
Electric vehicle fluids: More questions than answers
Driven by political incentives and regulations, electric vehicles (EVs) are poised to disrupt the incumbent internal combustion engine (ICE). We are witnessing increasingly rapid movement by original equipment manufacturers (OEMs) to develop and commercialise EVs, alongside reductions in research and development (R&D) budgets for fossil fuel-powered vehicles.
EVs might feel like the new kid on the block that is curtailing our long love affair with combustion engines. However, EVs have a long and storied history. Robert Anderson developed the first, albeit crude, EV in 1832. Electric powertrains became very popular in the early 1900s, accounting for around one-third of all vehicles on the road. Advocates enjoyed the relative hush of the vehicles compared to their noisy steam and gas counterparts, as well as the absence of smelly pollutants.
Yet, the heyday of the EV was short-lived, upended by the arrival and mass production of Henry Ford’s Model T. Abundant gasoline and continued improvement in the ICE offered little opportunity for alternative fuel vehicles throughout the 20th century.
The first serious alternative to the ICE was when the Toyota hybrid system was introduced in 1997. Fast forward 25 years and we are observing a dramatic increase in EV products in a revolutionary shift not seen for over a century.
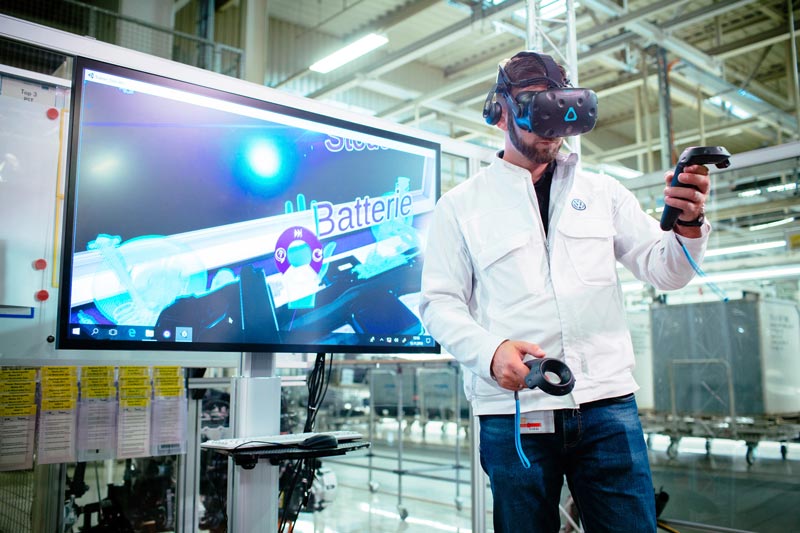
The second coming of EVs brings with it new and unique demands on the automotive lubricants required to ensure optimum operation. Formulation for EVs is complicated, with multiple vehicle types and, to date, there is a relative lack of knowledge on the associated lubricant challenges.
The Society of Tribologists and Lubrication Engineers (STLE) is a non-profit technical society for the tribology and lubrication engineering sectors. The U.S.-based organisation has recognised the dearth of published information about the growing EV lubrication challenges. The technical society held the inaugural Tribology and Lubrication for E-Mobility Conference in San Antonio, Texas, U.S.A., in November 2021 to expand industry knowledge on the topic.
In May 2022, STLE published a white paper on Tribology and Lubrication for E-Mobility. The paper, compiled by Dr. Neil Canter, shared the key findings of the STLE EV conference and summarised the current state of knowledge on the tribology of EVs.
Battery electric vehicles (BEV) have far better efficiency than their ICE counterparts. In the STLE white paper, Professor Ali Erdemir of Texas A&M University indicated the efficiency of a BEV is 3.4 times greater than an ICE. “The number of moving components is greatly minimised in BEVs. There are fewer components to consume energy, which leads to fewer frictional losses,” he says. Dr. Yungwan Kwak, of Afton Chemical, also suggested that some OEMs are questioning the sustainability value of hybrid electric vehicles—where a combustion engine continues to be employed alongside an electric motor.
Unfortunately, fewer moving parts don’t necessarily translate into easier lubricant formulation. The tribology has become more important, suggests Erdemir. “The remaining inefficiencies in a BEV are mostly due to inadequate tribology,” he says.
The STLE white paper highlighted several new challenges in formulating for an electric environment, including electrical breakdowns and heat/thermal management. Erdemir called for the establishment of a new sub segment in STLE called “electrotribology” to address the interaction between fluids and moving parts in an electrified environment.
Kwak outlined the primary lubricant challenges facing electric transmission fluids including cooling, antiwear, bearing reliability, efficiency and material compatibility. There is a need for better lubricants, with low-friction characteristics and improved compatibility with electric components.
The white paper offered a perspective on base stock selection for EVs which need to be dielectric, non-conductive and resistant to electrical breakdown, even at high voltages. A broad range of potential options includes mineral oil, aromatic, poly alpha olefin (PAO), silicate ester, silicone and fluorocarbon. Energy efficiency and heat transfer are the two parameters strictly controlled by base stock selection.
STLE outlined moves by OEMs to simplify vehicle architecture and combine the electric motor, reduction gear and power electronics into a compact integrated electric drivetrain unit—which will encourage a shift to higher voltages and power densities in the future. A careful balance of tribological properties of lubricants is necessary to lubricate gears, bearings and potentially clutches —as well as thermal management for electric motors, windings and other electrical components. Low-viscosity base stocks provide the best opportunity to achieve these objectives.
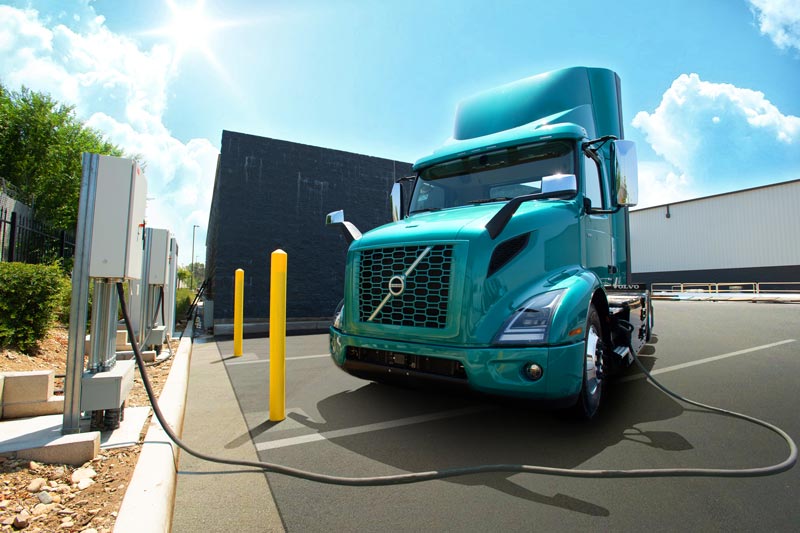
Dr. Gareth Moody of Croda Europe Ltd noted that esters are “particularly effective due to their oxidative stability, electrical properties, thermal conductivity and biodegradability.” A comparison to Group III and PAO base stocks demonstrated a higher breakdown voltage from esters—or the dielectric fluid’s ability to withstand electrical stress. Dr. Ken Hope of Chevron Phillips Chemical Co. outlined concerns related to the high-temperature properties and biodegradability of aromatics and also indicated that silicate esters are not hydrolytically stable. Dr. Babak Lotfi of ExxonMobil Chemical suggested that novel PAOs hold strong potential for maximising the performance and range of EVs due to their low viscosity, low volatility and superior tribological properties.
It is important to achieve a compromise between insulation and conductivity with base stocks, suggests Dr. Steffen Gläenzer of Clariant. If the insulating effect is too high, it can cause excessive bearing damage. Conversely, low insulation can cause electrostatic charge build-up, he says.
Consumers’ expectations of rapid EV charging and extended vehicle ranges are leading to challenges in thermal management. The required increase in power density and reductions in charge time increase the heat load that must be removed, says Dr. Andrew Richenderfer of The Lubrizol Corp.
Thermal conductivity, specific heat, density and viscosity are the four fluid properties that affect heat transfer, suggests Richenderfer, with the lowest viscosity lubricants exhibiting the best heat transfer. A shift to a single unified electric fluid is under consideration alongside OEM vehicle hardware changes. To do so, manufacturers must resolve the vastly different cooling needs of electric motors and batteries.
Low-viscosity fluids are more effective at heat transfer, however, they can produce detrimental impacts on friction and wear. “Moving to low-viscosity fluids will present challenges, especially with gear and bearing performance,” says Dr. Hitesh Thaker of Infineum USA.
Professor Dr.-Ing. Karsten Stahl of the Gear Research Center (FZG) at the Technical University of Munich discussed promising research into water-soluble poly alkylene glycols (PAGs) that contain 30%-50% water as an EV lubricant. Stahl highlighted the coefficient of friction levels below 0.01 in twin disk testing on PAGs, which is in the realm of superlubricity. However, Stahl also noted that the approach is not ready for commercial production due to concerns around rusting of bearings, fluid volatility and the lack of information on long-term impacts.
Ian Smith of Southwest Research Institute believes that immersion cooling, where the battery is completely submerged in a dielectric fluid, has widespread application in EVs. The heat transfer method is 50-100 times more effective than indirect cooling and enables the use of higher power density battery packs. Immersion cooling comes in single and dual phases, though, Richenderfer noted regulatory, cost and environmental concerns when using two-phase fluids.
The white paper also discussed the need for new approaches to bearings due to differences in ICE and BEV hardware architecture. Heavy battery packs are driving a higher gross axle weight rating (GAWR) or load on the axles. “Currently available wheel-end bearings used in ICEs are not usable in BEVs due to the higher axle rating,” says Dr. Ryan Evans of The Timken Co. A lower centre of weight in the vehicle will also impact wheel bearing designs, with changes in ball bearing and tapered roller bearing design required.
The white paper discussed the need for changes in grease formulation, including higher viscosity greases, potentially with non-standard extreme pressure/antiwear. Antioxidants may also be required due to higher loads and viscosity requirements, says Evans. Dr. Farrukh Qureshi of The Lubrizol Corp., one of the knowledge leaders referenced in the STLE document, says more research is required to better understand the lubrication of bearings and gears in EVs.
The introduction of new and different materials has raised significant concerns about material compatibility. Lubricants must not cause corrosion or degradation on interaction with copper windings in electric motors—either through conductive layer deposition or deterioration. Copper wire is generally protected by coatings, but imperfections can expose the copper to the lubricant. Rosemary Ran of Shell (Shanghai) Technology Ltd. indicated that in testing, one lubricant with the best copper corrosion performance failed the FZG test, which evaluates fluid lubricating and wear protection properties at the interface of a loaded set of gears. “The challenge is how to balance copper corrosion, FZG, friction, load and viscosity,” she says. Limitations of the standard test to evaluate corrosion, the copper strip test (ASTM D-130) were also addressed.
It’s not only the fluids in the EV that need to be considered. A significant reduction in parts in EVs will also impact the requirement for industrial lubricants during manufacturing. The STLE white paper anticipates a significant decline in industrial lubricants—such as metalworking fluids, machine lubricants and die release agents—as EV production accelerates. The changes will not be linear, says Canter, however lubricant companies and their raw material suppliers need to be ready, as it may happen quicker than expected.
With the impending boom in EV production, industry stakeholders are calling for the development of EV testing classifications, with some experts noting EV failures were occurring and no testing was in place to get to the root cause of these issues. Dr. Michael Miller of Southwest Research Institute called for testing protocols to be created for four types of lubricants and fluids: power-drivetrain fluids, greases, engine oil (for HEV) and coolants. The process is underway, with SAE J3200™ — Electric Drivetrain Fluids (EDF), which is currently under development. To be published as an SAE Information Report either in late 2022 or early 2023, SAE J3200 will assist those concerned with lubricants used in drivetrain components powered by electric power plants.