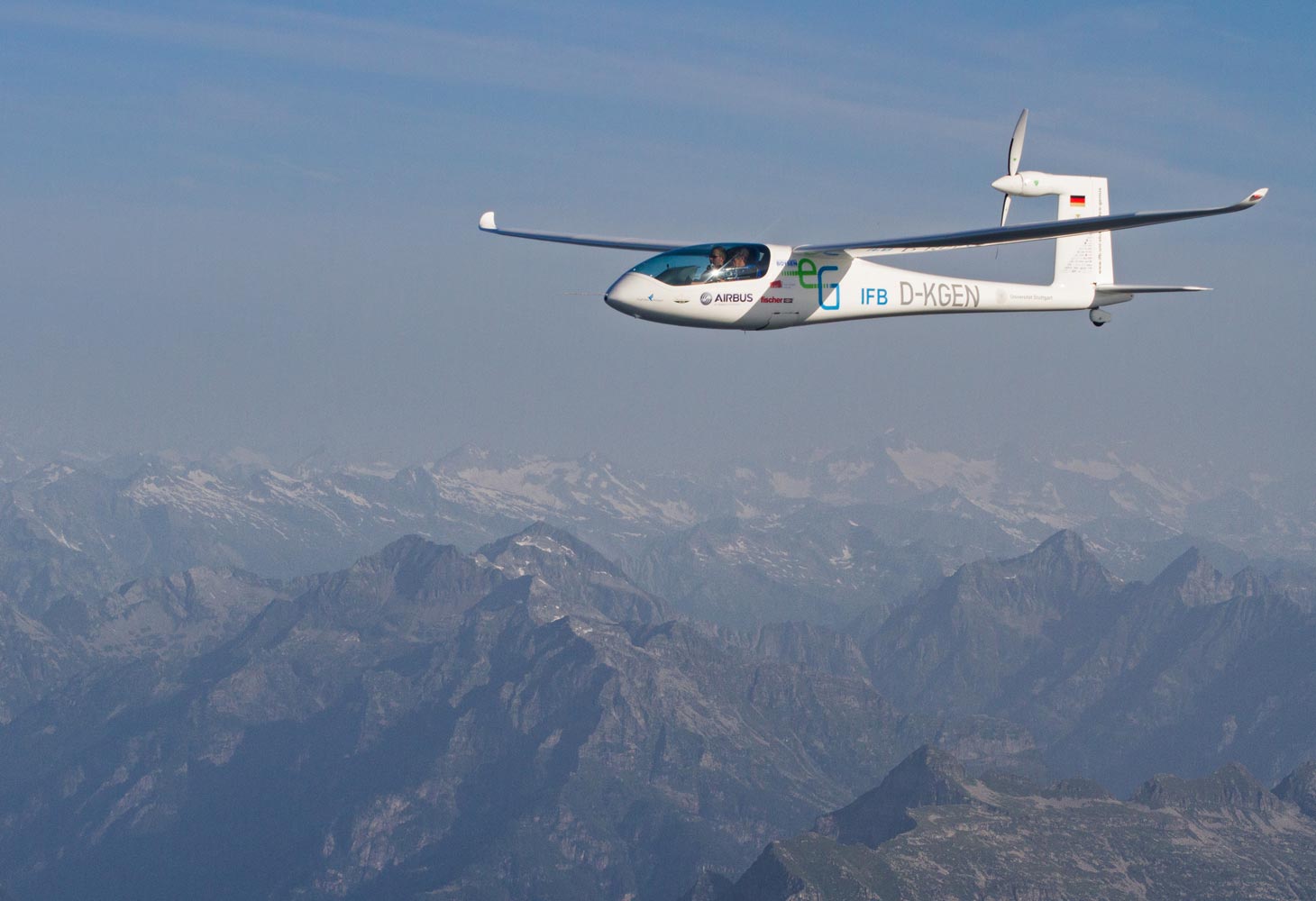
For how long will ashless dispersant aviation engine oils be around?
By Dr. Raj Shah, Dr. Mathias Woydt, Stefan Lim
When asked for an example of an air-cooled engine, many people will mention the Porsche 911 Carrera, known for its top-of-the-line air-cooled flat-six engine, the so-called ‘Boxer’ engine. Known by many as the ‘air-cooled 911s’, the final iteration of Porsche’s flat-six air-cooled engine was discontinued after the 1998 model year in favor of a water-cooled engine. It is among the last consumer automobiles to be produced with an air-cooled engine.1, 2
In contrast the aviation industry uses a mix of both air- and water-cooled engines, even favoring the air-cooled option in the case of aircraft piston engines. This preferred cooling method by the aviation industry hints at the reason behind the ubiquity of ashless dispersants in aviation engine oils.
Castor oil was the oil of choice for aircraft oils at the beginning of the aviation era because of their good lubricity. These oils were dropped in favor of mineral-based oils around 1925-1935. At the time, these oils did not contain any additives and compared to today’s engines, oil consumption was extremely high, with engines requiring regular top-ups.
Additives, such as ashless dispersants, help to reduce engine oil consumption. But before delving into the importance of ashless dispersants in aviation engine oils, it is important to understand what an ashless dispersant is. Ashless dispersants help prevent metallic deposits from forming in engines, which can cause pre-ignition and can result in catastrophic damage to the engine.3 An ashless dispersant works by dispersing accumulated ash out of the engine’s components to prevent buildup and excessive wear.
The Aircraft Owners and Pilots Association (AOPA) states that “ashless dispersant oils have an additive in them to aid in scavenging debris and carrying it to the filter or screen.”4 AOPA further states that “This is a very important quality, given the relatively high wear of aircraft engines and the amount of combustion acids and other contaminants that get past the cylinder rings and valves.” In effect, an ashless dispersant functions by surrounding unwanted debris to prevent it from settling and causing wear and other damage such as pre-ignition.5
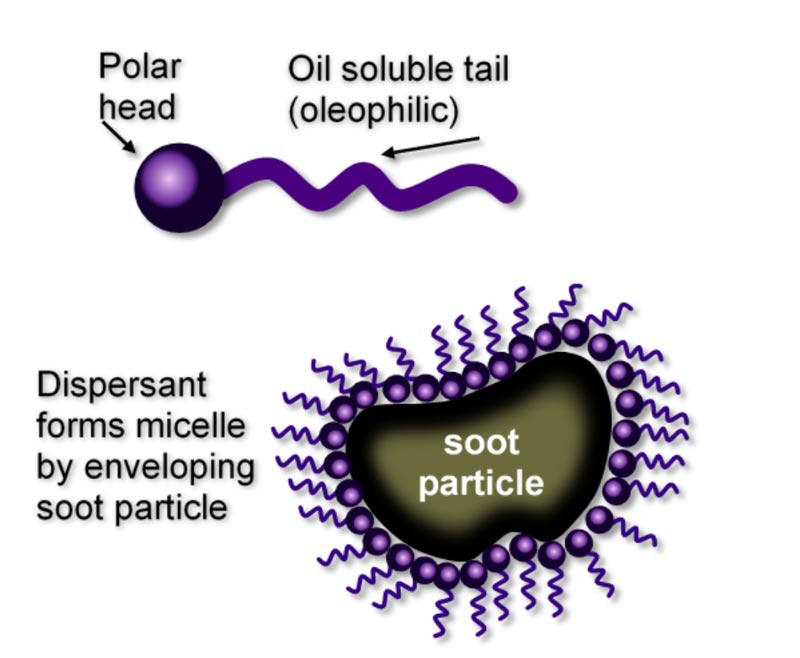
Aircraft piston engines deviate from the design and construction of modern automobile engines on many counts, most notably in their powerbands. An automotive engine typically has a redline of around 6,000-7,000 revolutions per minute (rpm) and rarely operates at peak power for more than a few seconds at a time, whereas an aircraft engine typically outputs peak power at around 2,700 rpm and operates at this level for the majority of its operation,6 with the higher end being those of World War II (WWII) aircraft, which peaked at 3,200 rpm.
Another difference is in the overall objectives in engineering these types of engines. Currently, the automotive industry is focused on improving fuel efficiency by downsizing, and providing convenience for both vehicle drivers and passengers. In contrast, airplane engines are focused on reliability and simplicity. A prime example of this is the Lockheed Constellation, which is a World War II aircraft that was named the “safest 3-engine plane,” despite its 4-engine design, because overseas flights often resulted in one engine dying along the way.
Water-cooled engines in World War II were mainly V12 by design and air-cooled engines followed a radial single or double star design with seven or nine cylinders per star. The power density improvements during WWII were rapid; aircraft engines had 20-50 litres in displacement and were often turbocharged, originally by Germany, followed by supercharging by the Allied Powers. The fuels used at the time were rated at or below 90 octane, except for an increase to 100 octane, even up to 150 octane during the war, in contrast to today’s lead- and sulphur-free 100 octane.
These engines reached around ~50 HP/litre and in overboost, by water-methanol injection, up to 50% more for up to 90 seconds. Today’s mass-produced gasoline passenger car engines can output 100-150 HP/litre, a clear advancement in engine technology over the century. A problem that plagued both sides of the fight during World War II was the reliability of the engines, even without enemy contact. Soot and deposit formation due to limited and skipped maintenance, limited additive knowledge and the resulting pre-ignition caused major issues. This was the practical birth of synthetic engine oils and functional additives. The German Luftwaffe used a base oil with an ash-free blend of a diester with a poly (ethylene) oil7 blended with an extreme pressure/anti-wear additive ‘Mesulfol II’, a sulphur carrier. In 1944, the U.S. Air Force in P-38, P-47, P-51 and B-25⁸ began to use an ashless polypropylene glycol from Prestone (Union Carbide). Both engine oil concepts were retired after World War II, but polyalkylene glycols (PAGs) have some auto-detergent and dispersant capabilities.
A comparison between an automotive car engine from the 1960s and one from the present shows several obvious changes and advancements while a similar comparison between two aircraft engines depicts two very similar-looking engines. Comparisons between two engines from 1967 and 2015 are shown in Figures 2 and 3.
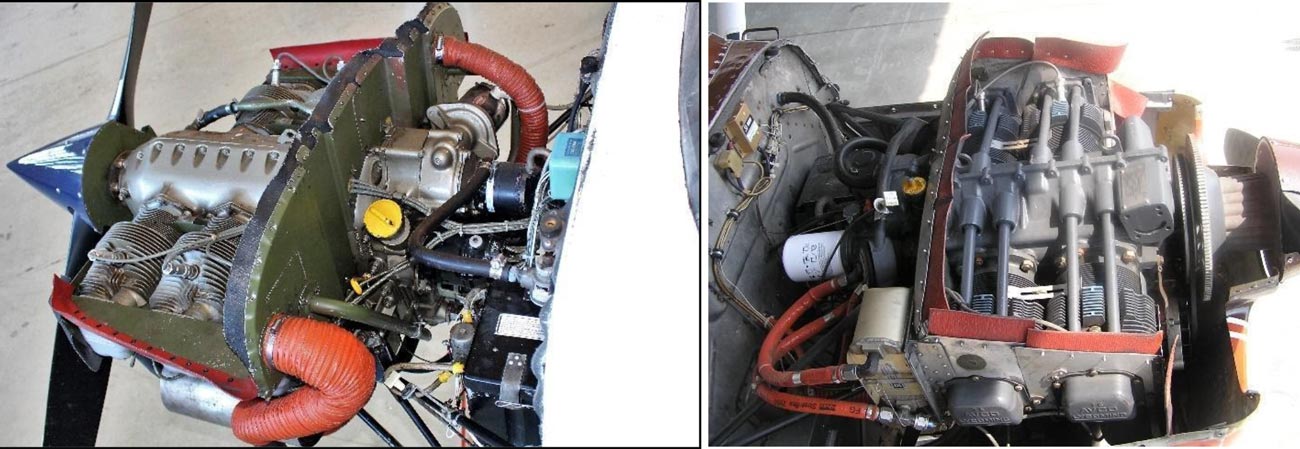
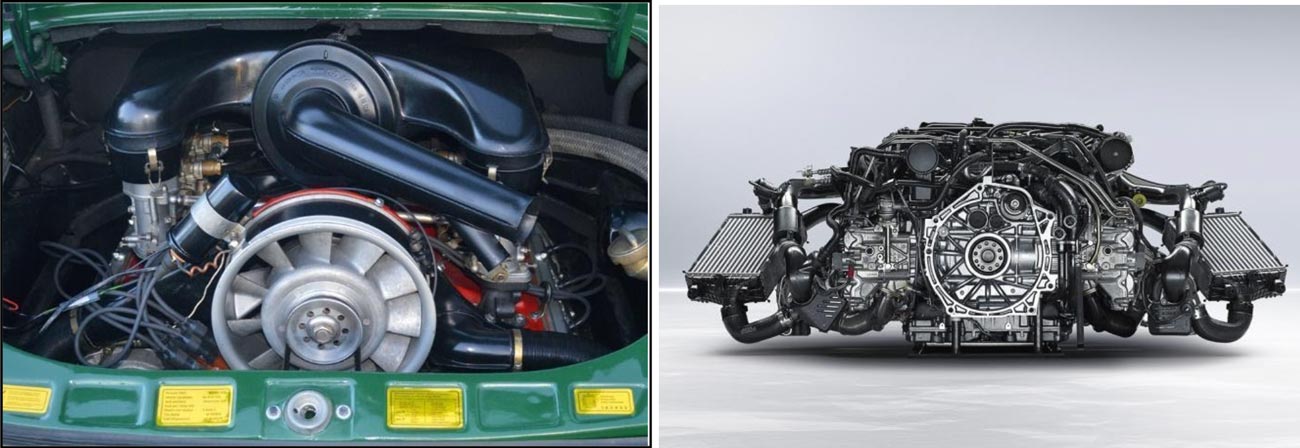
The comparison between automotive and aviation engines is critical to understanding why ashless dispersants are still common in aviation engine oils, but are rarely mentioned, when discussing automotive engine oils. A Google search for ‘ashless dispersant’ will yield results almost entirely pertaining to aircraft engines and aircraft engine oils. The advanced technology in new cars is aimed at keeping engines as pristine as possible for as long as possible to squeeze every extra mile out of a tank of fuel, not to mention that electric vehicles don’t need engine oils. However, the older designs of aircraft piston engines lend themselves more towards the car engines of the 1960s that relied on some deposits being left behind in the engine and were designed to not run under ‘like-new’ conditions for their entire life.
For this reason, automakers tend to recommend full-synthetic and mid-SAP (<0.80 wt.-% sulphated ash) or low-SAP (<0.50 wt.-% sulphated ash) oils with complex additive packages while aircraft manufacturers typically approve the use of two much more rudimentary types of oil: straight mineral oil and ashless dispersant mineral oil. SAP stands for sulphur, ash and phosphorus. Straight mineral oil (API Groups I-III) is essentially the oil that comes out of a refinery and is commonly recommended for the break-in period of a new aircraft piston engine.
According to retired AeroShell lubrication expert Ben Visser, “the old hard chrome used to bring cylinders into specification, where you had to actually wear down the parts — the particles worn off work as a lapping compound.”13 After the break-in period, the recommendation changes to prevent extra, unnecessary build-up. Most aircraft manufacturers will recommend ashless dispersant oil over straight mineral oil post-break-in to flush out additional metallic particles and contaminants.
Despite the strong persistence of these ashless oils in aircraft piston engines however, there is a potential challenge for the long-term endurance of ashless dispersant oils: electric aircraft. In 2014, Klaus Ohlmann broke seven world records with the two-seater e-Genius airplane. Among these records were a speed record of 142.7 mph (229.7 km/h) and an overall flight of 313 miles (504 km). These results are not groundbreaking when all aircrafts are considered, but knowing that the e-Genius completed these feats using only an electric motor with a single battery as its power source makes this a different accomplishment altogether.14, 15 To make this feat more impressive, the e-Genius only consumed one-fifth of the energy that would have been consumed in a fuel-powered two-seater plane for the same trip.15 These results are promising for the future of electric aircraft, but what do they mean for aircraft oils?
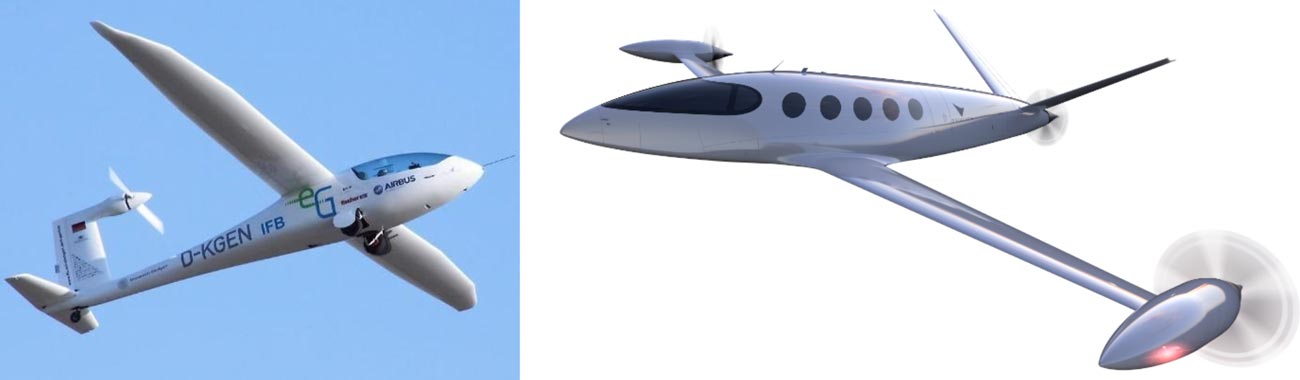
The e-Genius of the University of Stuttgart in Germany looks futuristic like a glider, but other more sophisticated e-plane concepts also exist. Electrification as a vision of the future is ‘en vogue’ for aeronautics, from full-electric to hybrid aircraft. Eviation presented the commuter plane ‘Alice’ for nine passengers with a projected range of 600 miles. Airbus proposed the e-fan X for more passengers, where one engine is replaced by a 2MW electric motor.17 The experimental all-electric airplane of NASA X-57 is equipped with large electric wingtip motors for cruise and 12 small electric motors with fold-in propellers for take-off.
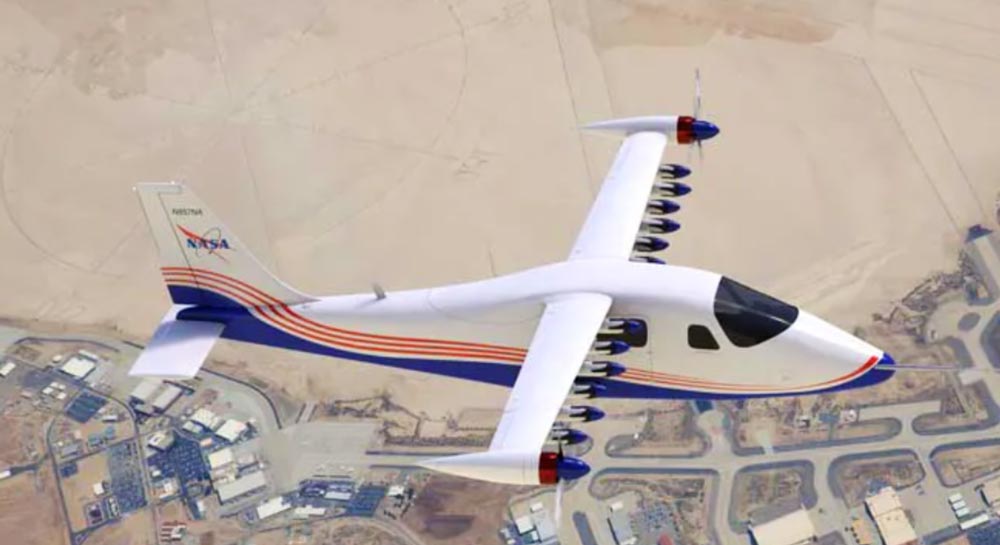
Vertical take off and landing (VTOL) are another group of electrically powered airplanes. They focus on regional air mobility and connect city centers as ‘urban air taxis’, because they need only a pad for landing. Examples are: CityAirbus, Daimler Velocopter, BOEING NEXT, and Lilium jet.
It is evident that the world is shifting in favor of electric technology. This technology has established a presence in the automotive industry, with vehicles such as the Chevrolet Volt, Nissan Leaf, Toyota Prius Prime, and Tesla’s family of vehicles growing their sales year after year.19 Planes such as the e-Genius also prove that it is possible to share this technology with the aviation world as well, but this doesn’t mean that the advent of electric aircraft means the demise of aircraft engine oils.
According to General Aviation News, the average age of a General Aviation* plane is 50 years old, putting the average year of manufacture at 1970.20 By comparison, the average age of a consumer car is only 12 years old, putting cars at an average manufacture date of 2008.21 In theory, this means that the mandatory implementation of a new feature or regulation would take until 2032. This makes it much harder to change aviation technology, for better or for worse. In the case of aviation engine oils, this prevents technology, such as full-synthetic oil with complex additive packages, from becoming commonplace in airplanes, but it also helps ashless dispersants persist despite the current global interest in alternative fuels and stricter emission standards.
It is clear that aviation competes with electrification. The goal is a CO2-neutral transportation and in this case, aviation is ahead of the automotive industry. ASTM D7566 is the key specification for conventional jet fuels, currently with seven annexes, which specify different pathways for sustainable aviation fuels (SAF), allowing up to 50% volume of sustainable aviation fuels from different sources in terms of biomass resources and processes. This can be a blueprint for internal combustion engines. BMW recently announced that it has approved 100% renewable diesel fuel, known as HVO100. HVO100 is a chemical copy of a hydrocarbon-based diesel fuel. Porsche promotes the development of synthetic fuels or eFuels, which are produced from CO2 and hydrogen using renewable energy. Another option is fuel blended with 33 vol.-% of hydrogenated used cooking oil, to produce petrochemical diesel fuel, as proposed by Volkswagen known as R33 BlueDiesel.
The mechanics of an aircraft engine have remained largely the same over the past half-century while the mechanics of an automobile engine have evolved significantly. Despite this contrast in development, electric technology is expected to permeate through both industries in the coming years. While this may cause a reduction in aircraft engine oil use, the persistence of old aircraft with simple piston engine designs will likely result in the persistence of ashless dispersant aviation engine oils. Ashless dispersant oils may not see many new developments and improvements in the coming years, but like the aircraft they service, they will likely be around for many years to come.
*General Aviation is defined by the Aircraft Owners and Pilots Association as all civilian flying except passenger airline service.22
References
1 https://newsroom.porsche.com/en/history/porsche-911-seven-generations-part-4-type-993-16486.html
2 https://www.aviationsafetymagazine.com/features/air-cooled-engines/
3 https://www.avweb.com/ownership/oil-myths-debunked/
4 https://www.aopa.org/news-and-media/all-news/2013/february/19/all-about-oils
5 https://www.machinerylubrication.com/Read/31107/oil-lubricant-additives
6 https://www.flyingmag.com/aircraft/do-car-engines-make-good-airplane-engines/
7 H.L. West, Major Developments in Synthetic Lubricants and Additives in Germany, Journal of the Institute of Petroleum, Vol. 34, 1948, p. 774-815
8 C. Kratzer, D.H. Green and D.B. Williams, New Synthetic Lubricants, SAE Journal (Transactions), vol. 54, No. 5, May, 1946, p. 228-238
9 https://www.007museum.com/CESSNA-172-O-300-Dc.jpg
10 https://cessnaowner.org/wp-content/uploads/2015/05/HAD3.jpg
12 https://presse.porsche.de/presskits_until_2015/motor_shows/2015/IAA/HighRes/html/en_26480_0.html#image_26641
13 https://www.planeandpilotmag.com/article/theres-more-to-oil-than-you-think/
14 https://www.uni-stuttgart.de/en/university/news/press-release/e-Genius-breaks-world-records/
15 https://www.theatlantic.com/sponsored/thomson-reuters-why-2025-matters/electric-flight/208/
16 http://cafe.foundation/blog/smartflyer-challenge-electric-airplanes-fill-swiss-skies/
17 https://www.bbc.com/future/article/20200617-the-largest-electric-plane-ever-to-fly
18 https://www.nasa.gov/centers/armstrong/features/Progress-on-X-57-Cruise-Motors-and-Wing.html
19 https://insideevs.com/news/392375/top-10-electric-cars-sales-us-2019/
20 https://generalaviationnews.com/2019/05/27/aging-pilots-aging-airplanes/
21 https://www.caranddriver.com/news/a33457915/average-age-vehicles-on-road-12-years/
22 https://www.aopa.org/-/media/files/aopa/home/advocacy/what_ga.pdf