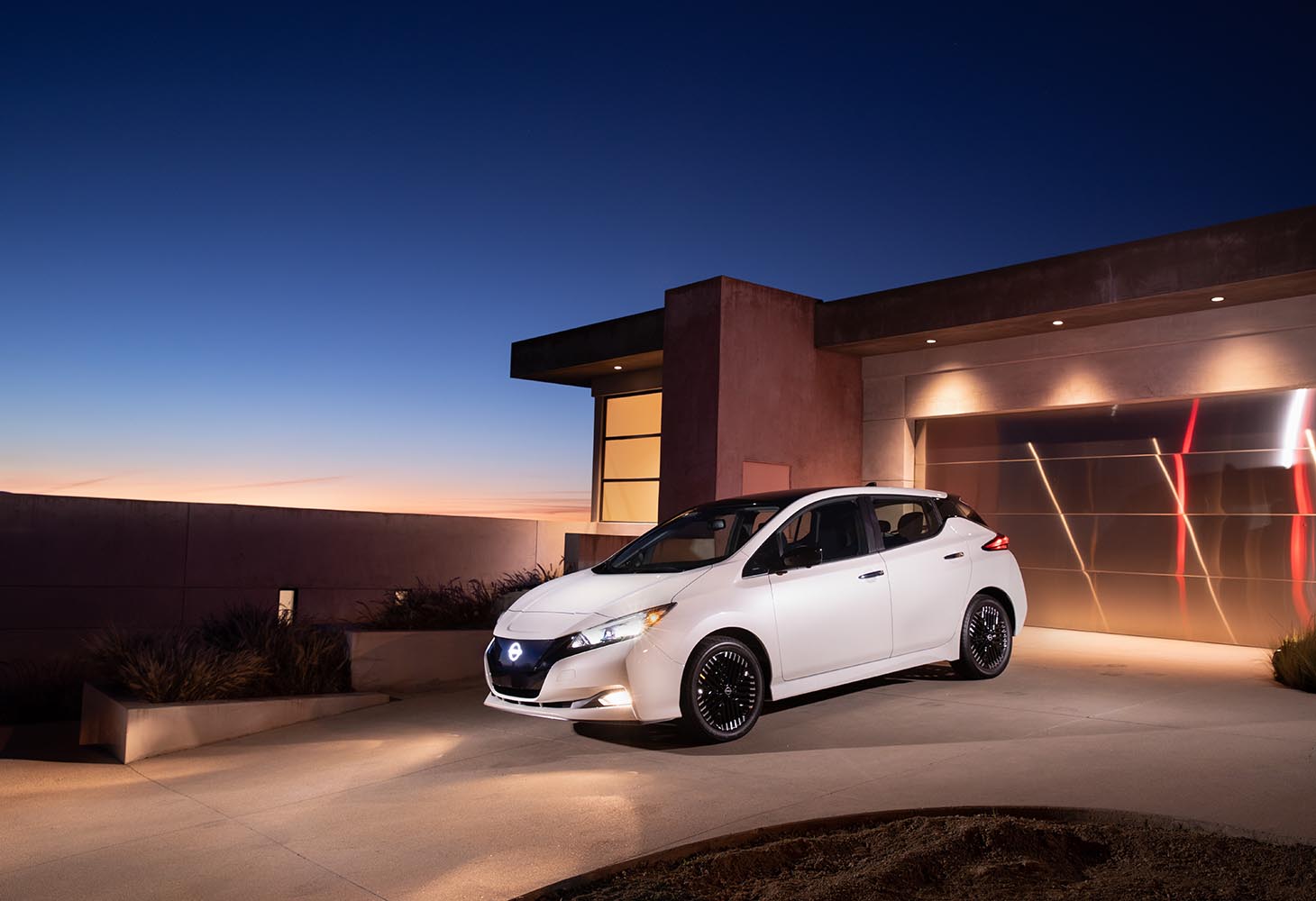
Closing the efficiency gap: Improving electric drive unit performance
Thermal management is critical in the efficient operation of battery electric vehicles (BEVs). Arguably, it is more important in BEVs than in hybrid and internal combustion engine (ICE) vehicles. BEVs generate heat from multiple sources including the battery pack, power electronics, electric motor and onboard chargers, yet the compact nature of electric vehicle (EV) components poses challenges in dissipating the heat effectively. Effective thermal management systems play an essential role in maximising energy efficiency and vehicle driving range, the longevity of power electronics components, enabling fast charging and enhancing passenger comfort.
Dr. Shrikant C. Nagpure is an expert in EV systems. He is currently Cell and Battery head at FEV India Pvt Ltd, a leading engineering and digital mobility company. Its parent company, FEV Group GmbH, is headquartered in Aachen, Germany. During the recently completed F+L Week conference, held in Kuala Lumpur, Malaysia, from June 14-16, Nagpure provided an overview of thermal management aspects for hybrid electric vehicles (HEVs) and BEVs.
Thermal management is more challenging in EVs compared to ICE vehicles, says Nagpure. An ICE typically includes one high-temperature cooling circuit (HT) that considers oil cooling, transmission cooling and air conditioning (A/C). The presence of a heat source (the engine) offers advantages in terms of effectively regulating and maintaining cabin temperatures.
BEVs also have requirements for heating and cooling. However, the operating temperature of the drivetrain is typically lower than a combustion engine. Nagpure outlined the need for low temperature circuits (LT) for the electric motor and power electronics, and controllable connections between LT, the battery, gearbox and A/C circuit. Cabin climatisation is complicated in EVs by the loss of the combustion engine heat source, he says. HEVs require two cooling circuits with different ranges and different temperatures—an HT circuit for ICE and LT for the electric motor and power electronics. This adds further complexity, says Nagpure.
In a BEV, individual vehicle components have differing needs for heating and cooling. These special requirements can impact the location of heat exchanges, cooling, radiators and the aerodynamics of the vehicle. There are many development tasks to understand the desired temperature ranges for the subcomponents—to ensure they maintain the temperature for optimal efficiency, says Nagpure.
The efficiency of electric drive units (EDU) continues to improve. However, Nagpure outlined a 10% efficiency gap between the highly operated regions and the peak efficiencies of e-drives. In a typical drive cycle, the EDU is used within a low/moderate efficient zone, he says.
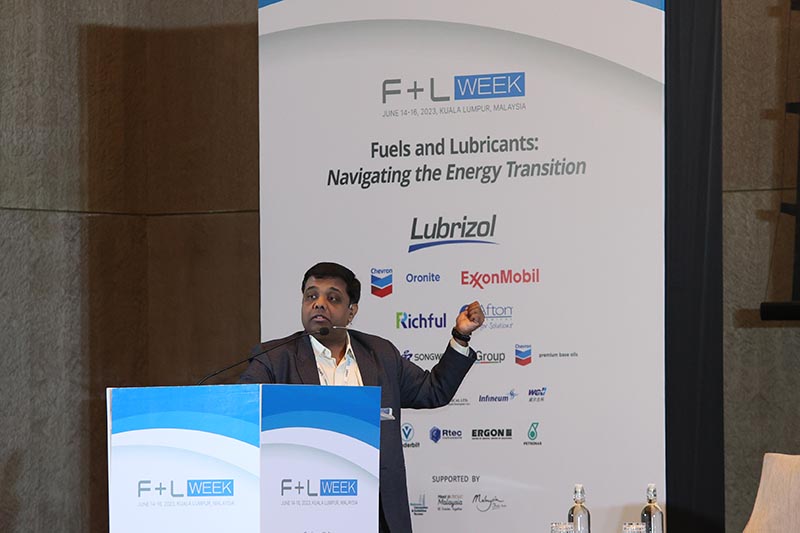
During his F+L Week presentation, Nagpure discussed the key efficiency losses in the electric motors and gearboxes. Electric motor losses largely consist of energy loss in the copper windings and the core, says Nagpure. Copper losses are predominant at lower speeds and high torque, whereas iron losses occur mainly at higher speeds. Losses in the gearbox include bearing, meshing, churning and seal losses, he says. A portion of electrical energy loss becomes heat instead of motive energy.
For battery thermal management, indirect cooling with water-glycol fluids is the most popular approach to cooling. This method will continue to be the most popular method to 2030 and beyond, suggests Nagpure. The FEV representative noted a small but growing application of dielectric immersion cooling, predominantly in large premium cars. The use of refrigerants for battery cooling will decline throughout the current decade.
Development goals in BEVs not only include the cooling of components to ensure they remain below critical temperatures, but also the warming of drivetrain components and batteries during cold start or cold charging events. Nagpure noted several temperature sensitivities of key BEV components determined through laboratory testing. The variable results emphasise the contrasting thermal needs of individual components.
Lay-shaft transmission efficiency is lower when the unit is cold. The transmission efficiency increases with load, says Nagpure. Fewer churning losses were apparent with higher temperatures and lower fluid viscosity. Higher fluid temperatures lead to higher efficiency at all loads, he says.
Electric motor spin loss analysis was undertaken using a demagnetized rotor at 40°C and 60°C. Higher spin losses were recorded at the colder temperatures. However, testing of the electric motor’s efficiency during operation indicated higher motor temperatures lead to lower motor efficiency. Nagpure emphasised the significance of cooling in optimising motor efficiency.
Testing of EDU (motor and gearbox) efficiency during high-load operation showed a quick warming of motor temperature. However, a corresponding increase in oil sump temperature was not evident during sudden load. The efficiency of the EDU decreased as the motor temperature increased over time.
The use of innovative manufacturing designs and thermal management systems has significantly improved e-drive performance and efficiency. Second-generation EDUs have a high level of integration with a 3-in-1 system housing. Gen 2 EDUs have adopted hybrid cooling strategies with dedicated fluids and with e-motor differentiation. In the next generation of EDUs, Nagpure expects higher power densities and the possibility of a single cooling system. Though, advanced solutions such as direct oil-cooled inverters and a split rotor EDU are not easy to implement, says Nagpure.
During his address, Nagpure summarised FEV’s approach to thermal management and cabin climatisation.
Thermal management development must begin in the early concept phase of vehicle development, he says. Nagpure emphasised the importance of simulation tools for development and testing. Computed-aided engineering (CAE) tools, including one-dimensional and three-dimensional computer fluid dynamics, are essential for thermal management optimisation, he says. The process at FEV follows the standard V-cycle including simulation, function development, and validation testing.
Once optimal operating temperatures are known, specialised lubrication and heat transfer fluids are selected. Nagpure emphasised the importance of understanding the properties of fluids to determine the best fluids for efficiency, but also for wear and tear.