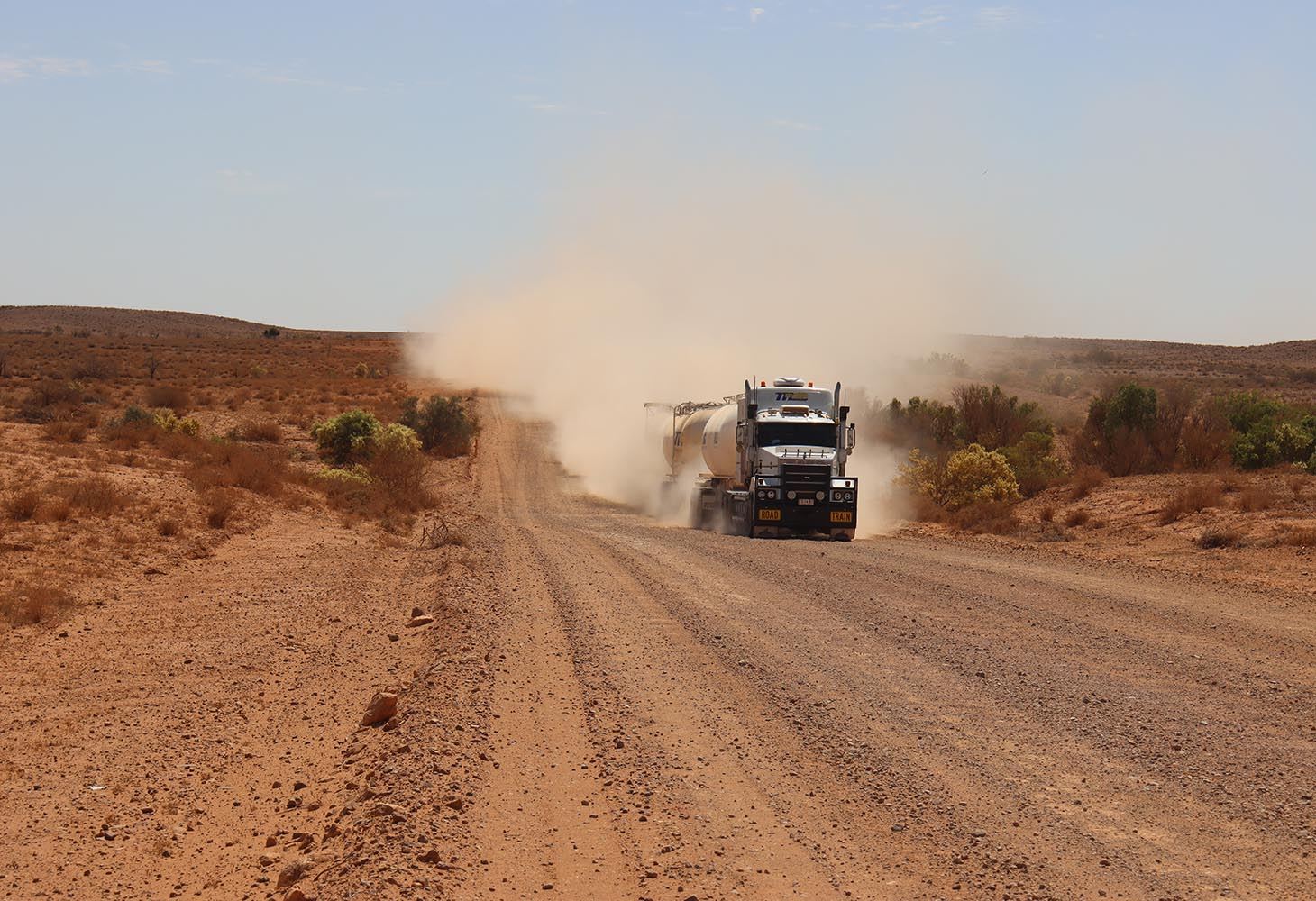
Alternative fuels for heavy-duty off-road applications are ready now
Fueling heavy-duty off-road vehicles is a far more complex exercise than powering personal transportation. Unlike on the road, heavy-duty off-road vehicles don’t “cruise” and fuel at the site. They are engaged in rugged applications, often with strong vibrations, heavy loads and high torques. The vehicles must contend with dirt and contamination, and durability and reliability are of utmost importance. Transitioning these vehicles to more sustainable, alternative fuels pose many challenges for engine designers.
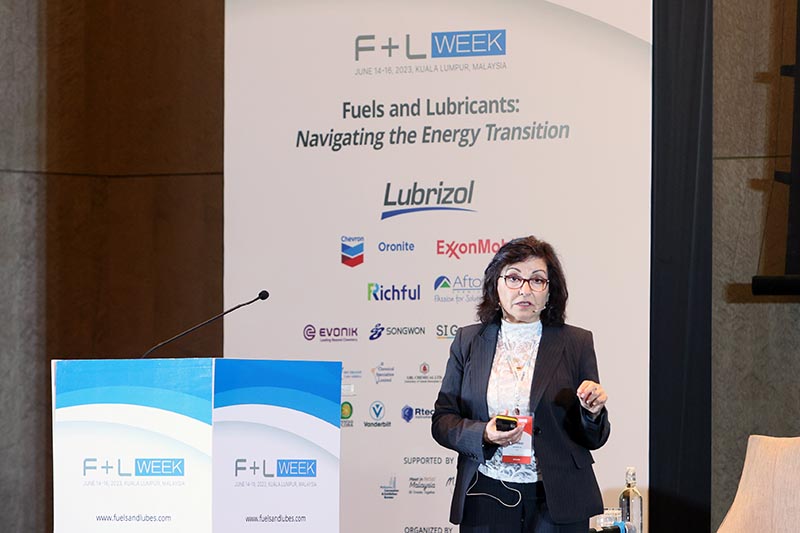
Hind Abi-Akar is senior advisor to the Electrification and Energy Solutions division at Caterpillar Inc., the world’s largest manufacturer of construction equipment and mining equipment, off-highway diesel and natural gas engines, industrial gas turbines and diesel-electric locomotives, based in Irving, Texas, U.S.A. Abi-Akar holds a PhD in Materials Science based on electrochemistry and surface science. During F+L Week 2023, held in Kuala Lumpur, Malaysia from June 14-16, Abi-Akar discussed Fueling Heavy Duty Applications for Energy Transition. In her presentation, Abi-Akar outlined several key engine design considerations relating to alternative fuels.
We focus on the [fuel] availability, says Abi-Akar. Equipment can operate in incredibly remote areas, making transportation of fuels to the work site difficult. If alternative fuels have low energy, not only does this mean carrying more fuel, but it also impacts work time. Fueling and maintenance such as filter changes are rigorously scheduled. “Downtime is costly,” says Abi-Akar.
Various lower carbon fuel options were discussed. The factors that impact the selection of these fuels were highlighted. Energy content of the fuels was one key factor. The storage volumes of renewable diesel, or hydrotreated vegetable oil (HVO), and biodiesel are relatively similar. HVO’s storage volume is 1.04 times the equivalent of diesel energy and biodiesel is 1.1 times. However, methanol requires 2.3 times the storage volume. This is a huge consideration, says Abi-Akar. Hydrogen (H2) requires 10 times the volume—at very high pressures—and requires a different level of expertise for handling. The ability to transport and store a particular alternative fuel dictate its use in the appropriate application.
Abi-Akar also highlighted the importance of materials compatibility of alternative fuels, which can influence component design—such as elastomers, hoses and engine components. Maintenance is critical in fluid technology and the impact of alternative fuels on service intervals also need to be considered, she says.
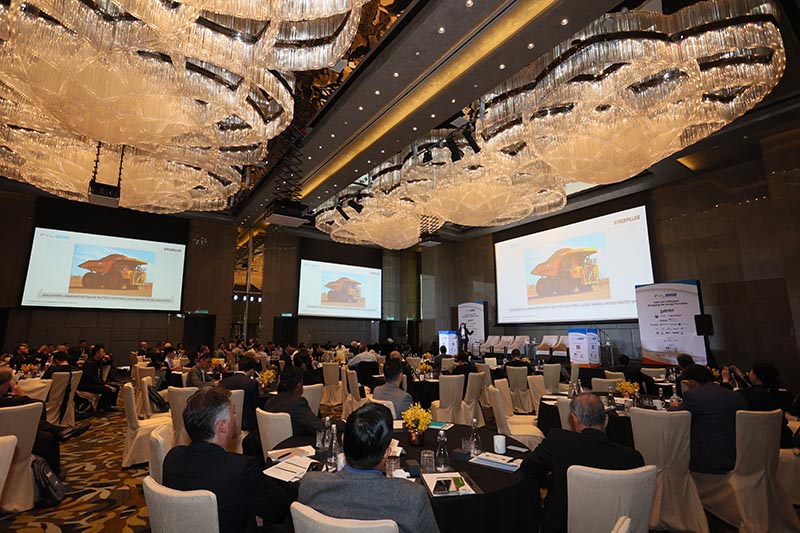
There are several important factors relating to the combustion of new fuels, including the autoignition temperature and its relativity to diesel fuels. Changes to autoignition dictate whether a compression ignition engine is appropriate or if the engine design needs to employ spark ignition— which is not common in diesel engines. Dimethyl ether (DME), a synthetically produced alternative to diesel fuel, has a similar autoignition to diesel fuel, whereas ammonia, methanol and hydrogen autoignition temperatures are much higher, potentially requiring spark ignition. This is a major change, says Abi-Akar.
Flame characteristics are also noteworthy. Significant differences exist between H2 and ammonia for example. Hydrogen is fast burning compared to diesel fuel, which means it can exceed pressure limits, says Abi-Akar. On the other hand, ammonia is slower burning, favouring lower engine speeds. This, however, can result in unburnt fuel—a challenge in a combustion environment.
There are conflicting views around the likely time frame for decarbonising the heavy-duty sector. “In our experience, some of these fuels are ready now,” says Abi-Akar. “Caterpillar encourages customers to use them,” she says. However, there are concerns about fuel supply. In some areas, there can be plentiful supply of a particular lower carbon fuel, but in most regions alternative fuel volumes are low or non-existent. Capacity is growing, but constraints can impact the price, says Abi-Akar. Currently subsidies are important for the final cost of alternative fuels. Costs and supply impact the total cost of ownership. This is a big consideration for Caterpillar and heavy-duty machines’ customers, she says.
During her presentation, Abi-Akar discussed a variety of lower-carbon intensity fuel options. Biodiesel and HVO can be implemented at any time and are miscible with diesel at any blend level. Caterpillar has been using biodiesel since the late 1990s, although she concedes it requires more management and handling than HVO. Caterpillar has certain models that allow blends of up to B100, which tend to be in the lower regulated engine models. If aftertreatment is used, then blends are limited to B20, she says. Abi-Akar also noted the potential role of synthetics. E-diesel is an excellent drop-in solution that can operate at any blend level up to 100%.
Results of testing on HVO using the Caterpillar 3MWe genset were discussed. A slight reduction in full power and transient response was observed compared to diesel fuel. HVO demonstrated half the smoke opacity on transients, and similar nitrogen oxide (NOx) levels, with a slight reduction at lower loads. NOx emissions can vary depending on the load, says Abi-Akar.
Abi-Akar also outlined Caterpillar’s expanding H2 capabilities. Using dynamic gas blending technology, Caterpillar engines can burn a wide range of fuels/H2 blends. The G3516H engine is currently available as a 100% hydrogen-capable demonstrator. The company is focused on expanding its H2 capabilities, she says.
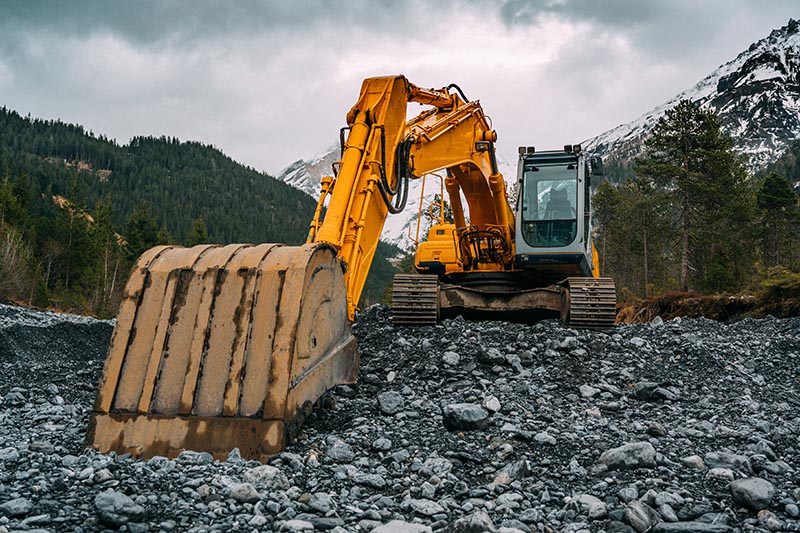
Methanol allows liquid storage in standard conditions and offers similar handling to gasoline. It is also relatively energy dense, compared to hydrogen and batteries, with multiple paths to renewable production. Methanol is widely available today as a commodity chemical and can offer a lower environmental impact due to its biodegradability. However, existing feedstock is natural gas or coal, requiring a shift to biomass and excess renewable electricity moving forward. Abi-Akar outlined various fuel injection strategies to allow use of methanol in heavy duty engines.
As part of its commitment to sustainability, Caterpillar is investing in a range of advanced power technology options, says Abi-Akar. An increasing use of lower-carbon intensity fuel and hydrogen blends is being used in existing field assets to make them more efficient and fuel flexible. There are also efforts to couple established power sources with new technologies, including electric and hybrid powertrains and the use of electric drive transmissions with power components. The equipment manufacturer is integrating renewable energy sources into electric power systems, with Abi-Akar noting the role of small-scale independent power grids (microgrids) to bring solutions to the customer.
Abi-Akar also underlined end-users’ concerns about the impact of alternative fuel use on equipment warranties. The Caterpillar representative reassured participants that the use of consumables, including fuels, do not void warranties. However, Caterpillar, and in general OEMs, warrant workmanship and materials and not issues resulting from the use of consumables, she says.
Finally, Caterpillar detailed efforts to replace established power sources with batteries, stored electrical energy, fuel cells and renewable hydrogen fuel. However, Abi-Akar emphasised that there is not one single solution. A variety of solutions and lower carbon intensity fuels are needed based on differing applications, regions, and availability. There will be challenges in infrastructure, distribution and customer education, she says, calling on various stakeholders for a high level of collaboration.