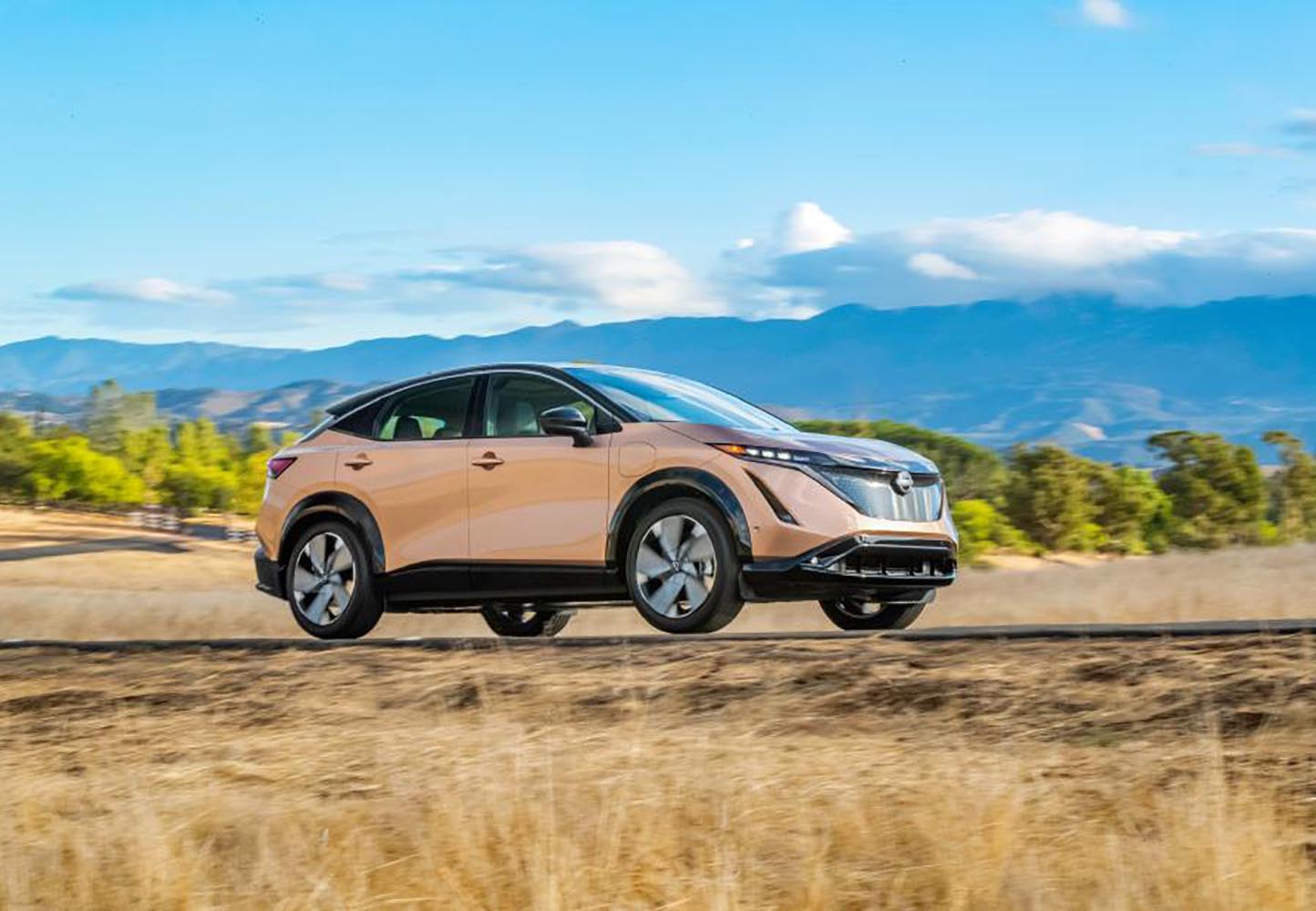
Are electric vehicle applications too diverse for industry standards?
Industry specifications are the cornerstone of the automotive lubricants industry. They provide a framework for manufacturers, ensure fluids consistently meet essential quality criteria, promote interchangeability, drive innovation in response to evolving technologies and support sustainability. As the automotive industry undergoes a monumental shift toward electric vehicles (EVs), industry standards for fluids and lubricants are evolving in tandem.
Oil marketers have recognised the need to adapt their products to cater to this emerging market. Leading manufacturers are pioneering a new era of lubrication tailored to the efficient, high-performance requirements of electric drivetrains and the thermal management needs of EV batteries.
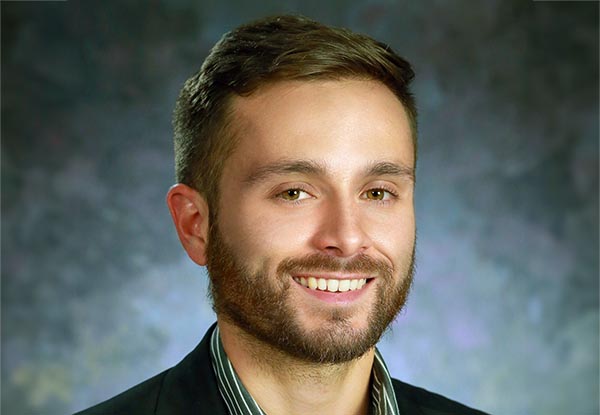
As lubricant manufacturers and OEMs adapt to this new world, there are growing calls for industry standards for EV applications to support the transition. Although, during the 2023 JSAE/SAE Powertrains, Energy & Lubricants International Meeting, held in Kyoto, Japan in August, Ian Smith of Southwest Research Institute (SWRI) questioned whether EV applications are simply too diverse to set industry limits or industry norms—at this time. During an Overview & Remarks of Fluids for Electric Vehicles, Smith noted that there are “lots of unanswered questions and even unknown questions at this point.”
Smith is manager of the electrified powertrain team at SWRI. He leads a group focused on applied research, development, and standard and certification testing in lithium-ion batteries. SWRI is a contract R&D organisation that provides independent services to government and industry clients. In his presentation, Smith discussed EV fluid considerations and properties, with a particular focus on wet motors and battery heating and cooling.
On the surface, EV fluids seem simple compared to the conventional internal combustion engine (ICE). The most challenging part is the thermal management system, says Smith. They consist of many complicated cooling paths, pumps, valves and even different types of fluids.
When it comes to EV motors, the complexity varies depending on whether it is a wet or dry motor. Wet motors typically contain an automatic transmission fluid (ATF) that also lubricates the gear train. In a dry motor, the cooling fluid is separated from the gear train. Power electronics, batteries and cabin comfort usually employ a water-glycol mix. Smith noted industry discussions around the possibility of a unified fluid in the future.
Fluids for EV motors lack the same standardisation as in the ICE. The SWRI representative emphasised a plethora of motor design choices including dry motors, wet motors, integrated inverters, separate inverters, and more. While diversity in light duty is well known, Smith noted significant diversity in heavy duty. The market is growing quickly and changing—and an optimised hardware design hasn’t yet been realised.
Conventional lubricant products developed for very different conditions are commonly used. “There hasn’t been the opportunity to come up with controlled test procedures to develop these EV fluids,” says Smith. Typically, OEMs use an established ATF with small changes to the additive package.
Some guidelines already exist for EV applications. SAE J3200 Fluid for Automotive Electrified Drivetrains was released in October 2022. The standard provides general information about the properties that may be important for electrified drivetrains. The specification discusses electrical properties, heat transfer, oxidation, material compatibility, aeration and more.
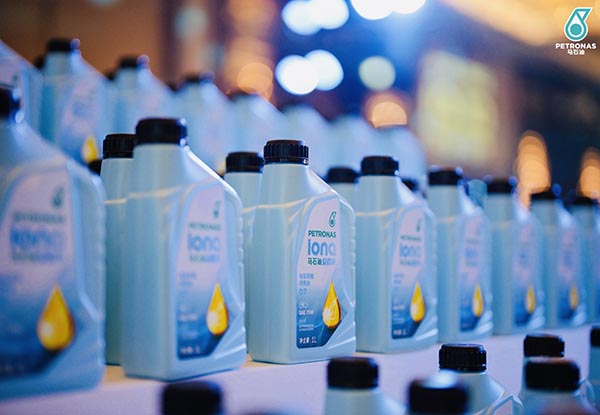
However, it typically doesn’t provide the specific ranges or tolerances that should be used, says Smith. SWRI is actively researching EV properties in a joint industry program, the Advanced Fluids for Electrified Vehicles program (AFEV). AFEV is concentrating on five separate tasks: high-speed durability—as motor speeds continue to push upward, material compatibility, challenges with electrified bearings, heat transfer properties for contact materials, and aeration—which has close links to high-speed durability. This research will help inform standard development and to update existing standards.
Despite the existence of some specifications for EV fluids, there is no true standard detailing the measurement technique for individual properties, says Smith. Many of the tests that have been developed and the limits set are for legacy applications, he says.
EV driveline lubricants need to be durable, as they are fill-for-life applications. Smith emphasised the need for strong oxidation control, heat transfer, thermal and electrical conductivity. Typically, friction control is not as important in an EV, he says. For EV motors, ATFs are a start, but there’s still a lot of research to be done, he adds.
SAE J3073 – Battery Thermal Management was published in 2016 and provides a “nice introduction to the thermal management of batteries,” says Smith. The standard includes design considerations for thermal management, depending on the battery system and the vehicle application. However, it does not describe all types of thermal management systems. References to indirect liquid cooling and heating systems, refrigerant cooling and solid phase change systems are included; but there is no mention of direct liquid battery cooling (immersion cooling).
Even indirect cooling, which is the benchmark for EVs today, contains no standard for the cell form factor or the type of fluid. There is considerable diversity in current system architectures. For example, the Volkswagen ID.3 employs a single cooling plate, the Ford Mach-E uses separate top cooling plates with a central cooling manifold, whereas Tesla has adopted a bottom cooling system using “ribbons.” Indirect cooling is limited in the amount of heat transfer based on the types of thermal interface materials.
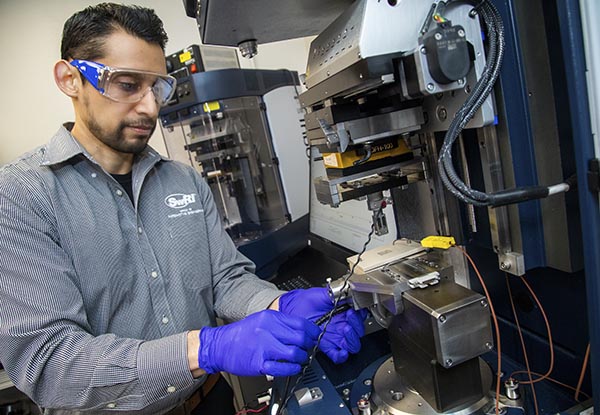
Immersion cooling, where components are submerged into a dielectric fluid with decent thermal conductivity and poor electrical conductivity, is more commonly associated with data centres, cryptocurrency mining and some high-performance computing applications. The cooling method offers up to 100 times improvement in heat transfer compared to indirect cooling, says Smith. In an automotive environment, immersion cooling also has the potential to help in safety and fire propagation, although there are potential negative impacts on weight and packaging.
The technology is being explored in the context of ultra-fast charging infrastructure to manage the heat generated during the rapid EV charging process. Material compatibility, combustibility and heat transfer are key considerations in immersion cooling fluids. OEMs need to ensure batteries maintain their temperature under typical cycling, allow for higher charge or discharge power, mitigate or reduce thermal runaway, and note any implications to battery life. Perhaps the most challenging aspect of immersion cooling is unit variability, with providers often recommending different fluids. Smith also outlined variations in conductivity depending on the fluid’s life, additive packages and base stocks. It’s not yet known what the exact tolerance should be based on battery design, he says.
There are several battery standards, although, Smith notes they are all “somewhat similar” once you dig into them. None of them specifically address immersion cooling. There is a specific standard that SAE recommends for battery safety and abuse, SAE J2464 Electric and Hybrid Electric Vehicle Rechargeable Energy Storage System (RESS) Safety and Abuse Testing. The most recent version was published in 2021.