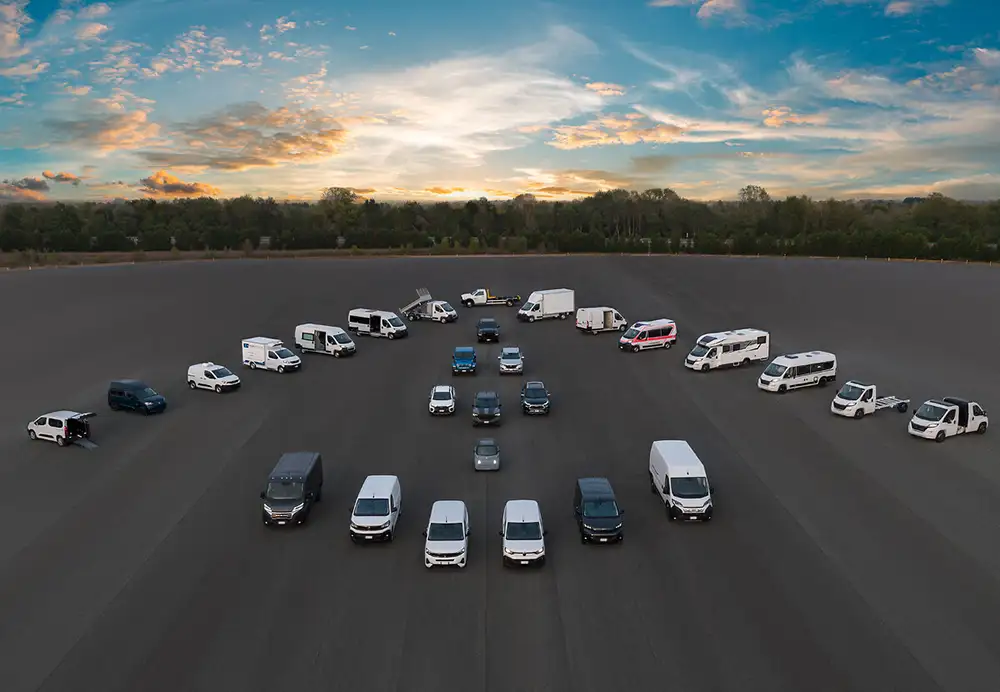
Energy-intensive materials drive emissions
According to the International Energy Agency (IEA), steel production accounts for 7-9% of global CO₂ emissions due to its coal dependence and energy-intensive processes, especially in blast furnaces. The World Bank estimates that aluminium production contributes about 2% of global greenhouse gas emissions. In 2022, the automotive industry consumed approximately 18% of global aluminium and 12% of global steel, with the top 16 automakers using an estimated 39-65 million tons of steel.
Decarbonising supply chains through innovation
McKinsey assesses that large lithium-ion batteries contribute 40% to 60% of total production emissions in EVs. The average EV battery today emits up to 100 kilograms (kg) of CO2 equivalent per kilowatt-hour (CO2e/kWh) as mining and refining of nickel, manganese, cobalt, lithium and graphite release substantial greenhouse gas (GHG) emissions.
A 2023 study by Poschmann et al., conducted in partnership with Volkswagen and the Institute of Environmental Technology at the Technical University of Berlin, titled Decarbonization Potentials for Automotive Supply Chains: Emission-Intensity Pathways of Carbon-Intensive Hotspots of Battery Electric Vehicles, explores potential emission reductions across the automotive supply chain.
The analysis focused on the reduction potential for steel, aluminium, battery cells, plastic and glass. Researchers found that emission intensities could be reduced by 69% to 91% by 2050. As a result, the carbon footprint of the reviewed vehicles could be cut by 47% in terms of supply chain emissions for BEVs. Nonetheless, the study concluded that BEVs cannot be fully decarbonised in alignment with the 1.5°C stretch pathway of the Paris Agreement through avoidance and reduction measures alone. The application of carbon removals is necessary to meet these climate goals, they say.
According to McKinsey, the global average of GHG emissions from battery production could decline to 85 kg CO2e/kWh by 2025. Ambitious industry players could go further, reducing the carbon footprint of battery production by up to 75% in the next five to seven years through concerted action across the value chain.
The majority of EV batteries are manufactured in Asia. Shifting battery production to regions with low-carbon electricity grids is a key strategy. Increasing battery production capacity in Europe, where electricity has a lower carbon intensity, is helping reduce overall emissions, says McKinsey. Factors such as design choices, vehicle type, range, freight requirements, production and sourcing locations all play a significant role in determining emissions levels.
McKinsey has also highlighted the merits of using recycled scrap in electric arc furnaces to produce steel, which it suggests will be cost-neutral in the future, and the opportunity of virgin iron reduced using hydrogen instead of coking coal.
Progress and challenges in supply chain sustainability
Lead the Charge, an advocacy network for sustainability in the auto industry, released its 2024 Leaderboard Report in February 2024, ranking 18 automakers based on their progress in eliminating emissions, environmental harms and human rights violations from their supply chains. The comparative report highlighted progress in making the automotive industry and its supply chain more sustainable. Notable advancements included advancements in sourcing steel without fossil fuels and improvements in human rights due diligence.
Despite the improvements, Lead the Charge suggested the industry continues to be “lacklustre when compared to the scale of the challenge.” Automakers are failing to take adequate action to ensure a just transition across their supply chains.
U.S. automakers have shown the fastest improvements in overall supply chain sustainability with Tesla demonstrating the biggest jump in performance and Ford ranking highest for overall supply chain efforts. In the category of Fossil-Free and Environmentally Sustainable Supply Chains, Volvo and Mercedes were the top performers.
Volvo stands out for its proactive approach to decarbonising the steel and aluminium used in its vehicles, scoring 42% on these indicators compared to an industry average of just 11%. Volvo is the only automaker to be a member of SteelZero and ResponsibleSteel, initiatives for responsible steelmaking, and has pledged to source 50% net-zero steel by 2030 and 100% by 2050.
Nearly half of the automakers evaluated have taken no concrete action on steel and aluminium decarbonisation, according to the report. No automaker has yet crossed the halfway mark toward building an equitable, sustainable and fossil-free supply chain. The report also highlighted stagnation in the responsible sourcing of transition minerals, as well as in the protection of Indigenous Peoples’ and workers’ rights.
Stellantis’ commitment to carbon neutrality
Stellantis, currently fifth on the Lead the Charge Leaderboard, has set an ambitious goal to achieve carbon net zero by 2038, with plans to halve CO₂ emissions by 2030, compared to 2021 levels. The company aims to offset only a single-digit percentage of residual emissions.
Its Daring for Zero series outlined efforts to engage thousands of suppliers in optimising resource use, minimising pollution and reducing GHG emissions across the supply chain. Stellantis says it is employing rigorous criteria in its sourcing strategy for EV components, focusing on environmental impact and prioritising components that can be re-manufactured, repaired, recycled or reused.
The Netherlands-based automaker is also exploring opportunities for greater vertical integration of the supply chain. Vertical integration involves automakers taking greater control of various stages of their supply chain —a strategy many carmakers are considering to reduce complexities and ensure sustainable practices.
Vertical integration as a strategic advantage
Vertical integration has been a critical component of the success of Chinese automakers. Leading Chinese automaker BYD has strategically employed vertical integration heavily in its market strategy, manufacturing its own batteries, chips, and motors. The company has also invested directly in raw material mining to enhance control over critical components. The approach has helped lower production costs and accelerate the transition to EVs in China.