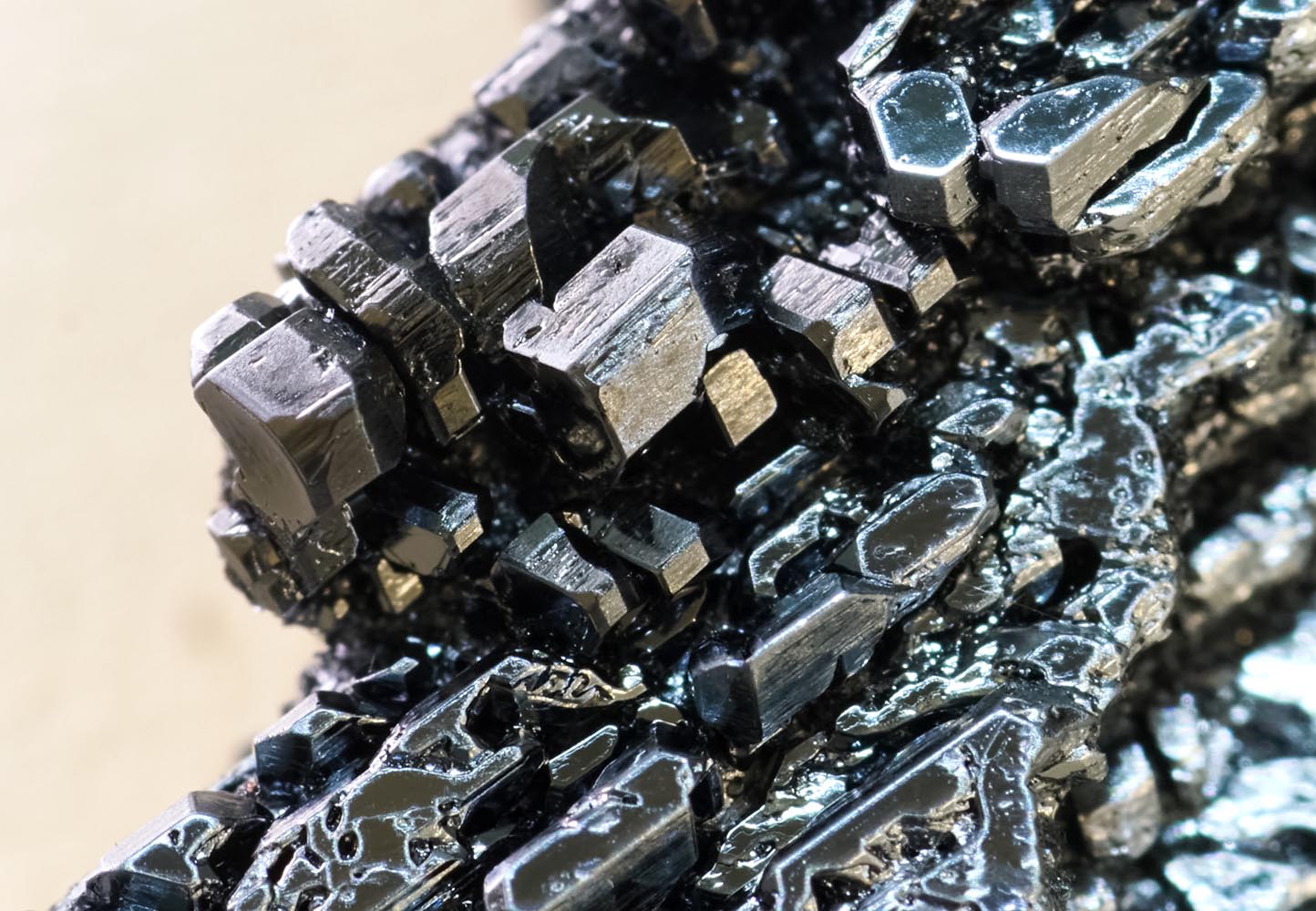
Global refrigerant shift: Navigating supply chain challenges for HFOs
As the global community intensifies efforts to combat climate change, industries reliant on refrigerants are increasingly switching to next-generation refrigerants like hydrofluoroolefins (HFOs) to reduce the environmental impact of cooling systems. This shift, driven by both regulatory mandates and market demand, brings significant challenges, particularly in securing the supply of critical raw materials, such as iodine, and managing the evolving regulatory landscape. The supply chain for these advanced refrigerants faces a complex set of challenges as demand for low-global-warming-potential (GWP) refrigerants continues to rise.
The Kigali Amendment and the global refrigerant shift
A major catalyst for this transition is the Kigali Amendment to the Montreal Protocol, adopted in 2016, which mandates the phase-down of hydrofluorocarbons (HFCs)—potent greenhouse gases used in air conditioning, refrigeration, and foam insulation. The agreement aims to reduce the production and consumption of HFCs by more than 80% by 2047. As a result, countries worldwide have begun implementing bans on high-GWP refrigerants like HFCs and are promoting the use of low-GWP alternatives such as HFOs.
- European Union: The EU has led the charge, banning HFCs with a GWP above 150 in certain applications, such as automotive air conditioning, as part of its F-Gas Regulation.
- United States: The U.S. Environmental Protection Agency (EPA) has enacted similar restrictions, phasing down HFCs under the American Innovation and Manufacturing (AIM) Act.
- Japan and Canada: Both nations are implementing Kigali Amendment mandates with their own phased approaches to HFC reduction.
- China and India: These rapidly growing economies are also key players in the global refrigerant market and have committed to phasedown schedules that align with the Kigali Amendment.
The adoption of the Kigali Amendment globally has spurred demand for HFO refrigerants, which offer the same performance as HFCs but with a fraction of the environmental impact. HFOs, such as R-1234yf and R-1234ze, have GWPs of less than 1, compared to R-134a, an HFC with a GWP of over 1,400.
Global demand projections for HFOs
The market for HFOs is experiencing rapid growth, driven by stricter environmental regulations and increasing awareness of climate change. In the short term (2023-2025), the global demand for HFOs is expected to increase at a compound annual growth rate (CAGR) of approximately 10%, as industries such as automotive, industrial refrigeration, and air conditioning systems switch to these low-GWP alternatives. By 2030, the market is projected to grow even further, as large-scale adoption across Asia, North America, and Europe accelerates, with demand potentially reaching millions of tons annually.
In the long term, by 2040-2050, HFOs will likely dominate the refrigerant landscape, with projections indicating global adoption across multiple sectors, driven by their superior energy efficiency, environmental safety, and regulatory compliance.
Iodine: A critical component and supply chain challenges
A key material in the production of HFOs is iodine, which is indispensable for the fluorination process involved in manufacturing these refrigerants. However, the iodine supply chain has been prone to disruption. During the COVID-19 pandemic, iodine supply faced significant bottlenecks due to halted mining operations, logistical challenges, and export restrictions. This created vulnerabilities in the supply chain for industries dependent on next-generation refrigerants.
Chile is the world’s largest producer of iodine, accounting for over 50% of global production, with companies like SQM and Cosayach dominating the market. Other key producers include Japan and the United States, which extract iodine from underground brines. However, reliance on a few geographic regions for iodine supply exposes the market to geopolitical risks and natural disasters.
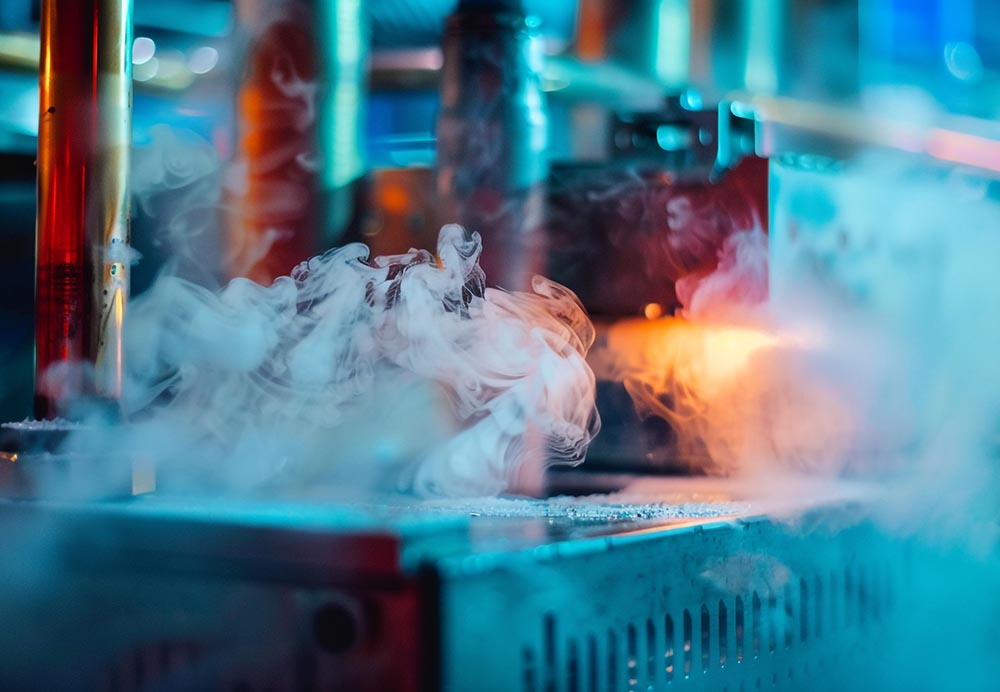
Key suppliers in the iodine supply chain and HFO market
- SQM (Sociedad Química y Minera de Chile): One of the largest iodine producers in the world, SQM supplies iodine for a range of industries, including the production of next-generation refrigerants. Its recent supply agreement with SK Enmove highlights the importance of securing iodine for refrigerant production.
- Cosayach: Another major Chilean iodine producer, Cosayach focuses on the extraction of iodine from caliche ore. The company is a key supplier for the global refrigerant market.
- ISE Chemicals Corporation (Japan): A significant producer of iodine extracted from brine, ISE Chemicals serves the growing demand for iodine in the fluorochemical and pharmaceutical industries.
While iodine remains critical to the production of HFOs, research is ongoing into alternative fluorination processes that could reduce reliance on this scarce resource. Synthetic catalysts and zeolite-based technologies are being explored as potential substitutes for iodine, though these technologies are still in the early stages of development. The goal is to create a more resilient supply chain that is less dependent on specific raw materials.
SK Enmove and SQM: A strategic partnership for supply stability
Recognising the critical nature of iodine in refrigerant production, SK Enmove, a subsidiary of South Korea’s SK Group, entered into a significant partnership with SQM (Sociedad Química y Minera de Chile), one of the world’s largest iodine producers. This strategic collaboration ensures that SK Enmove can secure a steady supply of iodine to support the production of next-generation refrigerants, particularly for the burgeoning electric vehicle (EV) market.
While specific financial details of the supply agreement have not been disclosed, the partnership underscores SK Enmove’s commitment to building a resilient supply chain. By securing raw materials like iodine, SK Enmove can ensure the continuous production of environmentally friendly refrigerants such as HFOs, which are essential for improving energy efficiency and reducing emissions in EVs and other applications.
Other supply chain challenges for HFO production
Beyond iodine, other supply chain challenges include:
- Fluorochemicals: The production of HFOs requires specialised fluorochemicals, which are subject to fluctuations in supply and pricing due to the concentration of fluorspar mining in regions like China. Any disruption in fluorspar availability can lead to bottlenecks in the production of HFO refrigerants.
- Specialised Equipment: HFO refrigerants require advanced production facilities and equipment capable of handling the high-pressure, high-temperature conditions needed for their synthesis. Scaling up these facilities involves significant capital investment, and any delays in equipment manufacturing or installation can affect supply.
- Regulatory Compliance: As global regulations continue to evolve, companies must ensure that their refrigerants meet the latest environmental standards. Navigating differing regulatory frameworks across regions can create supply chain complexity and lead to potential delays in production or distribution.
Lubricants for HFO refrigerants
Another critical component in the production and operation of HFO refrigerants is lubricants, which ensure the efficient operation of compressors in refrigeration systems. Polyol ester (POE) lubricants, polyvinyl ether (PVE) lubricants, and polyalkylene glycol (PAG) lubricants are commonly used with HFOs due to their chemical compatibility and thermal stability.
ExxonMobil, Chevron Phillips, and BASF are among the leading suppliers of synthetic lubricants for HFO refrigerants. These lubricants play a vital role in reducing friction, enhancing system efficiency, and ensuring the long-term stability of refrigeration and air conditioning systems.
Building resilient supply chains for the future
As the world transitions to low-GWP refrigerants to combat climate change, the supply chain for next-generation refrigerants like HFOs faces numerous challenges. From securing critical raw materials like iodine to navigating evolving regulatory landscapes, the industry must prioritize resilience and adaptability. Strategic partnerships, such as the agreement between SK Enmove and SQM, offer a glimpse into how companies are positioning themselves to ensure the stability of their supply chains.
In the future, research into alternatives to iodine and innovations in production technologies will be key to overcoming these supply chain vulnerabilities. As global demand for HFOs continues to rise, companies must invest in building robust supply networks to support the growing need for sustainable refrigerants.