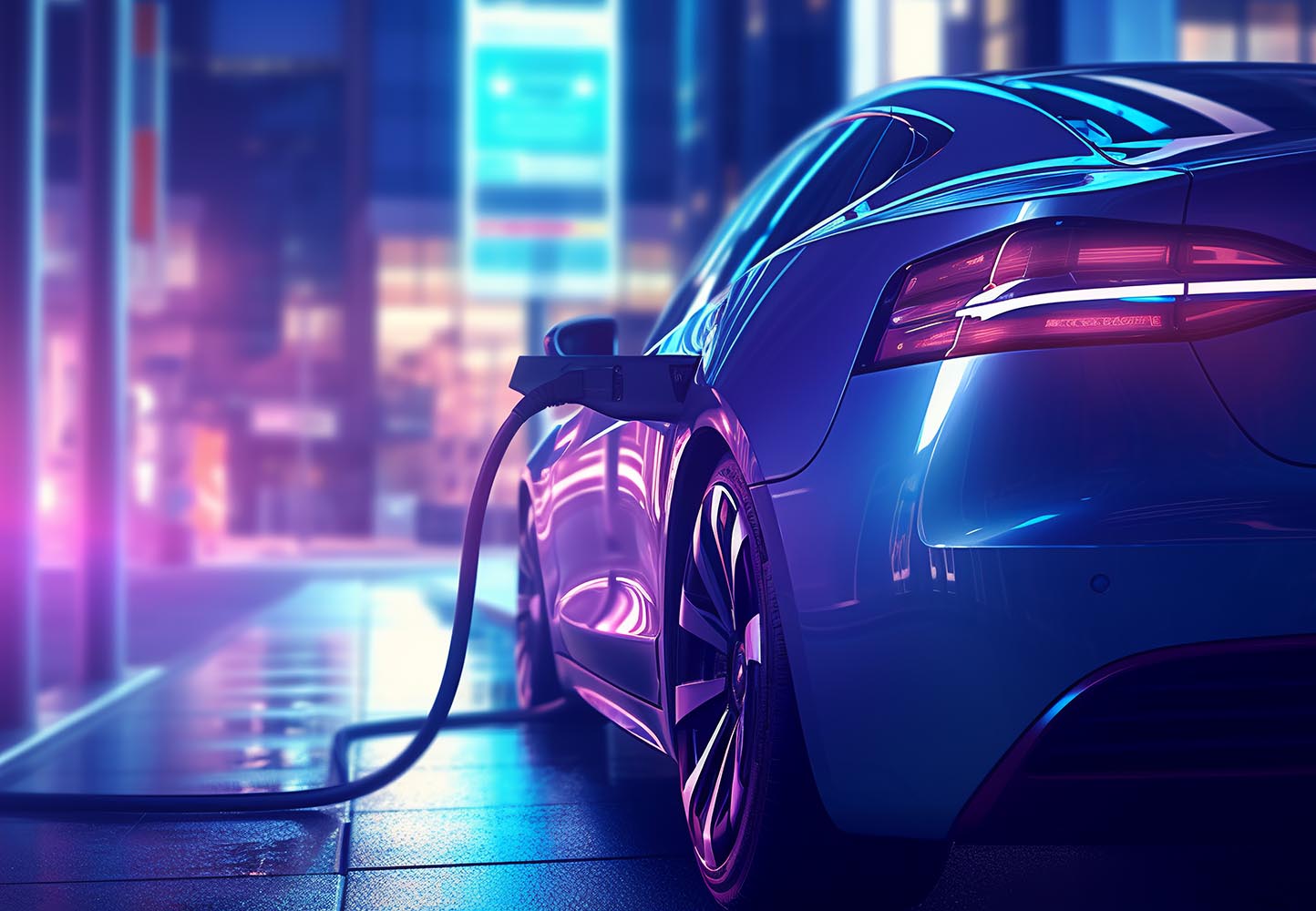
Global drive for standardisation in EV fluids and technologies
In 2023, around 90 million passenger vehicles were produced globally, with 11% being battery electric vehicles (BEVs). Electric vehicles (EVs) are increasingly becoming mainstream in the automotive market. However, the diversity in EV designs highlights the lack of standardised specifications or norms for their construction, components, and interfaces. This lack of standardisation extends to EV fluids, where there are no standardised specifications and test methods as there are for conventional engine oils.
Efforts are underway to address this gap, with several industry players establishing working groups dedicated to developing standards and performance specifications for EV fluids. At F+L Week 2024 held in Ho Chi Minh City, Vietnam, on March 7-8, Emmanuel Matray discussed ongoing initiatives in the United States, France, Germany, and China, to name a few. Matray is head of the Performance Fluids Department EV, Transmissions and Industry of TotalEnergies Lubrifiants SA, based in Paris, France.
In the United States, the SAE J3200 – TC3 Electric Drive Fluids Task Force (2022) brings together OEMs, additive and oil companies to develop new performance properties and suggested test methods for EV fluids. Another significant initiative is the Advanced Fluids for Electrified Vehicles Consortium (AFEV), led by Southwest Research Institute (SwRI), an independent, nonprofit applied research and development organisation headquartered in San Antonio, Texas, U.S.A. AFEV is investigating challenges in e-mobility such as high speeds, corrosion concerns and thermal properties.
In France, GFC (Groupement Français de Coordination) is exploring new aspects of EV fluids, including dielectric properties, high-speed wear, copper corrosion and water issues. GFC is a French non-profit organisation established in 1963, initially by the IFP (Institut Français du Pétrole), now known as IFPEN. Its main objective is to develop and refine testing procedures for the oil industry, engine manufacturers, and users, in coordination with other European entities, specifically addressing the unique requirements of French manufacturers and their brands.
In Germany, FVA Project 827 I, a collaborative effort involving the Forschungsvereinigung Antriebstechnik e.V. (FVA), the Fraunhofer Institute for Mechatronic Systems Design (IEM), and the Institute for Drive Systems and Power Electronics of the Leibniz University of Hannover (IAL), is conducting a preliminary study on high-voltage e-drive oil. This platform aims to facilitate the modeling, model coupling, and simulation of electric drives for research and industry experts.
China’s NB/SH/T 6042-2021 is an industry standard that ensures that lubricants for electric vehicle reducers meet specific criteria to provide effective lubrication and protection for electric vehicle gear systems. It specifies product varieties, requirements, test methods, inspection rules, marking, packaging, storage, delivery acceptance for lubricants produced using mineral, synthetic or semi-synthetic oils. This standard was issued on November 16, 2021, and was implemented on May 16, 2022. The Research Institute of Petroleum Processing (RIPP) is leading a group primarily focused on developing a comprehensive EV fluid specification (GB/T) with an emphasis on new testing methods for durability, efficiency and more.
In Japan and South Korea, efforts are mostly undertaken at the OEM level, with limited publicly available information.
Matray used the F+L Week forum to unveil TotalEnergies Lubrifiants’ new global EV specification dedicated to EV fluids. The pioneering standard encompasses a comprehensive electric drive unit (EDU) specification with robust benchmarks and internally developed methods. The initiative is geared towards assisting TotalEnergies’ partners in smoothly transitioning to e-mobility, says Matray.
One might wonder why the lubricant arm of global energy company TotalEnergies is taking the lead in developing a comprehensive EV fluid specification. Matray proposed it was their responsibility as a lubricant player and marketer to drive quality improvement in the EV segment, especially in the absence of any comprehensive specifications. TotalEnergies does not aim to substitute OEMs’ expertise, but to leverage their extensive lubricant knowledge and experience to fill the gap, he says.
TotalEnergies Lubrifiants, the fourth largest lubricants player globally, boasts 41 lubricant production plants worldwide, along with nine grease manufacturing locations and a dedicated workforce of 5,800 staff. They distribute products in 160 countries, demonstrating their global reach and influence. Notably, in 2018, TotalEnergies Lubrifiants introduced Total Quartz EV Fluid for light vehicles and Total Rubia EV Fluid for industrial, utility vehicles and electric buses. They are the world’s first product range of fluids tailored specifically for hybrid and electric vehicles and was recognised by F&L Asia as the Product Development of the Year in 2019.
The EV specification provides a comprehensive evaluation comprising five main parts: physico-chemical analysis, tribological tests, component testing, and system and fleet testing. In addition to standard tests, TotalEnergies Lubrifiants employs several internal methods, including assessments for copper corrosion and other specific criteria, ensuring a thorough examination and validation of EV fluid formulations.
Physico-chemical analysis, tribological and component testing are conducted to replicate the primary constraints of EDU fluids, encompassing gear and bearing durability, heat transfer characteristics and emerging concerns such as electric properties.
Matray outlined two new tests that are not traditionally employed. The Printed Circuit Test involves the optical inspection of components at the end of the test and continuous resistivity monitoring during ageing. An assessment of compatibility with coating materials, especially copper wire, utilises an adapted version of an existing test.
The TotalEnergies representative also outlined an in-house durability method as part of system testing that entails a rapid EDU durability assessment lasting 120 hours and simulating real-world conditions. The test methodology is designed to induce failures comparable to those observed in traditional mileage accumulation tests, primarily focusing on wear and gear scuffing.
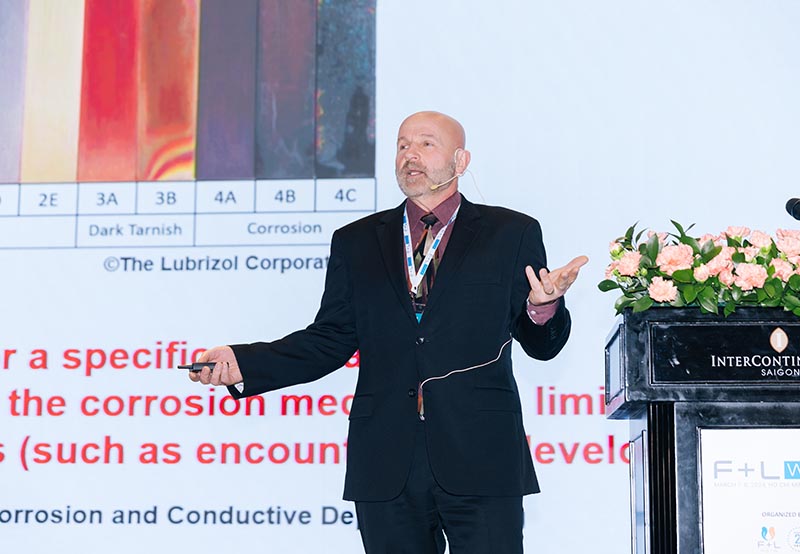
During F+L Week, Greg Miiller, VP of engineering and new business at Savant Inc., based in Midland, Michigan, U.S.A., raised concerns regarding the potential formation of conductive deposits and copper corrosion in electrified drivetrains. Miiller highlighted the shortcomings of the existing copper strip immersion test, ASTM D130, including its variability and reliance on operator judgement. ASTM D130 has been widely used since its introduction in 1922, however, the standard does not provide detailed information on the corrosion mechanism and is not sufficient to assess lubricant suitability in the EV industry, he says.
Electric motors and electronics in modern vehicles increasingly interact with lubricants or their vapour, making copper corrosion and conductive deposit formation on critical components a pressing issue. A detailed understanding of the interaction between the lubricant and copper components and wiring is critical. Miiller stressed the urgent need for directly applicable tests tailored to the evolving needs of the EV industry.
There are various versions of the copper test method already in use within the automotive industry. Although, like TotalEnergies’ in-house assessment, none are standardised.
Miiller outlined two new test methodologies: the Wire Corrosion Test (WCT) and the Conductive Deposit Test (CDT), developed by Savant Laboratory and its partners, including Lubrizol, APL and the Ford Motor Company. Together, these tests offer a predictive assessment of the corrosion and deposit risk in electrified systems. Efforts are underway to standardise these test methods and make them widely available.
In a world-first announcement at F+L Week, Miiller revealed that the CDT has received official approval from ASTM International, the global standards organisation that develops and publishes voluntary consensus technical standards. Miiller provided attendees with a sneak preview of the new standard, designated ASTM D8544-24, which was subsequently launched on March 14, 2024.
ASTM D8544-24 includes a 500-hour test length with a temperature of 150 degrees Celsius (°C). The test quantifies the accumulation of conductive deposits over time to assist in the determination of problematic systems.
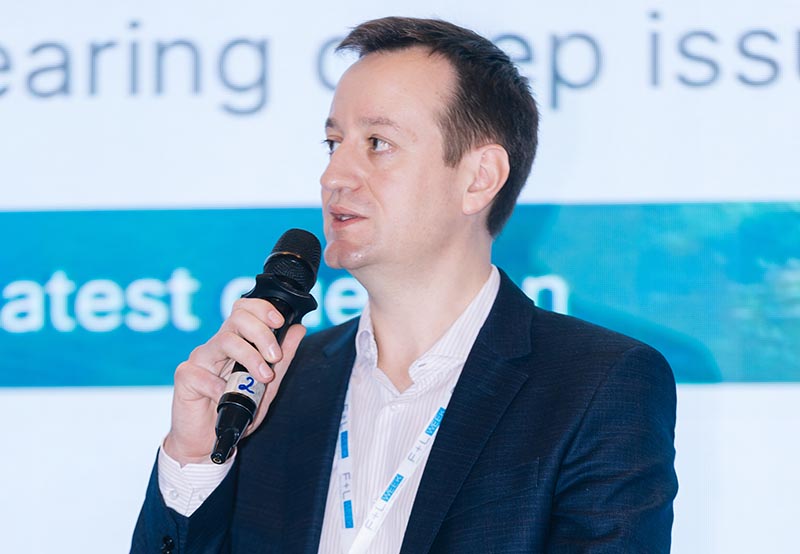
An additional ASTM standard has also been proposed for the WCT, which monitors corrosion events from copper or other metal substrates. Emmanuel Matray Miiller affirmed its applicability not only for the EV sector but across various industries. This 72-hour test evaluates corrosion risk at two critical temperatures (130°C and 150°C) and is presently in the round-robin stage. The WCT monitors real-time corrosion events with remarkable accuracy, precision and repeatability, says Miiller.
Alex Wang, technology development manager, Driveline & Future Mobility at Lubrizol China, highlighted the critical importance of conducting full unit testing on electrified hardware, including e-axles and dedicated hybrid transmissions, for e-fluid development. He outlined the test bed capability at Lubrizol, where the company has developed a full-scale unit that measures durability, thermal properties and efficiency—providing fundamental knowledge used to develop new fluid platforms and optimise e-fluid performance.
Wang detailed the results of an efficiency study on e-axles, with and without an embedded motor. The research analysed different combinations of base oils, viscosity modifiers, additive packages and finished oil viscosities, to correlate fluid efficiency with fluid properties.
Energy losses vary across different lubricant regimes. Wang outlined the efficiency benefits of higher viscosity fluids in a mixed lubricant regime. However, in a full film lubrication regime with thicker hydrodynamic or elastohydrodynamic fluid, lower viscosity and higher viscosity index (VI) fluids contributed to improved efficiency. Efficiency gains are dependent on the time spent under each lubrication regime, says Wang.
Viscosity index is a measure of how much the viscosity of a lubricant changes with temperature. It indicates the stability of the oil’s viscosity across a range of temperatures. A higher viscosity index means that the oil’s viscosity changes less with temperature, making it more stable and providing consistent lubrication performance in varying temperature conditions. Oils with a high VI are typically preferred for applications where the operating temperature varies widely, as they can maintain their lubricating properties better than oils with a low VI.
Differences in efficiency were observed for various base oil types in a dry motor environment using the Worldwide Harmonised Light Vehicles Test Procedure (WLTP). In general, polyalphaolefin (PAO) was always better than Group III, says Wang. The differences are likely from traction, which is always lower with PAO, he says. However, the cost of formulating with synthetic base stocks, such as PAOs, are much higher than formulating with Group III base oils. Wang emphasised the need to balance costs and benefits during base oil selection.
E-axles can have both the e-motor and reduction gear set in one housing. An all-in-one approach where the motor is exposed to the lubricant is far more complicated, however. You must think about copper losses, iron and core losses, gear losses, windage losses and churn losses, says Wang.
Copper losses refer to the energy lost as heat due to the electrical resistance of the copper windings in the electric motor of a vehicle. This loss is proportional to the square of the current flowing through the windings.
Iron and core losses occur in the magnetic core of the electric motor. They are caused by two main phenomena: hysteresis (energy lost due to the reversal of magnetisation in the core material) and eddy currents (induced currents in the core that produce heat).
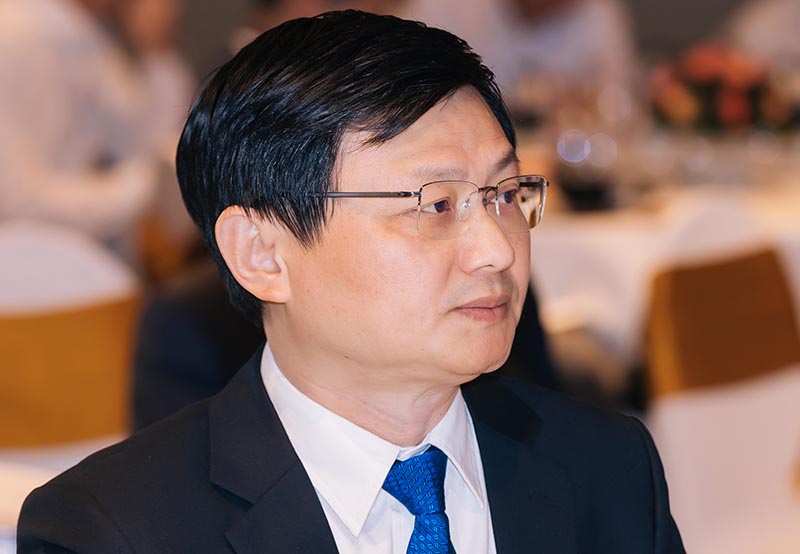
Gear losses occur in the gearbox due to factors such as friction between gear teeth, churning of lubricating oil, and bearing losses. These losses reduce the efficiency of power transmission from the motor to the wheels.
Windage losses refer to the energy lost due to the air resistance encountered by rotating components, such as the motor and the gearbox in an e-axle. This resistance creates a drag force that the e-axle must overcome, resulting in a loss of efficiency.
Churn losses, on the other hand, are related to the resistance encountered by moving parts in a fluid, such as oil. In an e-axle, churn losses occur when components like the motor and the gearbox rods move through the oil, causing it to be agitated and creating resistance. This resistance leads to a reduction in the e-axle’s overall efficiency.
In wet motor testing, PAO continued to demonstrate an efficiency benefit over Group III base oils. Although, Wang noted a turning point in the WLTP results suggesting going to extremes doesn’t continue to help efficiency.