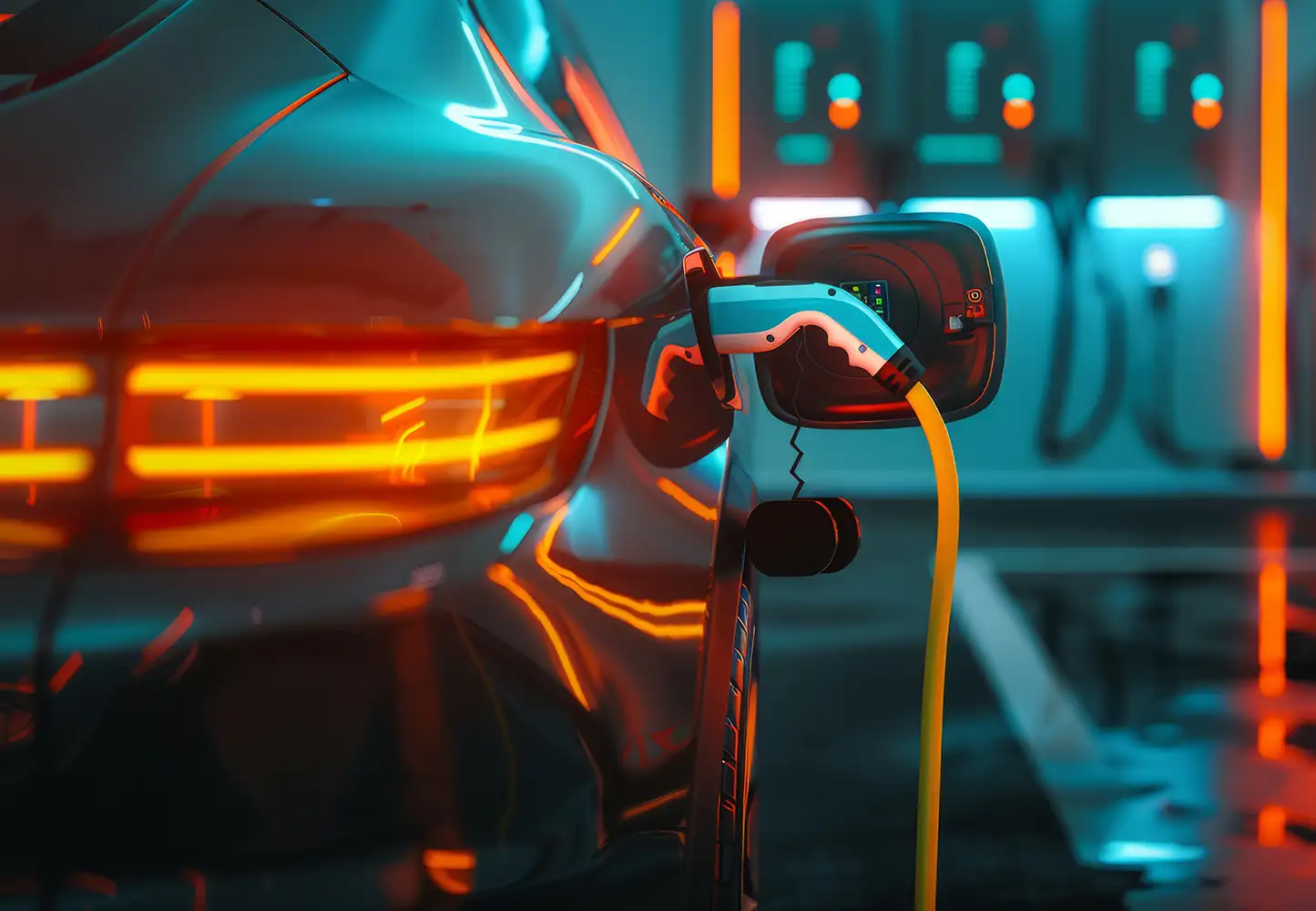
Future of lubricants in electrified tribology
In an age where industries are rapidly transitioning to electrification, the evolution of lubricants must keep pace. On October 9, 2024, during a webinar sponsored by the Asian Lubricants Industry Association (ALIA), Dr. Mathias Woydt, managing partner of MATRILUB, gave a presentation on how tribological systems are adapting to electrified environments. With more than 38 years of experience in tribology, lubrication, and disruptive technologies, Woydt explained the evolving role of lubricants in electrified systems, touching on a future where electrical properties play as much of a role as traditional factors like wear and friction.
The webinar was moderated by Paul Nai, regional business director at Lubrizol Southeast Asia Pte Ltd based in Singapore, and chair of the ALIA Technology Subcommittee.
“Today’s lubricants are mature, highly functional products designed to reduce friction and protect against wear,” Woydt said. However, the challenge lies in their adaptation to electrified tribology. Electrified systems, such as electric vehicles (EVs), wind turbines, and industrial machinery, introduce new complexities, demanding lubricants that can withstand increased contact with electrical components and elevated operating temperatures.
In such systems, lubricants now face exposure to various materials and electrical currents. The critical concern, according to Woydt, is how these lubricants maintain performance while preventing corrosion and ensuring efficient heat transfer. The introduction of wet batteries and immersion-cooled powertrains has placed new demands on thermal conductivity and electrical insulation properties.
New tribological challenges
One of the major shifts in electrified tribology is the interaction of lubricants with electrical properties. Traditional additives that protect surfaces from wear, scuffing, and reduce friction now must also contend with electrical conductivity, permittivity, and triboelectric effects. This interaction impacts how lubricants behave in environments with high voltages or amperages.
Woydt highlighted that electrified powertrains, particularly in EVs, involve different lubrication regimes. “When operating in hydrodynamic lubrication, the lubricant’s film behaves in a capacitive mode, where the bulk properties are of importance. In contrast, under mixed or boundary lubrication, the lubricant acts more like a resistor, leading to different responses depending on the system’s electrical properties, where the electrical properties of the tribofilm play a role,” he explained.
One of the most critical aspects of this transformation is the emergence of triboelectricity—the generation of electrical charges due to friction. This is a growing concern, especially in systems like wind turbines and EV drivetrains, which generate substantial triboelectric charges. To address this, Woydt emphasised the importance of testing lubricants for contact resistance, impedance, and their ability to prevent electrical arcing or to support arcing.
The role of electrical testing
A key focus of Woydt’s presentation was the evolution of testing methodologies. Historically, lubricants were tested for their mechanical properties—friction, wear, and scuffing resistance. However, as Woydt pointed out, “The future of lubricant development lies in combining tribometry with electrical testing.”
New standards are emerging to test the electrical properties of bulk lubricants. Woydt mentioned DIN 51111, the first test method fully dedicated to measuring lubricants’ electrical properties. Yet, he acknowledged that much work remains. “For greases, we still lack valid test methods to assess their electrical characteristics,” he said, suggesting that the industry needs to adopt standardised testing frameworks for both fluids and greases in electrified environments.
One of the most revealing aspects of the presentation involved testing results for greases. Woydt presented data showing how electrical contact resistance changes with temperature. At lower temperatures, certain greases maintain low resistance, but as the temperature rises, the resistance dramatically increases. This variability could lead to failure in electrical systems if not properly accounted for.
For example, he explained, “If a grease’s contact resistance is not stable across temperature ranges, it may fail in high-temperature applications, leading to triboelectric effects and system malfunctions.” Therefore, greases designed for use in electrified tribological systems must be formulated to maintain consistent contact resistance across varying conditions.
In addition to contact resistance, friction was also a factor. Interestingly, Woydt’s tests demonstrated that while friction coefficients remained largely unchanged between greases, the wear tracks showed significant differences based on contact resistance. This finding suggests that contact resistance may be a more reliable indicator of a lubricant’s effectiveness in electrified systems than friction alone.
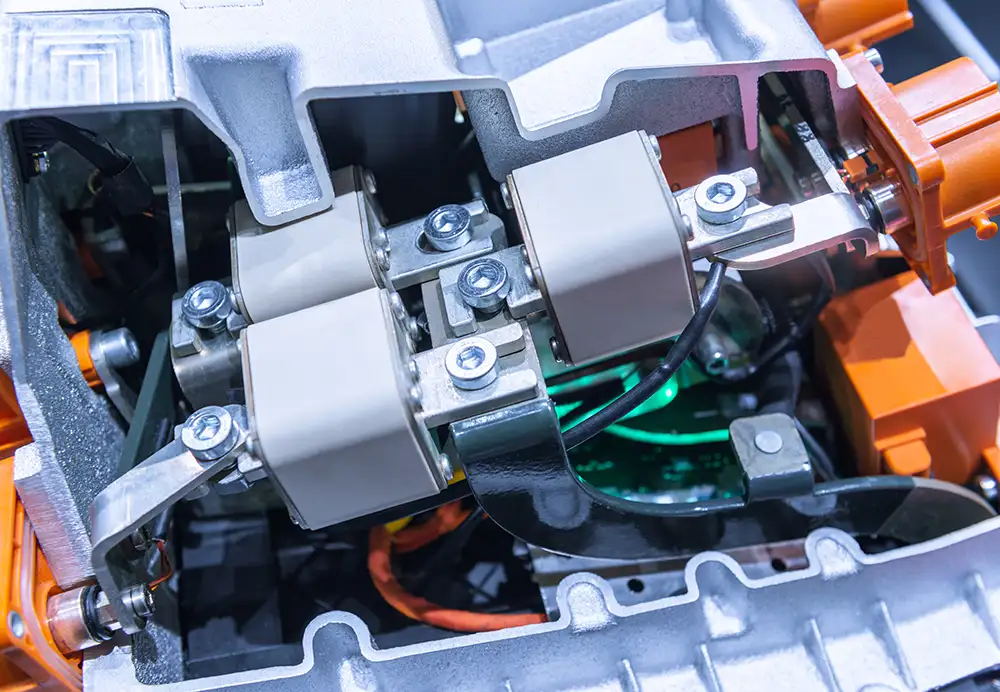
Developing for the future
The takeaway from Woydt’s presentation is clear: lubricant manufacturers must innovate to meet the needs of electrified systems. This involves more than just adapting existing formula—it requires a fundamental rethinking of lubricant design, with an emphasis on electrical properties and responses to voltages and amperages, alongside traditional tribological performance.
To this end, Woydt emphasised the need for collaboration across industries, citing the work of various standardisation committees, including SAE J3200 and ASTM CS97, both of which are developing testing methodologies for electrified drivetrains. He also mentioned that China and Germany are leading the way in these developments, with Southwest Research Institute and German Research Association for Powertrain (FVA) taking prominent roles.
Finally, Woydt encouraged manufacturers to develop lubricants with invariant electrical properties across a range of temperatures, ensuring that lubricants remain unaffected by and safe under a variety of operating conditions. “The electrification of tribological systems reshuffles the proper selection of additives and base oils,” he concluded, adding that lubricant developers now have the tribometric tools to address these challenges.
For manufacturers, the message is clear: innovation in lubricant development is essential for ensuring the safe and efficient operation of electrified machinery in the years to come.