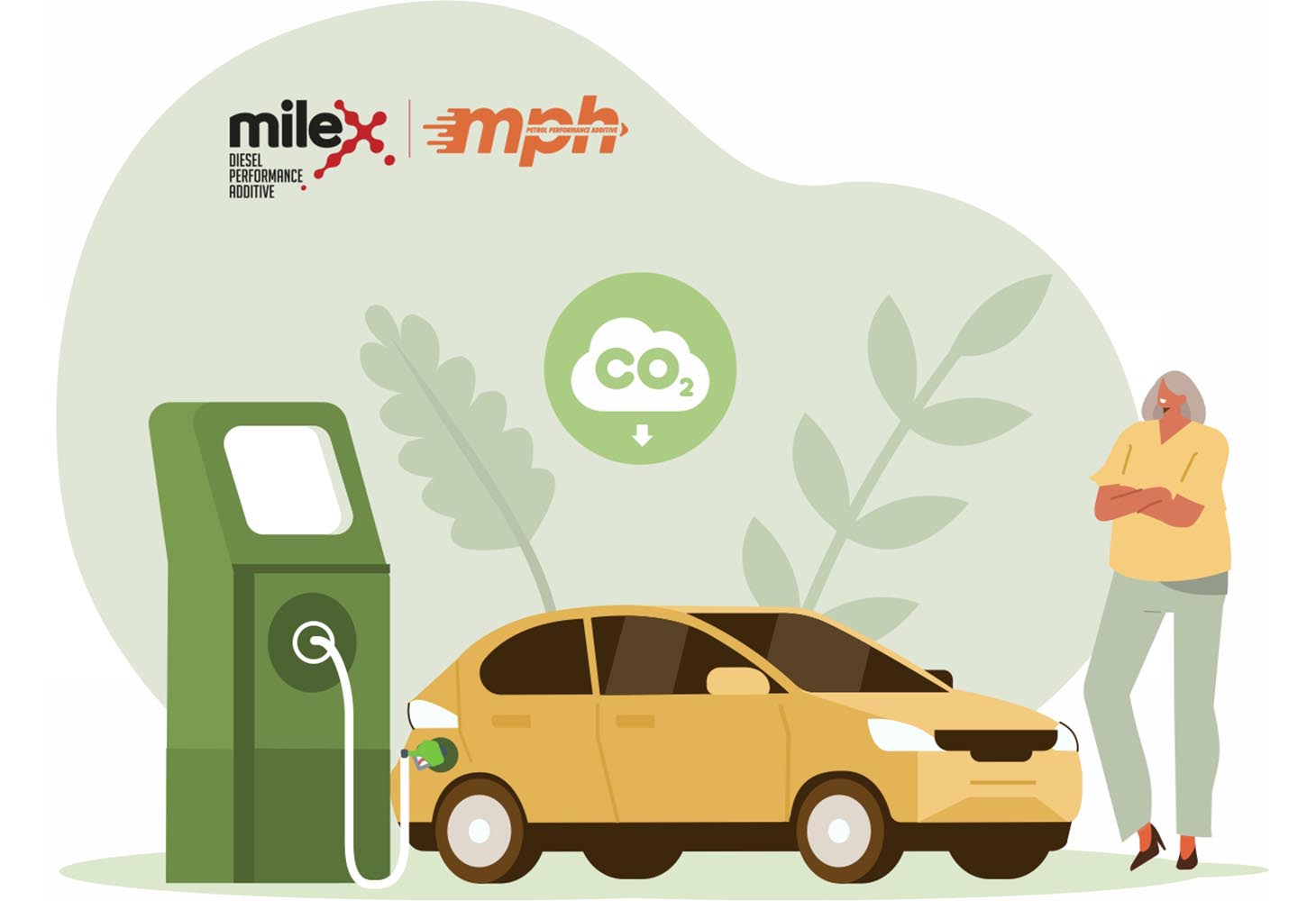
Dorf Ketal Performance Fuel Additives. Novel Fuel Additives Technology for Sustainability
by Reinaldo Nascimento, Global Market Lead, Performance Fuel Additives, Dorf Ketal PVT, and Aileen Valera, Global Technical Lead, Performance Fuel Additives, Dorf Ketal PVT
Abstract
Sustainability is becoming a key driver for innovation in the 21st century. Climate change is happening now and continues to be directly attributed to increased emissions and greenhouse gases. Extensive attention is given to excessive carbon dioxide (CO2) emissions due to fossil fuels combustion. Following the 2015 Paris agreement, 195 countries agreed to limit global temperature rise to 2°C by the end of the century and continue efforts to reduce it further to 1.5°C. To support this global effort, Dorf Ketal has developed novel additive technology that improves the combustion of liquid fuels used in internal combustion engines. This results in improved vehicle acceleration, power output and reduced engine out emissions for a given volume of fuel consumed. The reduction in fuel consumption directly contributes to global efforts to reduce carbonization including CO2. This paper provides an overview of the data developed to date and the potential impact should the technology be deployed in a timely and appropriate manner.
Introduction
Humans have traditionally grown their economy by burning fossil fuels, thus increasing carbon dioxide emissions, one of the key causes of the greenhouse effect and, therefore, global warming and climate change. Climate change is currently one of the biggest ecological and social challenges our global society has faced to date. The Global movement on climate change began in 1992, during Rio 92 (Rio de Janeiro, Brazil); however, the 2015 Paris agreement was pivotal in terms of action, as 195 countries agreed to limit the rise in global temperature to 2 °C until the end of the century and continue efforts to reduce it to 1.5 °C thereafter.
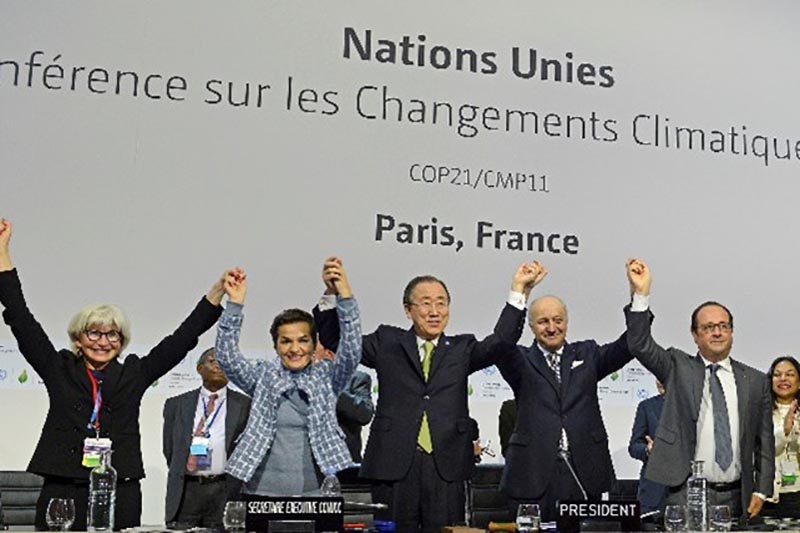
The ongoing process to achieve this goal is known as “decarbonization.” Decarbonization is the process of reducing carbon emissions into the atmosphere, especially its form as carbon dioxide (CO2). Its objective is to support a global economy with reduced emissions to achieve climate neutrality through the energy transition. Decarbonization requires an energy transition process, such as structural changes, to reduce or eliminate carbon from energy production. At the end of the scale, this includes electrifying the economy using only alternative sources of clean energy that the planet earth can absorb. However, this will be both a long process and challenging to achieve. As a result, there will be a transition period in which there will be a hybrid energy matrix, with several energy sources contributing to supply the total demand. This energy matrix will continue to include the use of fossil fuels, seeking, however, more efficient alternatives for their use.
Lobby groups such as the eFuel alliance work to push for a technology-neutral approach to decarbonization, but the end of the internal combustion engines (ICE) era will happen. The question is how quickly. Whilst the trend is clear, recent estimates suggest that more than 60% of the global car park will still utilize ICEs by the end of the current decade. This means that technology solutions will continue to be required if there is any chance to meet the emissions reduction targets being discussed throughout various platforms and industry / political bodies.
This work will explore the use of performance additives for fuels as one very real and already proven solution to contribute to these emissions reduction targets and achieve sustainability for our future energy demand.
Diesel and gasoline emissions
In 2019 (pre-pandemic), world diesel consumption reached 27.9 million barrels per day. Gasoline reached a worldwide consumption of 26.36 million barrels per day. Consuming these fuels causes the emission of CO2 into the atmosphere, as well as other harmful contaminants, such as SOx and NOx. Furthermore, the emission of solid particles (soot), a predominant component of pollution in big cities, causes severe damage to people’s health, especially with respect to respiratory infections.
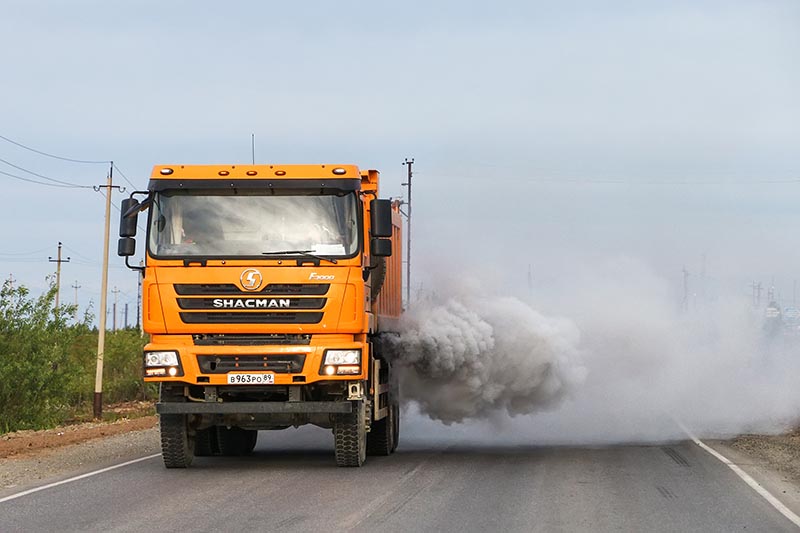
Based on diesel and gasoline consumption data for 2019, it is estimated that 21,391,337.25 tons of CO2 were released into the atmosphere daily.
Several initiatives are being adopted to reduce emissions derived from the use of diesel and gasoline and contribute to the sustainability of our energy demand namely:
- Making more efficient engines.
- Adding biofuels to fossil fuels.
- The introduction of synthetic fuels.
- Replacement of combustion vehicles with electric and hybrid vehicles.
- Improvement of fuel quality via production processes, such as hydrotreatment and chemical additives.
- Improved fuel efficiency using performance chemical additives.
- Efficient driving (hypermiling).
Except for the items related to “improving fuel efficiency through the use of performance chemical additives” and “hypermiling,” all others require significant capital investments, thereby adding an additional time factor, before which any return on investment can be expected and further delaying emission and sustainability benefits.
Working on improving fuel efficiency via the use of performance fuel additives requires no capital investment, and benefits can be realized immediately when using such technology. For example, suppose all the diesel and gasoline consumed in a single day, considering the 2019 volumes, had used additives to improve combustion efficiency by achieving an average fuel economy of 5%; in that case, it could have stopped emitting 1.07 million tons of CO2 daily into the atmosphere.
OEMs like Hyundai[1], believe that the industry can respond quickly and effectively to the need for synthetic and sustainable fuels. To manage this, fuel producers and the additive industry must collaborate to deliver sustainable fuels for the coming years. For low-quality fuels, the use of additives is crucial.
Fuel efficiency x less emissions
The combustion of a hydrocarbon-based fuel, regardless of its quality, is never 100% complete. In a complete combustion reaction, the key elements of any fuel – carbon, hydrogen, and oxygen – are converted to carbon dioxide (CO2) and water (H2O). When incomplete reactions occur, carbon monoxide (CO), soot (unburned hydrocarbons), and other chemical variants are generated.
Considering a typical gasoline component (octane), the general reactions are shown below:
- 2C8H18 + 25O2 → 16CO2 + 18H2O + heat↑ ΔH = -10,941.3 kJ/mol
- 2C8H18 + 17O2 → 16CO + 18 H2O + heat↑ ΔH = -6,413.6 kJ/mol
- 2C8H18 + 9O2 → 16C + 18 H2O + heat↑ ΔH = -4,645.1 kJ/mol
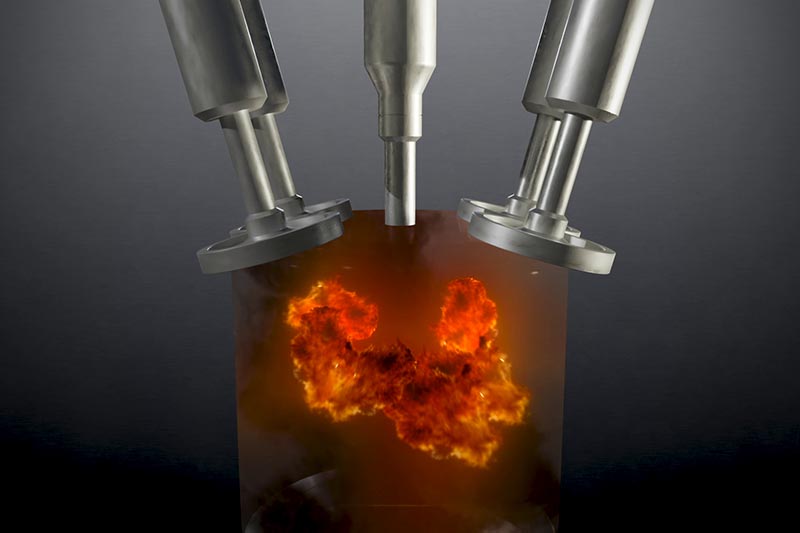
In an internal combustion engine (ICE), these typical reactions occur simultaneously albeit to various degrees depending on the efficiency of the entire system. In a new ICE, where all components are still clean and new, chemical reaction (1) is predominant, and efficient fuel utilization occurs. When engine components begin to foul (form deposits) or wear, chemical reactions (2) and (3) increase their contribution thereby requiring more fuel to perform the same amount of work. As more fuel is consumed, more combustion gases are also emitted, including CO2, which has now become a key concern because of its very significant greenhouse effect resulting in increased global warming. Other emissions also contribute to the “Greenhouse Effect” but nowhere near to the same degree as CO2.
As discussed, the burning of fossil fuels emits greenhouse gases into the atmosphere, which is major a concern. As a result, the focus is on developing alternative energy to power vehicles to reduce greenhouse gas emissions. Alternative fuels are a means to power vehicles. Such alternative fuels include, but not limited to, ethanol, biodiesel, natural gas, and hydrogen fuel cells. The most commonly used “alternative fuels” today are gasoline-ethanol and diesel-biodiesel blends. The main concern for these alternative fuels is their efficiency vs. cost when compared to fossil fuels. The table below shows the typical energy content for several fuels.
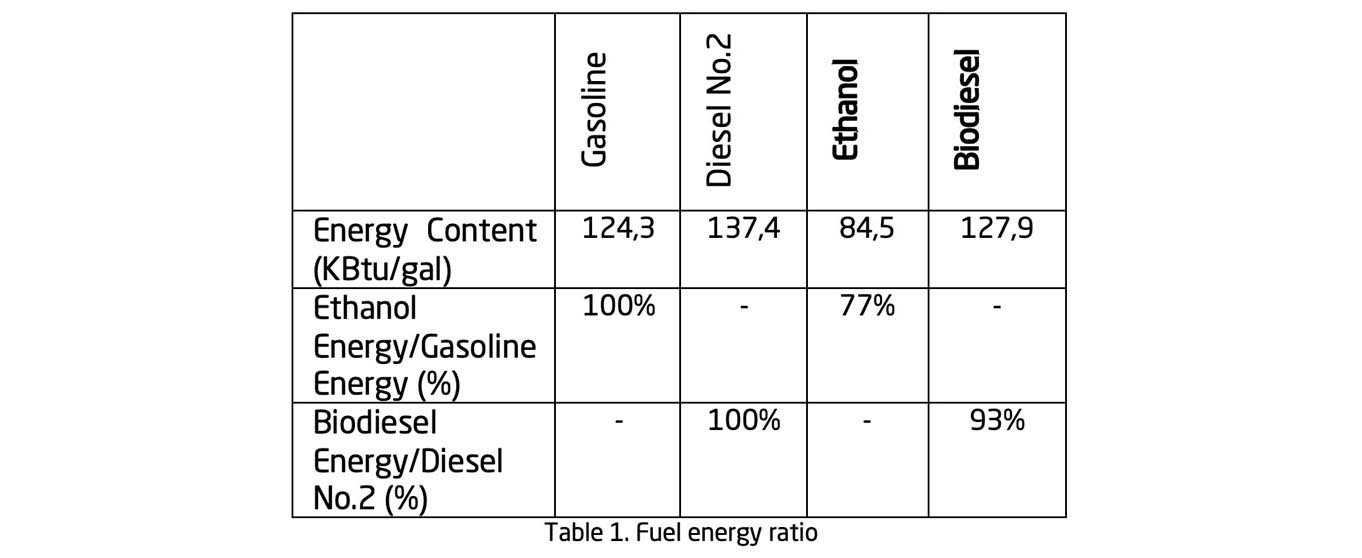
Considering the table above some questions arise.
In countries where the addition of ethanol has become mandatory, as is the case in Brazil, which requires the addition of 27% of anhydrous ethanol to gasoline (E27) , what would be the solution to increase the E27 efficiency while keeping the benefits of reducing emissions provided by ethanol addition?
The addition of biodiesel to diesel No.2 brings other problems such as filter blocking tendency (FBT). In some countries, the use of B30 (a 30% w.t. bio-component blend) is a reality. However, because of the lower energy content, this means less fuel efficiency due to fuel energy reduction as well as potential FBT problems.
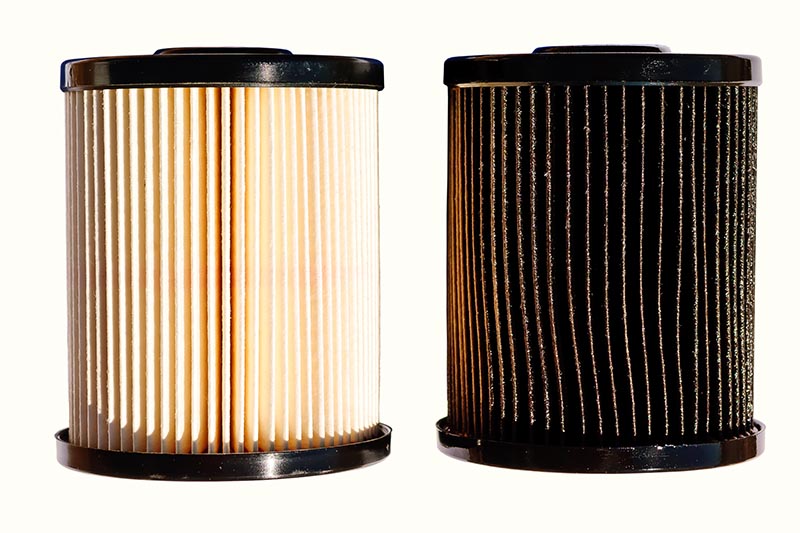
Again, one would question “what can be done to increase fuel efficiency without compromising both energy output and reduced emissions?
In several countries the quality of fuels is very low. It is known that low fuel quality, can result in the delayed opening and closing of fuel injection systems. This causes poor fuel atomization, poor spray formation, and fuel/air mixing. Poor diesel quality can lead to injector deposits and corrosion. The result is “reduced fuel efficiencies and increased emissions”.
Considering all the above, Dorf Ketal’s approach to solve such questions has been through combustion efficiency improvement.
Engine combustion efficiency is the rate at which an engine converts fuel into energy. Several parameters are considered to measure the overall engine combustion efficiency.
- Engine design.
- Electronic fuel injection control system.
- Fuel composition.
- Driving patterns – the manner in which a driver drives (hypermiling).
- The amount of oxygen entering the combustion chamber.
- Exogenous factors, such as poor fuel quality, the degree of cleanliness of the injection system, wear of parts, etc.
By adopting a technology that improves combustion efficiency it is been proven that it is possible to generate significant fuel savings, directly contributing to emissions reduction and improved sustainability. This technology works by allowing a more efficient combustion process that maximizes chemical reaction (1) and minimizes the chemical reactions (2) and (3). More energy is released, thus resulting in greater efficiency, and lower fuel consumption. As a direct consequence, by reducing the amount of fuel needed to perform a given task, lower levels of CO2, CO, and soot emissions are also achieved.
A proven practical solution is the use of performance additives containing “combustion improver” blended with with conventional deposit control additives and friction modifiers. The “combustion improver” approach offers the industry a truly novel route to immediate increased fuel economy and reduced engine out emissions without compromising on performance and driver experience. This technology has been introduced into the market by Dorf Ketal and is rapidly becoming the technology of choice as more and more fuel retailers, fuel blenders and customers alike adopt the approach. The reason is simple, it delivers real life improvements in factors (e) and (f) in the list above.
The following is a list of the mechanisms that act on these factors:
I. Dispersant components, or deposit control additives, as they are also known, act by cleaning and preventing the accumulation of carbon deposits on / within injection systems, engine combustion chambers and other engine components.
II. Friction modifiers reduce friction and prevent wear on piston rings and pistons, thus maintaining engine design efficiency.
III. The Dorf Ketal, “combustion improver” in its most recent generation, is non-metallic and fully organic chemistry. It provides an intelligent distribution of oxygen during the combustion process, thus maximizing equation (1) and reducing the occurrence of equations (2) and (3). This occurs partly due to the increase in the molecular interaction of fuel particles with oxygen by allowing nanometric atomization of the fuel droplets during fuel spraying into the combustion chamber.
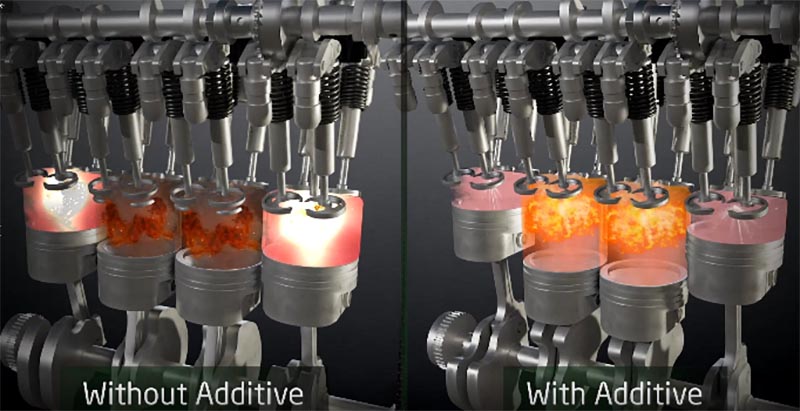
The combination of mechanisms (I), (II), and (III) has resulted, in the reduction of fuel consumption in percentages that vary from 4% to 20% in both bench and real-life applications.
This technological package is already used in Asia Pacific, India, Latin America and Europe. Performance benefits are achieved and not one single failure has been reported.
To support the above, a summary of some of the key testing data that has been generated at both industry leading test-houses as well as from real-life fleet trials follows.
Results
Chassis Dynamometer Tests
The chassis dynamometer tests demonstrate the ability of the fuel additive technology to reduce emissions as a result of improved fuel economy and energy efficiency; this being a direct result of improved combustion performance. The data also shows a significant carbon monoxide reduction. The carbon dioxide emission reduction is relatively proportional to the fuel economy; however, the monoxide emission reduction rate is six times higher on average.

Real-Life Tests
For real-life tests, it is considered that the net fuel economy directly impacts the reduction of emissions, where one can use the mathematical models already developed and validated by the IPCC. Real-life tests are considered the most significant, as they embed in their results several simultaneous mechanisms that contribute positively or negatively to reducing emissions. As part of the Dorf Ketal technology package, a mathematical model was developed to estimate diesel emissions, which calculates CO2, CO, NOx, SOx, Hydrocarbons, and Particulate emissions. The software was developed to support field testing of large fleets of diesel vehicles.
Case Study 1
A fleet of a company located in South America, composed of VOLVO FH 460 trucks, wanted to prove the efficiency of Dorf Ketal’s milEx® branded diesel fuel additives. For this, the company hired a Technology Center that specializes in vehicle performance tests. The first stage of the trial consisted of carrying out tests under controlled conditions in an indoor testing track and a street circuit. Emissions were measured directly using VOLVO’s Dynafleet® system.
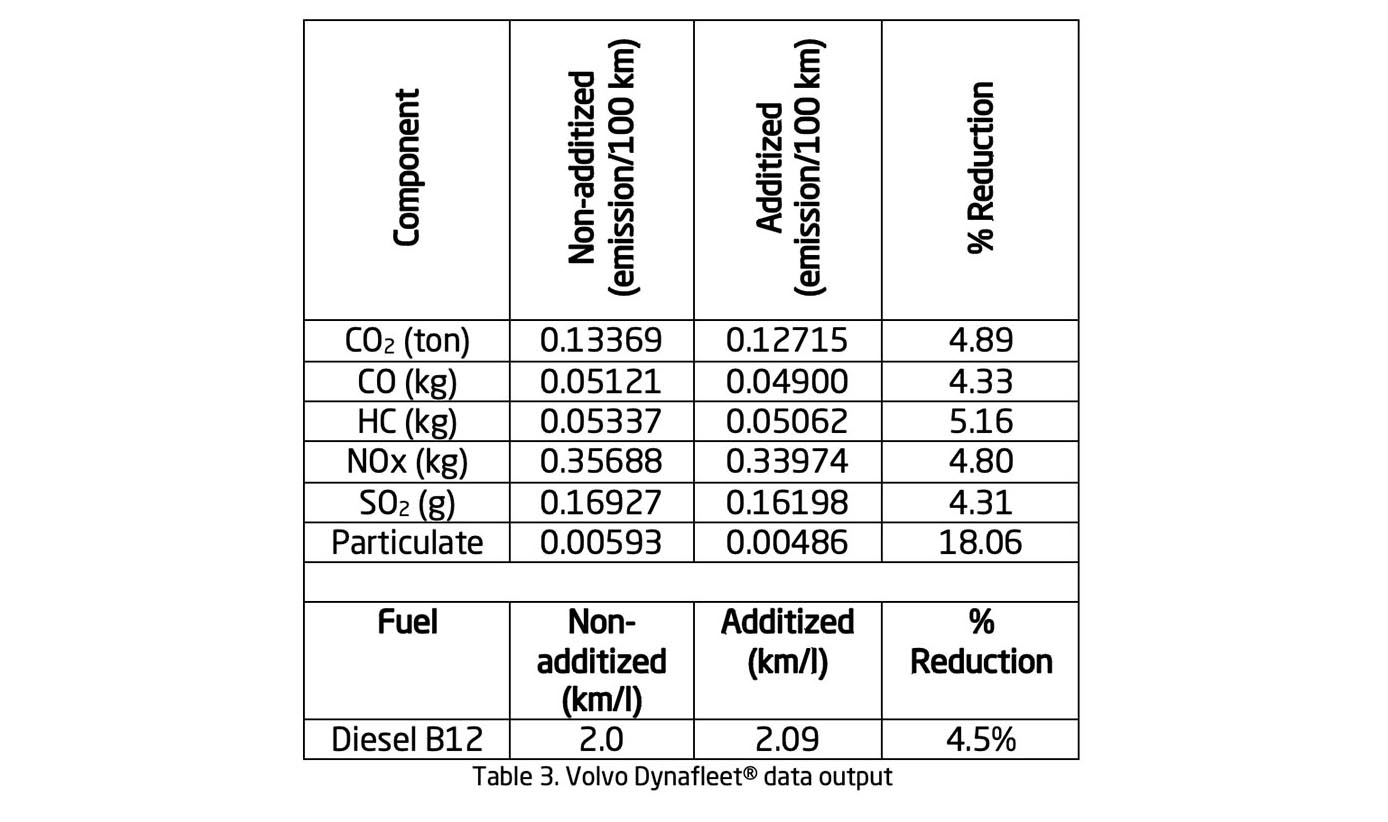
The results obtained in VOLVO’s Dynafleet® system demonstrate real fuel economy directly impacting emissions reduction. The additized diesel delivered an average fuel economy of 4.5% and reduced particulate emissions in the order of 18%, clearly demonstrating that the combustion improver favors chemical reaction (1).
Case Study 2
A major sugar cane company in South America decided to test the efficiency of the of Dorf Ketal’s milEx® branded diesel fuel additive to achieve fuel savings. The company’s Agricultural Division selected 29 trucks according to the table below:
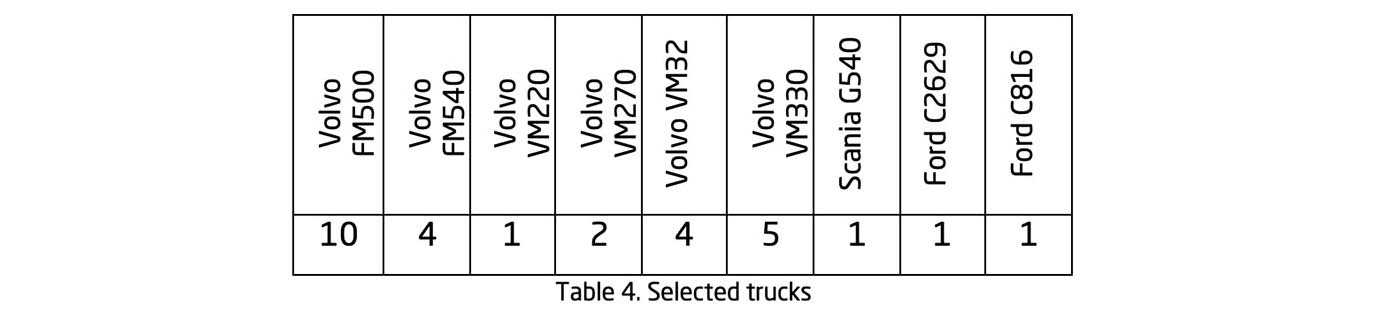
The test was carried out for 30 days, using low sulfur diesel (10 ppm -S10) with 12% biodiesel (B12). The test showed an average fuel economy improvement of 4.3%. The customer reports a monthly consumption of 320,000 liters of S-10 diesel to supply the trucks of this fleet during the harvest season. With milEx additive, a consumption reduction of 13,160 liters/month was estimated. Using the milExCalc™ calculator, this company reduced its emissions footprint according to the table below.

Case Study 3
A major national oil company in Asia intends to additize circa 6 billion liters/year of diesel for the next four years using Dorf Ketal’s milEx® branded diesel fuel additive. After having proven efficiency in fuel economy of around 11,3%, as part of its strategy, it seeks to offer its customers the most efficient diesel to capture marketing benefits associated with the carbon footprint. Based on this base, the contribution to sustainability that this major national company will deliver is shown in the table below.

Conclusions
Maximizing fuel efficiency by using fuel additive chemistry is a low-cost, and now proven, alternative to ensure the long-term market success of fuels.
Dorf Ketal milEx®|mph® fuel additives are proven technologies to support immediate fuel efficiency maximization.
Fuel efficiency maximization using fuel additives impacts positively on reducing emissions contributing to the environmental sustainability.
International and national oil companies and all end-users can make a significant contribution to reducing their environmental impact caused by fossil fuels, and thereby supporting their own sustainability targets by additizing diesel and gasoline with Dorf Ketal’s milEx®|mph® branded fuel additive technologies.
[1] https://www.fuelsandlubes.com/fli-article/hyundai-motor-new-fuels-new-challenges/