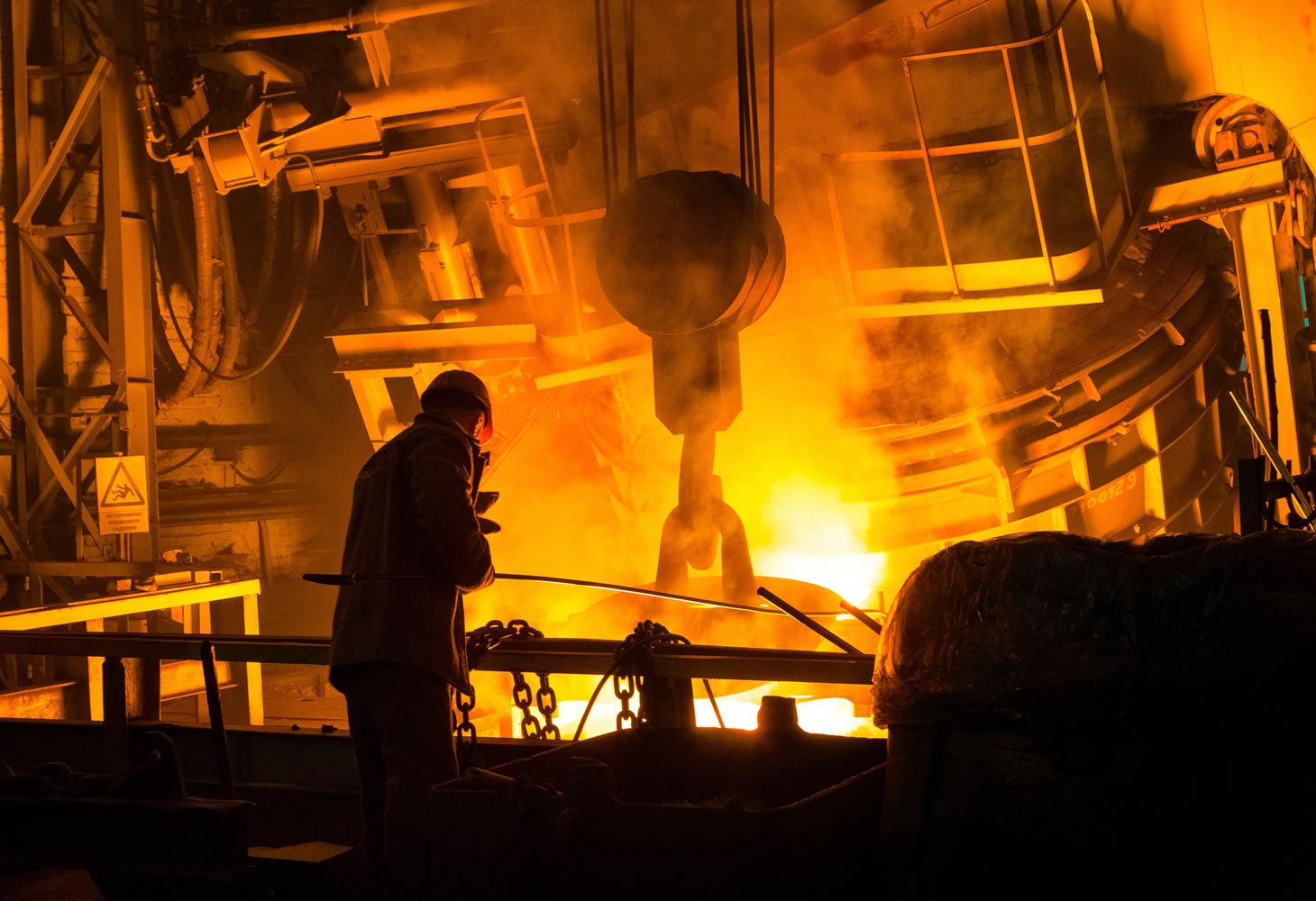
Electrolytic hydrogen essential to decarbonise steel industry
Iron and steel manufacturing is an energy and carbon-intensive process. It was estimated to account for 7% of global carbon dioxide (CO2) emissions in 2020, making it one of the most energy-demanding industries in the world. The reduction of iron ore in blast furnaces using a concentrated form of coal (coke) is the major source of CO2 emissions.
In some industries, the path to decarbonisation is (fairly) straightforward. In transportation, for example, the fossil-fuel hungry internal combustion engine is slowly being displaced by partially or fully electrified vehicles. Decarbonising steel manufacturing is perhaps not as clear-cut. Steel is a critical product that plays a central role in the transition to carbon-free energy. It is used heavily in the construction of utility-scale solar farms; nuclear, hydroelectric, and wind power generation; and electrical power transmission and distribution infrastructure. However, when it comes to decarbonisation, every industry needs to play its part.
A report, published by the U.S. Energy Information Administration (EIA) in February 2022, explores the decarbonisation pathways of the iron and steel industry and their implications on energy consumption and CO2 emissions, in four specific regions. IEO2021 Issues in Focus: Energy Implications of Potential Iron- and Steel-Sector Decarbonisation Pathways highlights the critical importance of electrolytic hydrogen in decarbonising the steel manufacturing sector.
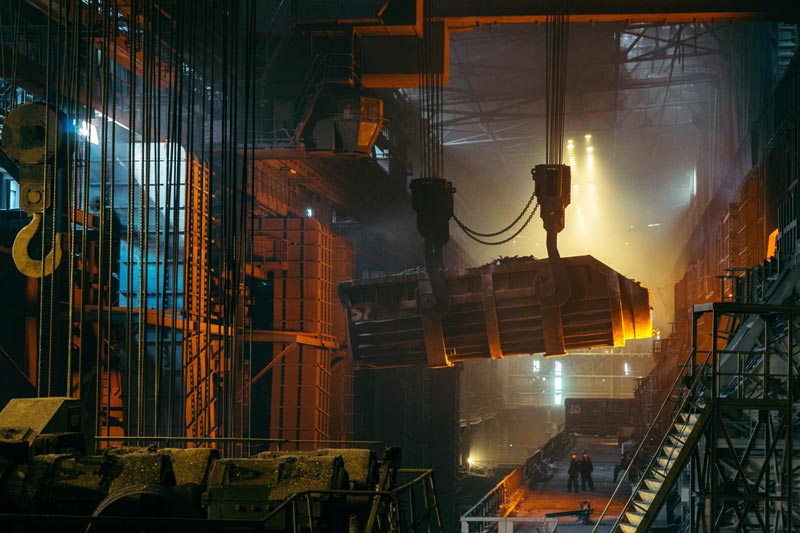
The manufacture of crude steel is a two-step process with two possible pathways. Two-thirds of crude steel is produced by a traditional method whereby blast furnaces (BF) use coal to produce “pig iron”—or crude iron in the form of oblong blocks. The iron is then converted to virgin crude steel using basic oxygen furnaces (BOF) in a steel mill.
The remaining third of steel production uses a less energy-intensive method employing electric arc furnaces (EAF). EAFs primarily make use of scrap steel and produce recycled steel products. However, they can use direct reduced iron (DRI) to produce virgin steel. The EIA report calls for greater recycling to continue to reduce the carbon intensity of steelmaking, though, it underlines concerns around the availability of scrap metal in some regions and issues with purity after repeated recycling.
The report examines the energy consumption and CO2 implications of a reduction in BF‐BOF steel manufacturing and greater adoption of electric arc furnaces. An increase in the DRI percentage of EAF manufacturing is necessary to compensate for lower BF-BOF virgin steel production. Though, a shift to DRI-EAF is not necessarily associated with lower carbon emissions. The DRI-EAF process usually uses natural gas or coal to heat the iron ore and synthesis gas (syngas)—a mixture of hydrogen (H2) and carbon monoxide (CO), to reduce the iron ore into iron.
To produce low-carbon, high-quality steel, the EIA outlines two key components—the use of electrolytic H2 as a reducing agent in the direct reduced iron process, and powering electric arc furnaces with renewable power derived from solar, wind, biomass, waste, or geothermal electricity. Hydrogen has been demonstrated as the sole reductant in the DRI process on a small scale, says the EIA.
Hydrogen by itself is not necessarily the solution to the environmental woes of the steel industry. In 2018, 99% of hydrogen production was generated using fossil fuels, with a meagre 1% through electrolytic processes. “In the years ahead, electrolytic H2 powered by renewable energy will be essential to decarbonising the steel industry,” says the EIA.
Despite a potential shift to the more environmentally friendly EAF process, the rate of emissions reduction will not be uniform. The report indicates that both the magnitude of increase in EAF and the power generation profile of individual regions will influence carbon reductions and there will be economic challenges until renewable-based electrolytic H2 production achieves cost parity with natural gas‐based H2.
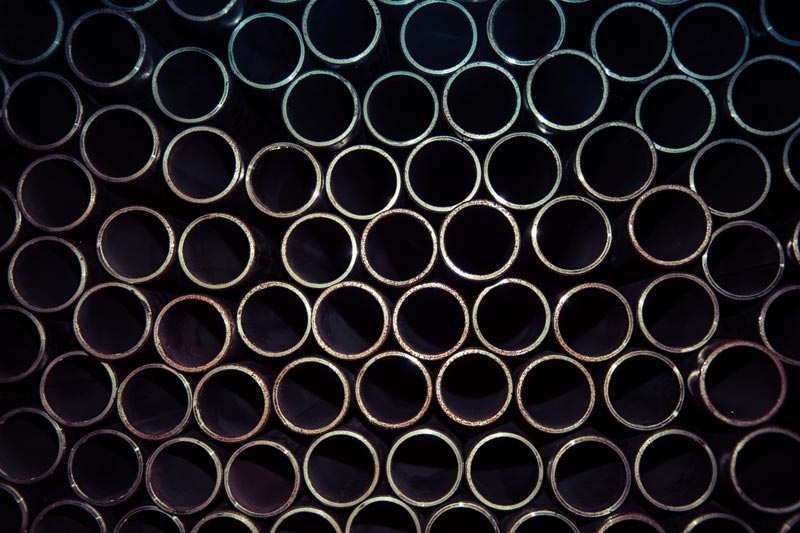
Four key steelmaking regions are examined in the EIA report: China, Japan, South Korea and OECD Europe. The size and composition of the respective steel industries and existing decarbonisation plans were cited as the rationale for the regional focus. China, for instance, currently accounts for half of global steel production.
Two scenarios were modelled—an early adoption case (EAC) and a delayed adoption case (DAC). The gross output of the steel industry remains the same in both iterations. Share of steelmaking using BOF-produced steel falls approximately 30% to 2050 in all regions, except China, and it is assumed that DRI will account for 40% of metallic input to electric furnaces, to compensate for lower BF‐BOF production of virgin steel, in both scenarios.
The key difference between the two scenarios is the timing for cost parity between electrolytic H2 and fossil fuel-based H2. EAC assumes cost parity in 2030, whereas DAC is delayed a further 10 years. The delay impacts the balance of natural gas and renewable power used to make hydrogen. In both cases, natural gas consumption increases (versus a reference case) due to the need for supplemental DRI to compensate for lower BF‐BOF virgin steel production. The EAC scenario trends slightly lower in natural gas consumption and slightly higher in renewable power consumption.
By 2050, DRI produced by electrolytic H2 and powered by renewable energy reaches 48% in the EAC scenario and the share of electric furnaces powered by renewable energy is the same. DAC reaches only 31% in the same timeframe.
A decline in coal use and a rise in electric power is predicted in all regions under both scenarios, as well as a fall in steel industry carbon emissions. The report indicates that “generally speaking” there will be little difference in CO2 emission between EAC and DAC in individual regions— primarily because the difference between the early and delayed adoption cases is relatively small compared to overall industry emissions—which EIA says are dominated by coal for BF production. A smaller, 12% increase in EAF production in China dictates a lower relative decrease in CO2 emissions compared to the other regions.
South Korea’s increase in EAF production (34%) is greater than OECD Europe (23%), however, declines in steelmaking emissions are substantially higher in Europe (28% for DAC and 31% for EAC) compared to South Korea (19% and 22% for DAC and EAC, respectively). The authors credit the influence of the power generation profile of the individual regions, with Europe boasting a much higher renewable generation share in the power sector.
China continues to rely heavily on coal-fired technologies. 90% of production is via BF-BOFs, many of which are relatively new, with a useful lifespan of over 40 years. To achieve the reductions in energy intensity in the EIA report, many of these facilities would need to be retired ahead of their typical end of life. Japan (76%) and South Korea (68%) also rely heavily on BF-BOF production of crude steel. However, Japan has committed to shifting its energy mix to rely on renewable‐based hydrogen and fossil‐fuel H2 with carbon capture and storage (CCS).
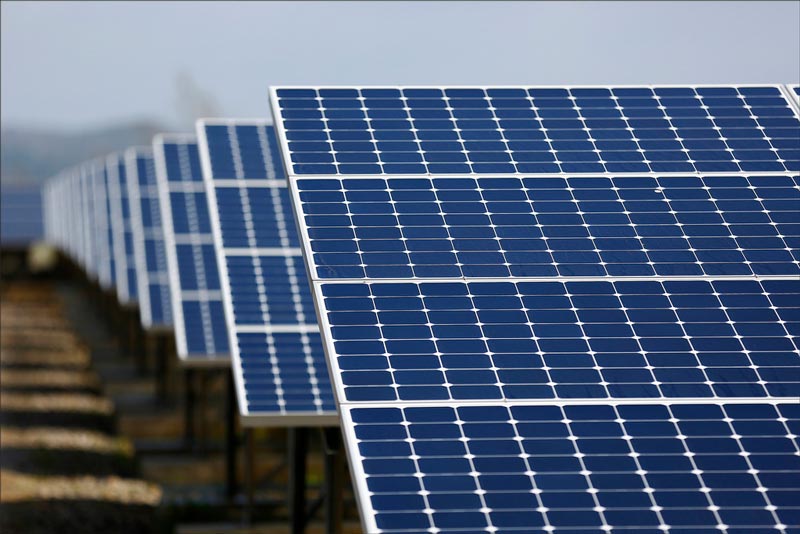
OECD Europe (51%) is well-positioned to transition to low‐carbon steelmaking, with the EIA report highlighting the availability of existing natural gas pipelines to transport H2, high volumes of scrap metal availability and stringent CO2 policies. Natural gas availability in Europe could change however with the recent Russia-Ukraine war. Russia accounted for about 45% of the EU’s natural gas imports and 40% of its entire natural gas consumption. The EU has announced a strategy to reduce its reliance on natural gas from Russia by two-thirds by the end of 2022.
Additional renewable electricity generation of 385 billion kilowatt-hours (BkWh) is required for China in 2050 to achieve the EAC scenario, an 8.7% increase over the reference case level, or a lesser 314 BkWh generation for DAC. The research anticipates that additional renewable power would be achieved through the combination of growth in solar and battery storage.
Japan needs a 10% increase in power generation, versus the reference case, 424 BkWh in EAC, which experts suggest would be satisfied through growth in solid waste and wind, supplemented by coal‐fired and natural gas‐fired generation to ensure grid reliability. South Korea requires additional renewable power generation of 58 BkWh in 2050 in EAC, a sizable 27% increase on the reference. After 2030, a shortage in the availability of high‐quality solar resources means wind resources start to become more economically favourable for South Korea.
OECD Europe will require an additional 135 BkWh renewable power generation by midway through the century, a 4.5% increase. For the DAC, additional demand reaches 98 BkWh. The authors expect growth in wind generation to be the predominant source of renewable‐powered electricity in the region.
The EIA report highlights several key challenges and uncertainties concerning the decarbonisation of the steel industry including economic challenges associated with replacing current BF‐BOF capital stock, decarbonisation of upstream processes—such as the mining of iron ore—and downstream processes, and the truth that there are multiple emerging technologies for creating hydrogen from renewable resources, such as biomass gasification. The authors also noted the competition between fossil‐fuel methane reforming and electrolytic H2 production methods.