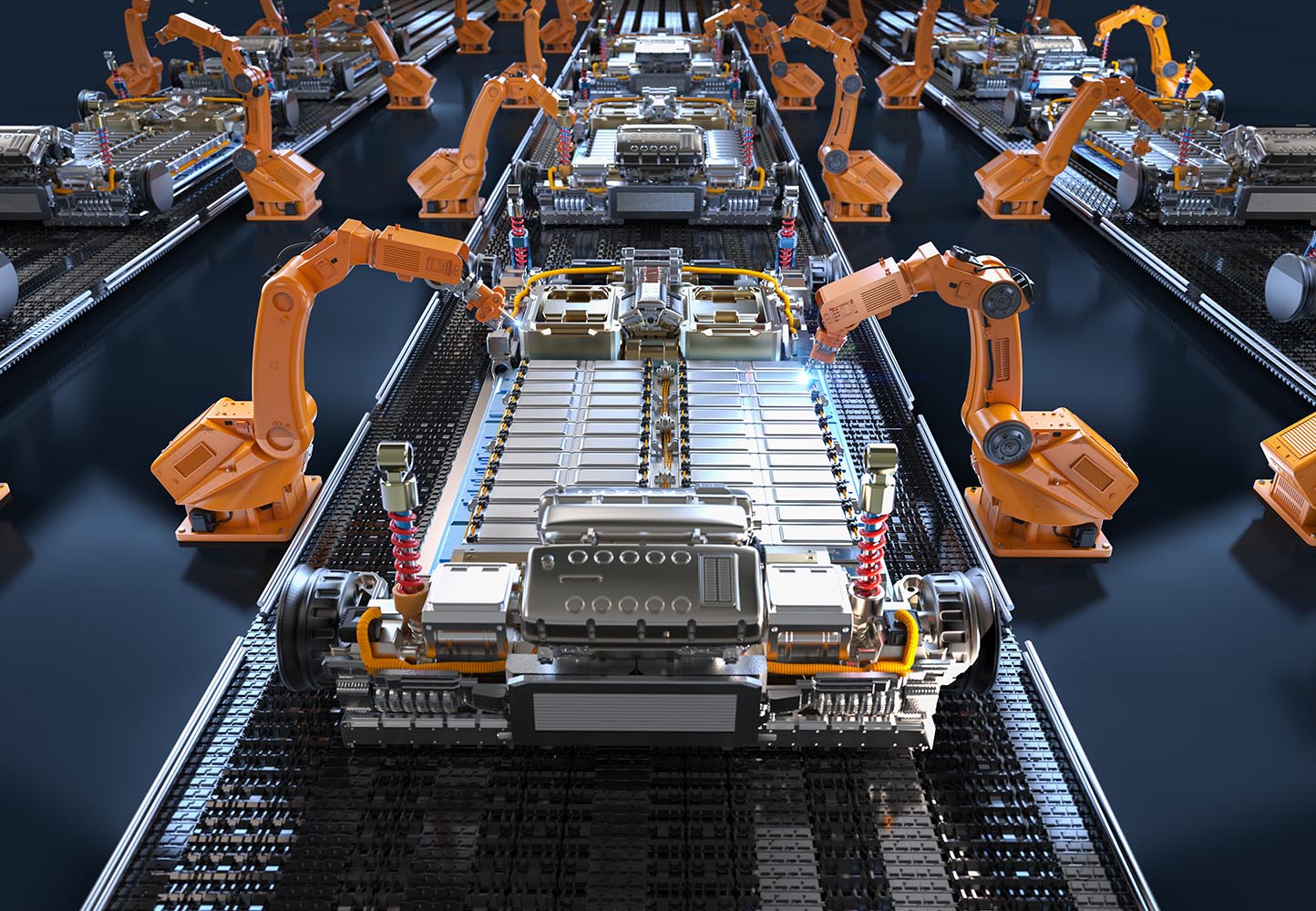
ASTM advances EV coolant specifications amid rapid industry change
One of the preeminent themes of F+L Week 2023, which was held in Kuala Lumpur, Malaysia, in June, was the need for specifications and standardised test procedures to support fluid development in electric vehicle (EV) applications. As previously reported by F&L Asia Ltd., Ravi Tallamraju, chief technology officer at PETRONAS Lubricants International, emphasised the urgency of creating test methods relating to hardware protection, copper compatibility, electrical properties and thermal management.
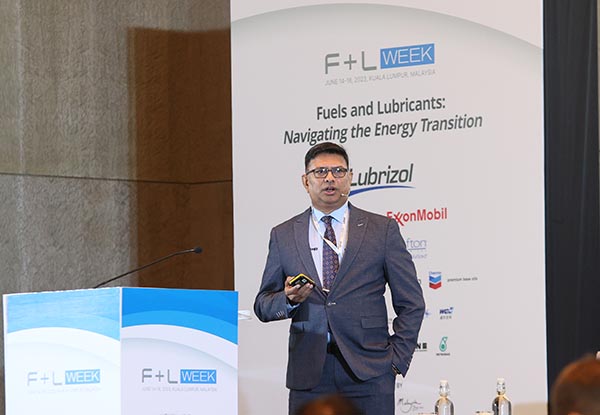
The EV industry continues to evolve at breakneck speed, with more than 60 new electrified vehicle models hitting showrooms around the globe in 2022. Companies that are invested in the development of fluids for EVs are starting to act, developing standards that ensure the requisite quality, safety and efficiency levels.
During F+L Week, Dennis Bachelder, senior engineer in the Engine Oil Licensing and Certification System (EOLCS) at the American Petroleum Institute (API) summarised efforts by API to establish a partnership between OEMs and the lubricant industry to develop fluid performance standards for new energy vehicles (NEV). ASTM International, a voluntary standard-setting organisation based in the United States that operates more than 12,800 standards around the globe, also has several specifications underway for EVs.
F+L Magazine sat down with Allan Morrison of AMT Consulting to discuss ASTM’s progress in producing specifications for EVs. Morrison is a member of multiple ASTM committees, including D15—which has jurisdiction over engine coolants and related chemicals. He is coordinating the development of several EV performance standards at the international standards organisation as a volunteer.
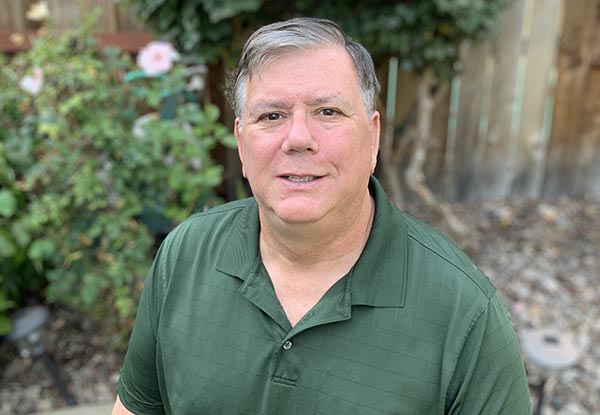
Morrison has a bachelor’s degree in chemistry from California State University of Sacramento and a technical background working in both environmental and automotive products laboratories. He has a long association with ASTM, originally joining in 2003 when employed at the California Department of Food and Agriculture – Division of Measurement Standards (CDFA/DMS).
It was in his work with CDFA/DMS in the D15 committee that Morrison recognised the need for EV coolant specifications. “We started noticing that coolants were coming in that were primary for fuel cell vehicles, but there was no standard for them,” says Morrison. “They would not meet labelling requirements of engine coolants written in state laws,” he says.
His efforts to develop coolant specifications for EVs began “a long time ago”—around 2015. Despite now being semi-retired, Morrison continues his labour of love with the desire to finish what he originally started at CDFA/DMS. “If anything, the need for EV standards has increased,” he says.
Coolants play a crucial role in maintaining a vehicle’s proper operating temperature, dissipating excess heat when required or protecting an engine from freezing in colder weather with antifreeze properties. Coolants also contain additives that inhibit corrosion, which can degrade the performance and longevity of EV components. Coolants need to be specifically designed for the unique characteristics of EVs.
Work has begun on specifications for two types of EV coolants, a glycol-based coolant for fuel cell electric vehicle (FCEV), battery electric vehicle (BEV) and plug-in hybrid electric vehicle (PHEV), and a waterless coolant for BEVs. He also noted the creation of a dedicated ASTM Subcommittee D15.26 Electric Vehicle Coolants to bring everything together.
The original ASTM work item WK52011, specification for glycol-based coolants included four different grades within one standard, each for different uses. While everybody realises that these coolants are necessary, it proved impossible to get consensus, says Morrison. This work item has been split up to ensure the required focus on individual uses. There are now three work items for glycol-based coolant specifications, says Morrison.
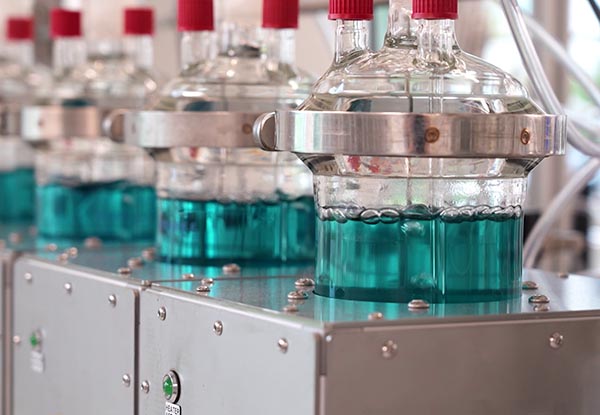
WK87290 is the specification for specialised coolants used in FCEVs. These coolants will have an electrical conductivity requirement of less than 5 microsiemens per cm and require limited corrosion inhibitors.
WK87291 details the requirements for low electrically conductive, fully formulated glycol-based coolants used in BEVs. The low conductivity requirement is to protect the batteries from shorting out in the event of a cooling system failure. These coolants will require non-ionic corrosion inhibitors.
Work on WK52011 continues, although Morrison noted that this is not the highest priority at this time. This standard addresses existing coolants currently being used in most EVs. The specification has no limit on electrical conductivity and can include traditional additives that are included in the bulk of EV coolants currently on the market.
Morrison also outlined two separate waterless coolant specifications that are under development for BEVs. WK80854 is a specification for high dielectric waterless coolants. These coolants are water intolerant at less than 100 parts per million of water. WK87295 is water tolerant up to 2000 parts per million. There is no limitation on the dielectric constant.
Waterless coolants are not very common at this point. However, they are set to play a far greater role in the future. Morrison emphasised the future need for alternative cooling options with the arrival of megawatt chargers for ultra-fast vehicle charging. With a megawatt charger, you can’t use a traditional glycol water coolant, or you will cook the battery, he says. Instead, full immersion systems where the fluid is in contact with electrical conductors may be necessary.
In July 2023, as part of the effort to develop coolant specifications for EVs, D15 published ASTM D8485—a Standard Test Method for Corrosion Test for Electric Vehicle Coolants in Glassware. This simple beaker-type procedure evaluates the effect of glycol-based EV coolants on stainless steel and aluminium, with an option for a copper test specimen.
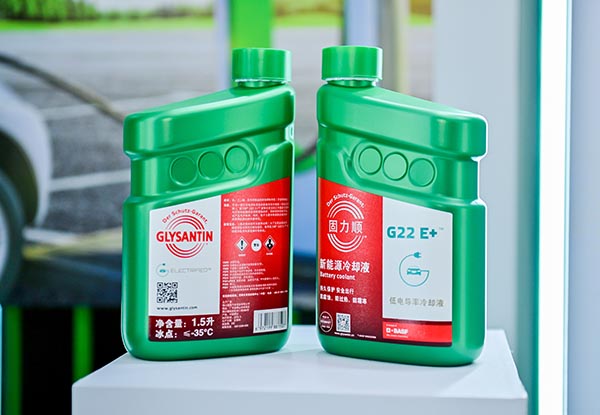
The test method was based on ASTM D1384, a standard glassware corrosion test method that has been used for internal combustion engine (ICE) coolants since the 1950s—with some modifications. The 336-hour test assesses the efficiency of corrosion inhibitors in EV coolants to guard against corrosion.
A second work item WK83561 is a test method for the corrosion of aluminium alloys in EV coolants under heat-rejecting conditions that may be present in the vehicle cooling system. Again, the test is a modification of an existing test method—ASTM D4340. Some of the corrosive elements are removed and the alloys are changed to ensure similarity to EV cooling systems. Basically, the method removes the cast aluminium and employs different alloys of aluminium plate, says Morrison.
WK83561 is currently out for ballot which closes on September 29, 2023. However, the vote has been met with some resistance and Morrison anticipates a failed ballot. While a re-ballot may be required, Morrison believes “we are not far away.” Outstanding issues are mainly procedural at this point, he says. The two test methods are part of a range of new EV specifications that are a work in progress.
One of the common complaints received by OEMs regarding the development of new test methods is the correlation between a bench test and the field. Morrison also highlighted efforts to develop fleet testing for EV coolants, with the potential inclusion of this detail in the upcoming standards. Further discussions on fleet testing will take place during the November D15 meeting in Washington D.C., he says. Although, fleet testing data is not commonly included in industry standards and it is a difficult and expensive exercise.
One of the key aspects of ASTM’s standards, including its test methods, is that they are developed through a voluntary consensus process. At its core, “voluntary consensus” signifies that the standards are established through collective agreement. Industry experts, business representatives, government officials, and even consumers come together to discuss, review, and refine these standards. This collaborative approach ensures that the standards are both technically sound and relevant to real-world applications.